CNC 가공 중 알루미늄 합금 부품이 변형되는 데는 여러 가지 이유가 있습니다., 그리고 조작 방법도 실제 조작의 이유 중 하나입니다. 다음, 알루미늄 합금 부품의 CNC 가공 제조업체는 알루미늄 합금 부품 가공의 운영 기술을 간략하게 소개합니다..
(1) For parts with large milling allowances, in order to have better heat dissipation conditions during processing and avoid heat concentration, symmetrical processing should be used during processing. 90mm 두께의 알루미늄 시트를 60mm로 가공해야 하는 경우, if the other side is milled immediately after milling all the margins on one side, and the final size is processed at one time, the flatness can only reach 5mm; If symmetrical processing with repeated feeds on two sides is used, 각 면은 최종 크기로 두 번 처리됩니다., which can ensure a flatness of 0.3mm.
(2) 절단량을 변경하여 절단력을 줄이고 열을 절단합니다.. 절삭량의 3요소 중, 절단 두께는 절단력에 큰 영향을 미칩니다. If the milling allowance is too large, 한 패스의 절삭력이 너무 큽니다., 부품을 변형시킬 뿐만 아니라, 뿐만 아니라 공작 기계 스핀들의 강성에 영향을 미치고 공구의 내구성을 저하시킵니다.. 절단두께가 감소된 경우, 생산 효율성이 크게 저하됩니다.. 하지만, high-speed milling is used in CNC machining, which can overcome this problem. 절단 두께를 줄이면서, 그에 따라 피드가 증가하고 공작 기계의 속도가 증가하는 한, 가공 효율성을 보장하면서 절삭력을 줄일 수 있습니다..
(3) If there are multiple cavities on the aluminum plate part, 가공 중에 캐비티별 순차 처리 방법을 사용하는 것은 바람직하지 않습니다., as this will easily cause uneven stress and deformation of the parts. 다층 처리가 채택됩니다., 각 레이어는 가능한 한 모든 캐비티에 동시에 처리됩니다., 그런 다음 다음 레이어를 처리하여 부품에 균일한 응력을 가하고 변형을 줄입니다..
4) The thin-walled aluminum alloy workpiece is deformed due to the clamping of the fixture during CNC machining. Even finishing is unavoidable. 가공물의 변형을 최소화하기 위해, you can loosen the clamp before the finishing process reaches the final size, so that the workpiece can be restored to its original shape freely. Then lightly compress it to the extent that it can just clamp the workpiece, 이상적인 가공 효과를 얻을 수 있도록. 요컨대, 클램핑 힘의 작용 지점은 지지 표면에서 가장 좋습니다., and the clamping force should act in the direction where the rigidity of the workpiece is good. Under the premise of ensuring that the workpiece does not loosen, 클램핑 힘이 작을수록, 더 나은.
(5) The CNC cutting sequence should also be paid attention to. 황삭 가공은 가공 효율성 향상과 단위 시간당 제거율 추구를 강조합니다.. Rough machining can generally be upside milling. 그건, 블랭크 표면의 과잉 재료는 가장 빠른 속도와 최단 시간으로 제거됩니다., 마무리에 필요한 기하학적 윤곽이 기본적으로 형성됩니다.. 마무리의 강조점은 높은 정밀도와 높은 품질입니다., so down milling should be used. 다운밀링시 커터날의 절삭두께가 최대치에서 0까지 점차 감소하기 때문에, 가공 경화 정도가 크게 감소합니다., 그리고 동시에, the degree of deformation of the parts is reduced.
(6) When CNC machining aluminum parts with cavities, try not to let the milling cutter plunge directly into the part like a drill. This leads to insufficient chip holding space of the milling cutter, unsmooth chip removal, and unfavorable phenomena such as parts overheating, 확장, tool collapse, and tool breakage. 첫 번째, drill the hole with a milling cutter of the same size as the milling cutter or one size larger, and then use the milling cutter to mill. 대안으로, CAM 소프트웨어를 사용하여 나선형 절단 프로그램을 생성할 수 있습니다..
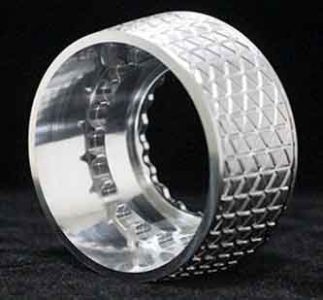
알루미늄 합금 부품의 터닝 및 밀링 기술