Numerical control processing integrates drilling, ಗಿರಣಿ, ತಿರುಗುತ್ತಿದೆ, ನೀರಸ, ರೀಮಿಂಗ್, tapping and other processes into a whole, which requires high technical quality of technicians. A true CNC master should have not only a wealth of theoretical level, but also superb practical experience and practical ability. ಸಾಮಾನ್ಯವಾಗಿ ಹೇಳುವುದಾದರೆ, it will take at least 6 years to become a real CNC master after graduating from CNC major and entering the factory. There are absolutely no quick skills in this industry! Now that the division of labor in factories is getting more and more detailed, you must not think that you have mastered a certain skill without thinking about making progress. Only by constantly pursuing technological progress and constantly pursuing excellence can we establish ourselves in the enterprise as a master.
1. Must be an excellent technician
ವಾಸ್ತವವಾಗಿ, when we choose the profession of machining, it means that the early career is difficult. The basic knowledge learned in school is pitiful to meet the needs of the factory. Machining engineers are, to some extent, experienced engineers. ಆದ್ದರಿಂದ, a lot of time must be with workers, familiar with lathes, ಮಿಲ್ಲಿಂಗ್ ಯಂತ್ರಗಳು, grinders, machining centers, ಇತ್ಯಾದಿ. Then in the office, the process is programmed, the material consumption is estimated, and the quota is calculated.
ಈ ಮಾರ್ಗದಲ್ಲಿ, after 2-3 years of practice, you can basically become a qualified technician. Young people who are just working must humbly learn from the workers. Once they can pass on decades of experience to you, you can avoid many detours. Because these experiences cannot be learned in books, the choice of technology is a comprehensive consideration of equipment capabilities and personnel technical capabilities.
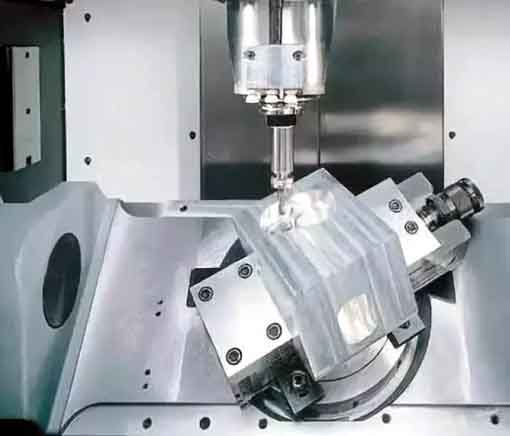
CNC machining sets drilling, ಗಿರಣಿ, ನೀರಸ, ರೀಮಿಂಗ್, ಟ್ಯಾಪಿಂಗ್
2. Through long-term study and accumulation, you should reach the following numerical control technical standards and requirements:
1. Familiar with the structure and process characteristics of lathes, ಮಿಲ್ಲಿಂಗ್ ಯಂತ್ರಗಳು, boring machines, grinders and planers;
2. Familiar with the performance of processed materials;
3. Solid basic knowledge of tool theory, master the conventional cutting amount of the tool, ಇತ್ಯಾದಿ;
4. Familiar with the company’s process specifications, guidelines and general requirements that can be achieved by various process processing, process routes of conventional parts, reasonable material consumption and working hours quota, ಇತ್ಯಾದಿ;
5. Collect a certain amount of tool, machine tool, and mechanical standard data, especially familiar with the tool system used in CNC machine tools;
6. Familiar with the selection and maintenance of coolant;
7. Have a common sense understanding of related types of work, ಉದಾಹರಣೆಗೆ: ಬಿತ್ತರಿಸುವುದು, electrical processing, heat treatment, ಇತ್ಯಾದಿ;
8. Have a good fixture foundation;
9. Understand the assembly requirements and use requirements of the processed parts;
10. Have a good technical basis for product measurement.
CAM programming software needs to learn modeling, but it is not difficult for people with a good CAD foundation. Reading is the most suitable for learning this knowledge.
