ನಾನು ಕಾರ್ಯಾಗಾರದಲ್ಲಿದ್ದೆ ಮತ್ತು ಪರಿಪೂರ್ಣ ಭಾಗಗಳನ್ನು ಪಡೆಯಲು ಅಲ್ಯೂಮಿನಿಯಂ ಅನ್ನು ಮಿಲ್ಲಿಂಗ್ ಮಾಡುವಾಗ ಯಾವುದು ಮುಖ್ಯ ಎಂದು ಕೇಳಿದೆ.
ಹಾಗಾಗಿ ಸಂಶೋಧನೆ ಆರಂಭಿಸಿದೆ, ಪುಸ್ತಕಗಳ ಮೂಲಕ ಸುತ್ತಿಕೊಳ್ಳುವುದು ಮತ್ತು ಅರ್ಧದಷ್ಟು ಇಂಟರ್ನೆಟ್ ಅನ್ನು ಹುಡುಕುವುದು. ಈ ಲೇಖನದಲ್ಲಿ ಅಲ್ಯೂಮಿನಿಯಂ ಮಿಲ್ಲಿಂಗ್ ಬಗ್ಗೆ ನಾನು ಕಂಡುಕೊಂಡ ಎಲ್ಲವನ್ನೂ ನಾನು ಸಂಕ್ಷಿಪ್ತಗೊಳಿಸಿದ್ದೇನೆ.
ಅಲ್ಯೂಮಿನಿಯಂ ಅನ್ನು ಮಿಲ್ಲಿಂಗ್ ಮಾಡುವಾಗ ನೀವು ಏನು ನೋಡಬೇಕು?
From a technical point of view, components made of aluminum with polished surfaces and a dimensional accuracy of 1/100 mm and less can be produced.
ಆದಾಗ್ಯೂ, in order to achieve very high surface quality and good dimensional accuracy, the boundary conditions must be right when milling aluminum.
end mill
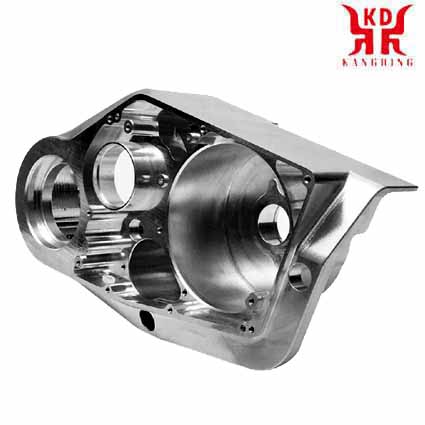
5-axis milling of aluminum parts
In contrast to the processing of wood and steel, aluminum can become soft due to the heat generated during milling. Molten aluminum can then stick the cutting edges of the milling tool.
ಪರಿಣಾಮವಾಗಿ, the chips can no longer be removed, the chip space clogs and new chips are no longer cut. The inevitable result is an unusable surface and the breakage of the milling tool.
Milling aluminum – 6 important parameters
So that you can mill aluminum ideally, you should know the most important parameters and properties of the machining process.
For a top milling result, the correct interaction between the physical properties of the aluminum alloy, the milling tool and the machine parameters is required. A correctly set milling process determines whether the machining process is successful or not.
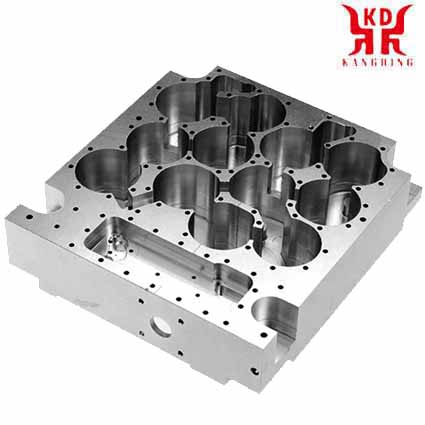
ಅಲ್ಯೂಮಿನಿಯಂ ಯಂತ್ರದ ಮೂಲಭೂತ ಅಂಶಗಳು
ದಿ 6 most important parameters for milling aluminum are:
Type of aluminum alloy
Type of cutter (material and number of cutting edges)
Height of the feed speed
Height of the cutter speed
Type of cooling lubricant (KSS)
ಮಿಲ್ಲಿಂಗ್ ವಿಧಾನ
These 5 parameters are explained in more detail below:
Which aluminum alloys to use for milling?
