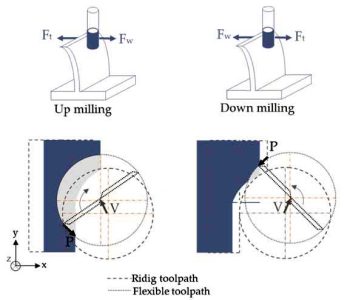
CNC 가공 얇은 벽 캐비티 기술
CNC 가공 중에 알루미늄 부품 및 알루미늄 캐비티 부품이 변형됩니다.. 이전 섹션의 이유 외에도, 실제 작동 중, 수술방법도 매우 중요합니다.
1. CNC 가공 공차가 큰 캐비티 부품의 경우, 가공 공정 중 더 나은 방열 조건을 유지하고 열 집중을 피하기 위해, 가공 중에 대칭 가공을 사용해야 합니다.. 900mm 두께의 시트를 800mm로 가공해야 하는 경우, 한 쪽을 밀링하고 다른 쪽을 즉시 밀링하는 경우, 최종 크기는 한 번에 처리됩니다., 평탄도는 50mm에 도달합니다.; 반복 이송 대칭 처리를 사용하는 경우, 각 면은 최종 크기로 두 번 처리됩니다., 평탄도는 0.3mm까지 보장됩니다..
2. 알루미늄 시트 부품에 공동이 여러 개 있는 경우, 가공 중에 캐비티별 순차 처리 방법을 사용하는 것은 바람직하지 않습니다., 부품에 고르지 않은 응력과 변형이 발생할 가능성이 높기 때문입니다.. 다층 처리가 채택됩니다., 각 레이어는 가능한 한 모든 캐비티에 동시에 처리됩니다., 그런 다음 다음 레이어를 처리하여 부품에 균일한 응력을 가하고 변형을 줄입니다..
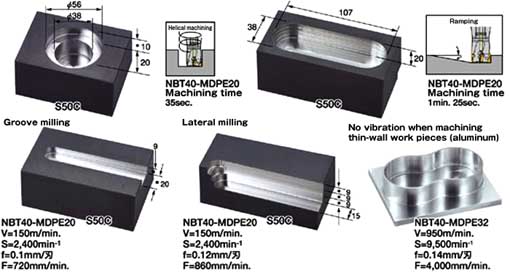
벽이 얇은 알루미늄 공작물 밀링
3. 절단량을 변경하여 절단력을 줄이고 열을 절단합니다.. 절삭량의 3요소 중, 절단 두께는 절단력에 큰 영향을 미칩니다. 가공 여유가 너무 큰 경우, 한 패스의 절삭력이 너무 큽니다., 부품을 변형시킬 뿐만 아니라, 뿐만 아니라 공작 기계 스핀들의 강성에 영향을 미치고 공구의 내구성을 저하시킵니다.. 절단두께가 감소된 경우, 생산 효율성이 크게 저하됩니다.. 하지만, CNC 가공의 고속 밀링은 이 문제를 극복할 수 있습니다.. 절단 두께를 줄이면서, 그에 따라 피드가 증가하고 공작 기계의 속도가 증가하는 한, 가공 효율성을 보장하면서 절삭력을 줄일 수 있습니다..
4. 칼의 순서도 주의해야 합니다.. 황삭 가공은 가공 효율성 향상과 단위 시간당 제거율 추구를 강조합니다.. 일반적으로, 업사이드 밀링을 사용할 수 있습니다.. 그건, 블랭크 표면의 과잉 재료는 가장 빠른 속도와 최단 시간으로 제거됩니다., 마무리에 필요한 기하학적 윤곽이 기본적으로 형성됩니다.. 마무리의 강조점은 높은 정밀도와 높은 품질입니다., 다운 밀링을 사용해야 합니다.. 다운밀링시 커터날의 절삭두께가 최대치에서 0까지 점차 감소하기 때문에, 가공 경화 정도가 크게 감소합니다., 동시에 부품의 변형 정도가 감소됩니다..
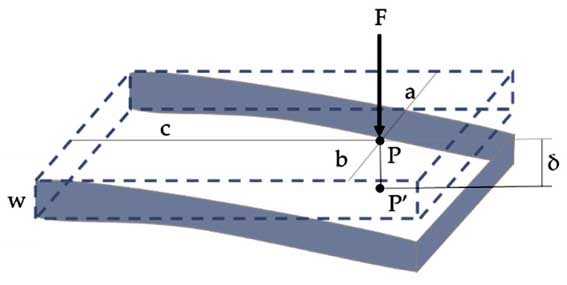
벽이 얇은 알루미늄 캐비티의 절단 순서
5. 벽이 얇은 알루미늄 캐비티 공작물은 가공 중 클램핑으로 인해 변형됩니다., 그리고 마무리하는 도중에도 피할 수 없는 일이다. 가공물의 변형을 최소화하기 위해, 마무리 공정이 최종 크기에 도달하기 직전에 클램핑 및 프레싱 부품을 느슨하게 할 수 있습니다., 공작물을 원래 상태로 자유롭게 복원할 수 있도록. 그런 다음 살짝 고정하고 압축합니다., 공작물을 클램핑할 수 있는 한 (완전히 손으로), 이상적인 가공 효과를 얻을 수 있도록. 요컨대, 클램핑 힘의 작용 지점은 지지 표면에서 가장 좋습니다., 고정물의 클램핑력은 작업물의 강성이 좋은 방향으로 작용해야 합니다.. 공작물이 느슨해지지 않도록 보장하는 전제하에, 클램핑 힘이 작을수록, 더 나은.
6. 캐비티가 있는 알루미늄 부품을 가공할 때, 드릴처럼 밀링 커터를 부품에 직접 삽입하지 마십시오.. 결과적으로, 밀링 커터의 칩 보유 공간이 충분하지 않습니다, 그리고 칩 제거가 원활하지 않습니다, 부품 과열 등의 불리한 현상이 발생합니다., 확장, 도구 붕괴 및 도구 파손. 첫 번째, 밀링 커터와 같은 크기 또는 한 크기 더 큰 드릴로 구멍을 뚫습니다., 그런 다음 밀링 커터로 밀링합니다.. 대안으로, CAM 소프트웨어를 사용하여 나선형 절단 프로그램을 생성할 수 있습니다..
알루미늄 부품의 가공 정밀도와 표면 품질에 영향을 미치는 주요 요인은 해당 부품을 가공하는 동안 변형이 발생하기 쉽다는 것입니다., 운영자에게 특정 운영 경험과 기술이 필요합니다..