3. Skilled in operating CNC machine tools
This requires 1-2 years of learning, and the operation is sensitive to the touch. Beginners, especially students, know how to do it, but the operation just cannot be controlled. In this process, learn: System operation mode, fixture installation, part datum alignment, tool setting, zero offset setting, tool length compensation, radius compensation, tool and tool holder loading and unloading; Sharpening of knives; Measurement of parts (proficient in the use of vernier calipers, micrometers, dial indicators, dial indicators, inner diameter lever gauges), ಇತ್ಯಾದಿ.
The practice of operation requires savvy! Sometimes there is an artistic conception of “a leisurely heart, but a good point is difficult to talk to you”! In the CNC workshop, you can calm down and practice! ಸಾಮಾನ್ಯವಾಗಿ ಹೇಳುವುದಾದರೆ, the process from the processing of the first prototype parts to the qualified processing accuracy requires the CNC programming technician to complete it in person. You can’t operate the machine proficiently, you can’t pass this level.
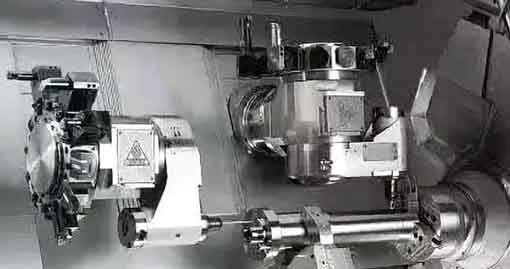
Estimation of material consumption and pricing of CNC machining parts
4. Good tooling and fixture foundation and measurement technology level
I listed tooling fixtures and measurement technology as a separate focus because:
It plays an important role in the quality of parts processing and machine tool accuracy, and is one of the signs that reflects the level of CNC technicians.
Accurate measurement level is one of the basic skills for CNC machining. To be proficient in using vernier calipers, micrometers, dial indicators, dial indicators, internal diameter lever meters, calipers, ಇತ್ಯಾದಿ. Sometimes parts processing, three-coordinate measuring machine is not expected. Must be measured manually. Just imagine, the parts are not accurately measured, which master will trust you?
5. Proficient in the maintenance of CNC machine tools
ಪ್ರಥಮ, you must be familiar with CNC machine tools, and it is recommended to consult the master of the equipment maintenance department. I won’t talk about the details of machine maintenance. Each company has its own experience and standards. The main point of machine maintenance is “maintenance”, which should be paid attention to at ordinary times.
6. Cultivate good habits and adapt to the characteristics of CNC machining
To become a master of CNC machining should be humble, rigorous, calm, meticulous thinking, methodical and independent.
1> The CNC machining of some large parts not only has a lot of processing content, but also has the conversion of space three-dimensional coordinates. The calculation of the processing trajectory is very complicated and difficult to determine. If the consideration is not detailed and comprehensive, and the calculation is not accurate, the program modification will become more chaotic during debugging, and the probability of error will be greater. “Think twice before acting” is most appropriate here.
2> The part debugging process is a process of multi-person cooperation. Including operators, inspectors, fixture designers, fixture assembly personnel, ಇತ್ಯಾದಿ. When problems arise, you should consult them more, do more experiments, and avoid making arbitrary conclusions. Don’t blame too much on employees who make mistakes.
3> The work of CNC machine tools is controlled by instructions. During debugging, you must be very clear about the track of the machine tool before pressing the “Start” button. Be rigorous and meticulous, and never let the machine tool run before debugging. Once the program is wrong or the compensation parameters are incorrect, or the wrong coordinate system is selected. In the worst case, the parts will be scrapped, and in the worst case, there will be a safety accident. Those who are grumpy, clueless, and do not change after repeated instruction are not suitable for CNC machine operation.
4> When there is a problem during debugging and processing, please calm down and don’t panic. If misoperation occurs again, the psychological quality is better.
5> When the parts are unqualified for many times during debugging, the analysis must be organized and the responsibility must be based. Certain relevant departments will give various explanations for various reasons. ಈ ಸಮಯದಲ್ಲಿ, you have to be assertive and remember: it doesn’t matter if you do one thing wrong, but you can’t choose the wrong way to do it.
6> Any CNC technician has limitations in technical ability due to environmental constraints. Coupled with the rapid development of technology, there is always room for improvement. When the internal technology of the factory has been digested, we must keep our eyes open and follow the advanced processing technology at home and abroad to learn and digest.