Choosing a suitable aluminum material is half the battle. Soft aluminum sheets from the hardware store are comparatively difficult for machining.
Aluminum with defined alloy additives can be many times stronger than pure aluminum. It can also be said that brittle alloys with higher tensile strength are easier to machine.
“Brittle alloys with higher strength are easier to machine.”
If you cannot specify a DIN designation when ordering your material, please ensure that you request at least aluminum in turning / milling quality.
As is well known, e.g. the alloys EN AW-2007 and EN AW-6012 are typical free-cutting alloys. The high-strength “aircraft aluminum” EN AW-7075 is usually very easy to machine.
The following table shows the suitability of frequently used aluminum alloys for milling:
EN designation No. old norm Machining welding Anodizing Yield strength min.
[N / mm²]
EN AW-1050A 3.0255 Al99,5 (Reinalu) bad mittel gut 20
EN AW-2007 3.1645 AlCuMgPb very good bad bad 210
EN AW-2011 3.1655 AlCuBiPb very good bad bad 195
EN AW-2017 3.1325 AlCuMg1 very good bad bad 220
EN AW-2024 3.1355 AlCuMg2 Well bad bad 270
EN AW-5083 3.3547 AlMg4,5Mn Well very good Well 110
EN AW-5754 3.3535 AlMg3 middle Well Well 70
EN AW-6012 3.0615 AlMgSiPb very good bad bad 200
EN AW-6026 – AlMgSiBi Well Well Well 240
EN AW-6060 3.3206 AlMgSi0,5 middle Well Well 160
EN AW-6061 3.3211 Mg1SiCu middle very good bad 230
EN AW-6063 – AlMg0,7Si middle middle Well 110
EN AW-6082 3.2315 AlMgSi1 Well Well middle 200
EN AW-7020 3.4365 AlZn4,5Mg1 Well middle middle 270
EN AW-7075 3.4365 AlZnMgCu1,5 very good bad middle 400
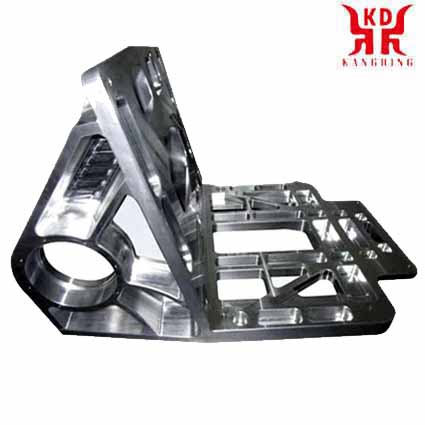
Aluminum parts are milled correctly
Selection of milling cutters for machining aluminum
End mill
The shorter and thicker the cutter, the greater its stability and strength. A stable cutter prevents the cutter from swinging and breaking. Similar to milling all other materials, the following rule of thumb also applies to aluminum:
“The milling cutter has to be as thick as possible and as short as possible.”
ಜೊತೆಗೆ, the free removal of the chips by the milling cutter must be guaranteed for a good milling result. The single-edge milling cutter has the best chip evacuation, as this is where the chip space is greatest. ಆದಾಗ್ಯೂ, the lower the number of cutting edges, the higher the load on the individual cutting edge as a rule.
ಈ ಕಾರಣಕ್ಕಾಗಿ, a compromise must be made between cutting edge load and good chip evacuation when milling aluminum.
