ステンレス鋼材は靭性が高い, 高い熱強度と低い熱伝導率. フライス加工および旋削加工中, 塑性変形が大きい, 加工硬化は深刻です, 切断熱が高すぎる, そして放熱が難しい. その結果、工具先端の切削温度が高くなります。, 刃先への切りくず付着が激しい, 切りくずエッジが蓄積しやすい, 工具の磨耗を悪化させるだけではありません, ただし、加工面の表面粗さにも影響します。. 加えて, チップがカールしたり壊れたりしにくいため、, 加工面にダメージを与え、ワークの品質に影響を与えます。. 加工効率とワークの品質を向上させるために, 工具材料を正しく選択する方法, 旋削工具の幾何学的パラメータと加工量は次のように導入されます。:
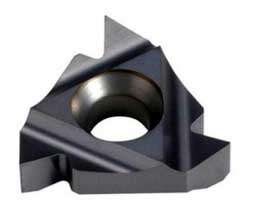
Stainless steel turning tools
Tools for milling and turning stainless steel
1. The correct choice of milling tool materials. The tool material is the decisive factor to ensure high-efficiency machining of stainless steel. According to the cutting characteristics of stainless steel, the tool material should have sufficient strength, toughness, 高硬度, high wear resistance and low adhesion to stainless steel. Commonly used tool materials include cemented carbide and high-speed steel, and tools with complex shapes mainly use high-speed steel materials. Since the cutting speed of high-speed steel cutting stainless steel cannot be too high, it affects the improvement of production efficiency. For simpler turning tools, the tool material should be high-strength, good thermal conductivity cemented carbide, because its hardness, wear resistance and other properties are better than high-speed steel.
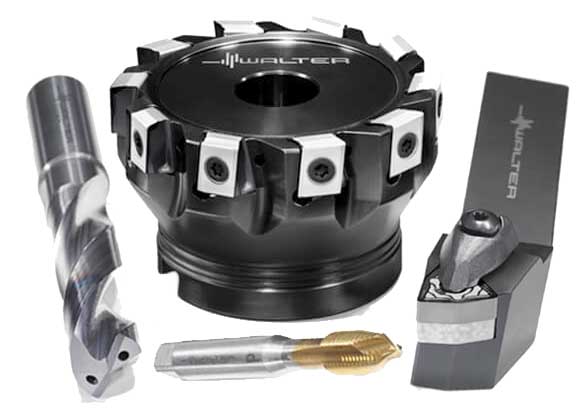
ステンレス鋼フライス工具
Commonly used cemented carbide materials are: Tungsten cobalt type (YG3, YG6, YG8, YG3X, YG6X), tungsten cobalt titanium type (YT30, YT15, YT14, YT5), general type (YW1, YW2). YG cemented carbide has good toughness and thermal conductivity and is not easy to bond with chips. したがって, it is suitable for rough turning of stainless steel; The hardness, 耐摩耗性, heat resistance, oxidation resistance and toughness of YW cemented carbide are good, and they are suitable for stainless steel fine turning processing. When processing 1Cr18Ni9Ti austenitic stainless steel, YT cemented carbide is not suitable. Because Ti in the stainless steel and Ti in the YT-type hard alloy have an affinity, the chips can easily take away the Ti in the alloy, which promotes the increase of tool wear.
Geometric angle of milling and turning tools
2. Choosing the geometric angle of the cutting part of the tool has a great influence on the productivity of stainless steel cutting, tool durability, surface roughness, cutting force and work hardening. Reasonable selection and improvement of tool geometric parameters is an effective way to ensure processing quality, improve efficiency and reduce costs.

Set the geometric angle of the tool for milling stainless steel
The choice of turning tool rake angle γ0:
The size of the rake angle determines the sharpness and strength of the blade. Increasing the rake angle can reduce chip deformation, thereby reducing cutting force and cutting power, lowering cutting temperature, and improving tool durability. しかし, increasing the rake angle will reduce the wedge angle, reduce the strength of the blade, cause chipping of the blade, and reduce the durability of the tool. When turning stainless steel, the rake angle should be appropriately larger without reducing the strength of the tool. When the tool rake angle is large, its plastic deformation is small, the cutting force and cutting heat are reduced, the work hardening trend is reduced, and the tool durability is improved. 一般的に, the rake angle of the tool should be 12°~20°.
