百年前, ハイス切削工具の使用開始, 普通鋼のフライス加工の切断速度はわずか25〜30m/分でした. 炭素工具鋼、合金工具鋼との比較, その切削速度での加工は “高速フライス加工”. したがって, “ハイス鋼” と名付けられた. In the era when high-speed steel tools just appeared, American Taylor F.W. engineers did a lot of CNC cutting theory and practice work, and established the T-v equation. He has made great contributions to CNC cutting technology and industrial management.
50 years ago, shortly after the end of the Second World War, cemented carbide tools began to be widely used. At that time, carbide tools were used to cut ordinary steel, and cutting speeds of 80-100m/min were available. At that time, this cutting speed was called “高速フライス加工”.
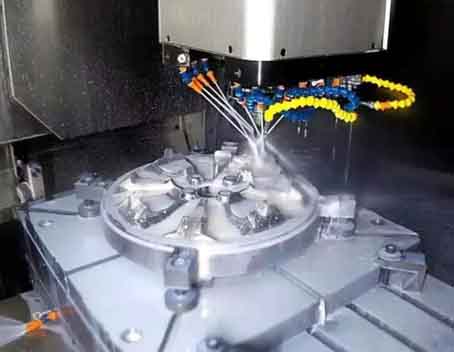
高速フライス加工部品
In April 1931, German physicist Carl. J. Saloman first proposed the theory of high-speed milling and applied for a patent in the same year. He pointed out: In the range of conventional cutting speed, the cutting temperature increases with the increase of cutting speed. しかし, after the cutting speed is increased to a certain value, the cutting temperature will not increase but will decrease, and the cutting speed VC is related to the type of workpiece material. For each workpiece material, there is a speed range, within this speed range, due to the high cutting temperature, the tool material cannot bear it, and the cutting process is impossible. If this speed range can be exceeded, high-speed milling will be possible, thereby greatly improving production efficiency. Due to the limitation of experimental conditions, high-speed cutting could not be put into practice at that time, but this idea gave posterity a very important enlightenment.
High-speed CNC machining technology has gone through four stages: theoretical exploration, application exploration, preliminary application and more mature application, and has now been popularized in production. Especially since the 1980s, the needs of the aviation industry and the mold industry have greatly promoted the application of high-speed machining. There are a large number of thin-walled parts in aircraft parts, such as wing ribs, long stringers, frames and so on. They have very thin walls and ribs, the metal removal rate is very high during processing, and they are prone to CNC cutting deformation, which is more difficult for CNC processing; 加えて, aircraft manufacturers also urgently demand to improve the processing efficiency of parts, thereby shortening the delivery time of the aircraft. In the mold industry and the automotive industry, mold manufacturing is a key. Shortening the mold delivery cycle and improving the quality of mold manufacturing are also the long-term goals of people’s efforts. High-speed cutting is undoubtedly an important way to solve these problems. Since the 1990s, high-speed machining has gradually been promoted and applied in the manufacturing industry. 現在のところ, according to statistics, in the United States and Japan, about 30% of companies have used high-speed machining, and in Germany, this proportion is higher than 40%. In the aircraft industry, high-speed milling has been commonly used for machining parts.
現在のところ, high-speed cutting has been applied to a certain extent, but it is still difficult to give a precise definition to high-speed milling, and it is difficult to give the milling speed range of high-speed cutting. High-speed cutting is a relative concept, which has a great relationship with processing materials, processing methods, ツール, cutting parameters and so on. It is generally believed that the milling speed of high-speed cutting is 5-10 times the conventional cutting speed. For commonly used materials, some materials give rough data: aluminum alloy 1500~5500 m/min;
Copper alloy 900 ~5000 m/min;
Titanium alloy 100~1000 m/min;
Cast iron 750~4500 m/min;
Steel 600~800 m/min. The feed speed range for high-speed cutting of various materials is 2~25m/min.