Inexpensive milling cutters are not recommended because the cutting edges quickly become blunt and the service life of the milling cutter is significantly shorter than with high-quality milling cutters.
Originally the statement was made that a single-edge milling cutter is not suitable for machining aluminum. Fortunately, an extremely knowledgeable reader (JACK) corrected my misjudgment and pointed out, ಉದಾಹರಣೆಗೆ, the so-called “single tooth cutter with hawk’s beak” from VHF, which is actually particularly well suited for machining aluminum!
Speed and feed rate
The cutting speed (combination of speed and feed rate) also has a significant influence on the result when milling aluminum.
Values of thumb:
Cutting speed for aluminum: vc ~ 100 ಮೀ / min for high-quality HSS milling cutters.
Feed for aluminum: fc ~ 0.1 mm per cutting edge. With a three-cutter this is 0.3 mm feed per milling cutter revolution.
In technical tables (e.g. metal table book) you can find or calculate the guide values for speed, size and feed of the different tools and alloys.
The speed of the milling cutter is calculated using the following relationship:
n = vc / d x pi
n = speed of the milling cutter in rpm
vc = cutting speed in mm / ನಿಮಿಷ
d = cutter diameter in mm
pi = circle number (3.14)
The feed rate of the milling cutter is calculated using the following formula:
vf = n * z * fz
vf = feed speed in mm / ನಿಮಿಷ
n = milling cutter speed in rpm
z = number of cutting edges on the milling cutter
fz = tooth feed in mm / tooth
Example calculation:
3 cutters with 6 mm cutter diameter.
Cutting speed vc = 100 ಮೀ / min = 100 * 1000 ಮಿಮೀ / ನಿಮಿಷ
Milling cutter diameter d = 6 ಮಿಮೀ
Milling speed n = 5300 rpm
Feed fz = 0.1 ಮಿಮೀ / rev
-> feed speed vf = 1600 ಮಿಮೀ / ನಿಮಿಷ
For all lazy CNCers there is also a calculation tool for determining the cutting data.
Choosing the coolant when milling aluminum
ಅಂತಿಮವಾಗಿ, you should think about the right cooling.
The general question is whether to work with or without cooling lubricant.
The disadvantages of wet milling are high temperature fluctuations in the cutting edge, which lead to a shorter tool life. The fluctuations are smaller with dry milling. When roughing, you should work dry if possible.
Some hobbyists also use petroleum / alcohol from the squirt bottle for cooling. I do not recommend this, ಆದಾಗ್ಯೂ, as petroleum / alcohol is easily flammable and therefore dangerous. If you work with minimum quantity lubrication, make sure to use a suitable cooling lubricant for aluminum.
ಸೂಚನೆ: When using water-based cooling lubricants, please clean the machine completely after using the KSS.
In the event of a longer standstill, the water separates from the emulsion and causes your milling machine to rust.
ಇದಲ್ಲದೆ, standing cooling lubricant can easily accumulate fungi and bacteria, which is why special fungicides are often necessary as an additive in the cooling lubricant.
ಮಿಲ್ಲಿಂಗ್ ವಿಧಾನ
The choice of milling method, such as up-cut milling, down-cut milling, circular milling, helical milling or trochoidal milling (whirl milling) also has a direct influence on the milling result. Trochoidal milling increases the tool life enormously.
The following video shows what exactly trochoidal milling is.
A frequent tip is to continue to ensure sufficient delivery. Infeeds of 0.3 mm or less place a heavy load on the cutting edge and lead to faster tool wear. Just be brave and experiment with slightly higher infeeds.
Application examples
Tons of aluminum parts are milled every day.
Typical application examples range from machine and vehicle construction, through engraving of signs to lightweight components in aircraft construction.
The face milling of sealing surfaces on engine or gear housings is just as much a part of everyday aluminum milling tasks as the production of fashionable aluminum jewelry.
Other readers were also interested in:
How are plastics properly milling?