Selection of lathe tool relief angle α0
In the cutting process, the relief angle can reduce the friction between the flank face and the cutting surface. If the relief angle is too large, the wedge angle will decrease, worsening the heat dissipation conditions, reducing the strength of the cutting edge of the tool, and reducing the durability of the tool; If the relief angle is too small and the friction is serious, the cutting edge will become blunt, increase the cutting force, increase the cutting temperature, and increase the wear of the tool. 通常の状況下で, the clearance angle does not change much, but it must have a reasonable value to help improve the durability of the tool. When turning stainless steel, since the elasticity and plasticity of stainless steel are greater than that of ordinary carbon steel, the tool clearance angle is too small, which will increase the contact area between the cutting surface and the turning tool clearance angle. The high temperature area generated by friction is concentrated on the back corner of the turning tool, which accelerates the wear of the turning tool and reduces the finish of the processed surface. したがって, the clearance angle of the turning tool when turning stainless steel is slightly larger than that when turning ordinary carbon steel. しかし, too large a relief angle will reduce the strength of the blade and directly affect the durability of the turning tool. したがって, 通常の状況下では, the clearance angle of the turning tool should be 6°~10°.
The choice of turning tool entering angle Kr
When the cutting depth ap and the feed amount f remain unchanged, reducing the entering angle Kr can improve the heat dissipation conditions, reduce tool damage, and make the tool cut in and cut out smoothly. しかし, the decrease of the entering angle will increase the radial force, which will easily cause vibration during cutting. Turned stainless steel has a strong tendency to harden and is prone to vibration, which will cause serious work hardening. したがって, the entering angle should generally be 45°~90°. The specific angle should be selected according to the rigidity and cutting amount of the machine tool, 部品, and tool system. The choice of turning tool blade inclination λs The blade inclination can control the chip flow direction. When the blade angle λs is negative, the chips flow to the machined surface; When the blade angle λs is positive, the chips flow to the surface to be processed. In order to prevent the chips from scratching the machined surface, the blade angle λs is a positive value during finishing. When λs is a positive value, the strength of the tool tip is low and first contacts the workpiece, which is easy to damage; When λs is a negative value, the cutting edge has high strength and impact resistance, which can avoid breaking the cutting edge and cut in and out smoothly. When turning stainless steel, the inclination angle of the cutting tool is generally 0°~20°.
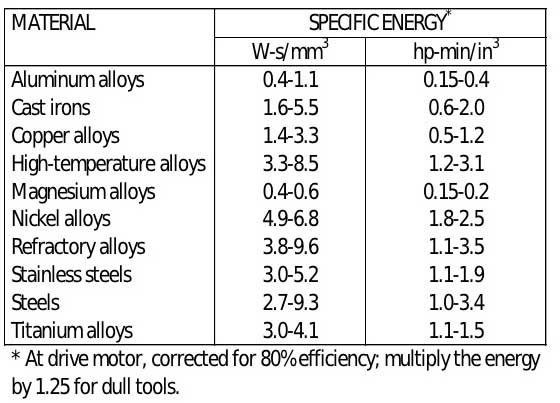
Turning amount of stainless steel
3. Selection of turning and milling amount
The amount of turning and milling has a great impact on production efficiency and processing quality. したがって, after determining the geometric parameters of the tool, a reasonable cutting amount must be selected. When choosing cutting parameters, the following factors should be considered:
1>The cutting amount should be selected according to the hardness of stainless steel and various blanks;
2>The cutting amount should be selected according to the tool material, welding quality and sharpening conditions of the turning tool;
3>The cutting amount should be selected according to the part diameter, machining allowance and lathe accuracy. 同時に, in order to suppress the generation of built-up tumors and scales, and improve the surface quality. When using cemented carbide tools for processing, the cutting amount should be slightly lower than turning general carbon steel workpieces, especially the cutting speed should not be too high (vc=50~80m/min);
The cutting depth ap should not be too small to avoid the cutting edge and the tool tip from scratching the hardened layer, ap=0.4~4mm; したがって, the feed rate f has less impact on tool durability than cutting speed, but it will affect chip breaking and chip removal, strain and scratch the surface of the workpiece, and affect the surface quality of processing. The feed rate is generally f=0.1~0.5mm/r.
ステンレス鋼, especially austenitic stainless steel, has better plasticity. During cutting, the generated chips are difficult to break, which increases the friction between the chips and the rake face of the tool and increases the cutting force. 同時に, work hardening will increase the hardness and strength of the material being cut, which will also increase the cutting force. このため, on the basis of reasonable selection of tool materials, tool geometric angles and cutting parameters, a comparative test of cutting force was done on stainless steel and 45 鋼鉄. The test results show that, under the same cutting amount, the cutting force when machining stainless steel is only 8.5% higher than when machining 45 鋼鉄. Reasonable selection of tool materials, tool geometric angles and cutting quantities is completely possible to improve the production efficiency of stainless steel cutting and the quality of processed workpieces.