Machining is a manufacturing process that comprises a set of Non-standard parts shaping operations by removing material, either by chip removal or by abrasion. Also in some areas of South America the term machined is used, although due to the double meaning that this term may have (warping or plotting something) it would be advisable to use the first. It is made from semi-finished products such as ingots, billets or other pieces previously formed by other processes such as molding or forging. The products obtained can be final or semi-finished that require subsequent operations. The most widely used machine tool in this manufacturing process is the lathe.
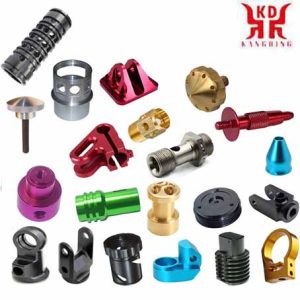
Machining Non-Standard Parts
Non-Standard Machining without chip removal
All metal Non-Standard parts, except castings, at some point in their manufacture have undergone at least one metal-forming operation, and several different operations are often required. ಹೀಗೆ, the steel used in the manufacture of tubes for the construction of chairs is forged, hot rolled several times, cold rolled into sheet metal, cut into strips, cold formed into the tubular shape, it is welded, machined into weld, and sometimes cold drawn as well. The theory of metal forming can help determine how to use machines in the most efficient way possible, as well as improve productivity. the machining includes a final piece of great resistance.
Manual machining
It is done by a person with exclusively manual tools: saw, file, chisel, burin (EDM); in these cases the operator machines the Non-Standard part using one of these tools, using his dexterity and strength.
Non-Standard Machining with machine tools
Machining is done by means of a manual, semi-automatic or automatic machine tool, but the machining effort is carried out by mechanical equipment, with the necessary motors and mechanisms. Classic machining machine tools are:
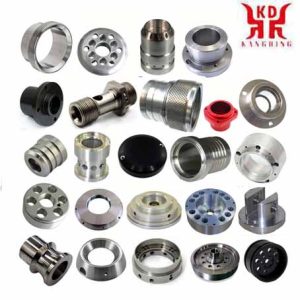
Non-standard milling parts
Drill: The piece is fixed on the drill table, the tool, called a drill, performs the rotary cutting movement and linear advance, machining a hole or drill theoretically of the same diameter as the drill and of the desired depth.
File machine: this machine tool performs machining with a blade mounted on the ram’s tool holder, which performs a linear cutting movement, on a piece fixed to the table, which has the advance movement perpendicular to the cutting movement.
Mortiser: machine that removes material linearly from inside a hole. The cutting movement is carried out by the tool and the advance movement by the table where the Non-Standard part to be machined is mounted.
Planer: larger than the filing machine, it has a sliding table on which the piece is fixed and which performs the cutting movement by sliding longitudinally. the blade mounted on a bridge on the table moves transversely in the forward movement.
Broaching machine: Machine in which the cutting movement is carried out by a progressive multi-edged broach tool that removes material from the piece with a linear movement.
ಲೇಥ್: the lathe is the most widely used machining machine tool. These are in the industry the most general use, the piece is fixed on the lathe plate, which performs the cutting movement by turning on its axis, the blade performs the forward movement eliminating the material in the precise places.
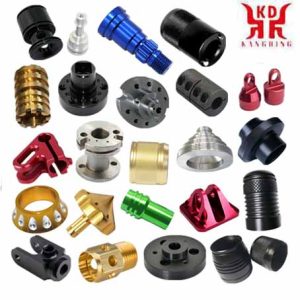
ಪ್ರಮಾಣಿತವಲ್ಲದ ತಿರುವು ಭಾಗಗಳು
Multi-task lathe: This machine allows machining in multiple axes, integrating both turning operations (ತಿರುಗುತ್ತಿದೆ, facing, ಕೊರೆಯುವುದು, …) and milling operations. ಜೊತೆಗೆ, it usually has a double screw, so that the part, performing a transfer operation between the screws, comes out completely finished.
Milling machine: in the milling machine the cutting movement is controlled by the tool; called milling cutter, rotating on its axis, the advance movement is held by the piece, fixed on the table of the milling machine that performs this movement. Together with the lathe, it is the most universal and versatile machine tool.
For some time now, computer science applied to industrial automation has made the machine tool evolve towards numerical control. ಹೀಗೆ, we are talking about 5-axis machining centers and multifunction lathes, which allow obtaining a complex part, completely finished, starting from a billet or a metal bar and all this in a single clamping.
These numerically controlled machines offer versatility, high production and preparation capacities, offering extremely high precision on the order of microns.
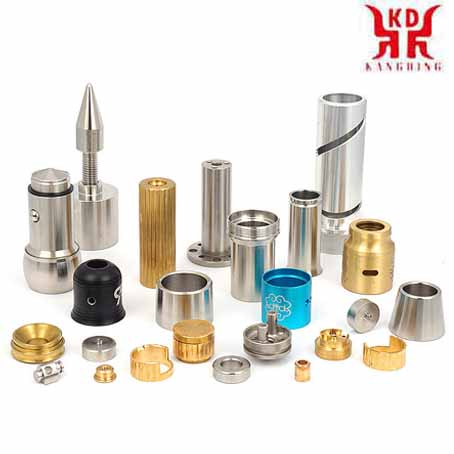
Non-standard micro-machined parts