高速フライス加工システムは複雑な動的システムです, 薄肉部品の加工時にびびり振動が発生しやすい. フラッターは、フライス加工プロセス中の工具とワークピースの間の非常に強い相対振動です。. この種の振動は、工具とワークの相対的な正しい位置を破壊します。, 表面処理品質とフライス加工効率が低下します。. 長い間, 切削びびりは、機械製造業界およびフライス加工における主要な研究テーマとなっています。. The research on cutting chatter involves a wide range of contents. In this paper, a certain research on the flutter model, including the nonlinear mathematical model and stability conditions; On this basis, MATLAB/SIMULINK software is used to carry out a certain simulation study on the generation and control of chatter, including the adjustment strategy of milling parameters (主軸速度, feed, tool angle, 等).
There is relative movement between the tool and the workpiece, and the excess material of the workpiece is removed by the action of the cutting edge and the knife face.
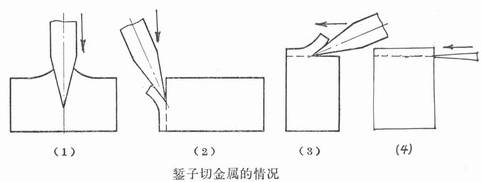
Allowance on the milled workpiece
形 1, the allowance of the chisel milled on the workpiece
図に示すように 1, the milling edge plays the role of “cutting” and “milling”, and the cutter face plays the role of “pushing”.
“Cut”-the workpiece has no motion component relative to the cutting edge.
“フライス加工”-the workpiece has a motion component relative to the cutting edge.
“squeeze”-mainly the squeeze of the rake face, but also a certain amount of squeeze on the flank face.
The margin of removal of the workpiece is the result of the combined effect of the above three. Due to the high strength of the material being cut, the knife has a large wedge angle and cannot be very thin. の “push” function consumes a large share of energy;
And “cutting” そして “フライス加工” play an important role in separating the cut material and forming the machined surface.
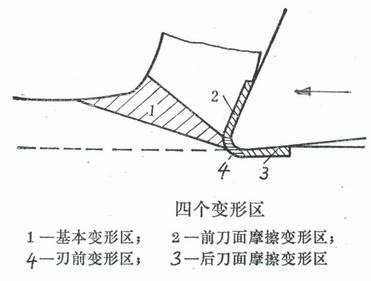
Four deformation zones during milling
形 2. Four deformation zones of the part
図に示すように 2, 1 is the basic deformation zone of the part;
2 is the frictional deformation zone of the rake face;
3 is the frictional deformation zone of the flank surface;
4 is the front deformation zone. Zone 1 and Zone 2 consume the main part of power, while Zone 3 and Zone 4 play an important role in forming the processed surface.
If the cutting edge is very sharp, zone 4 is very small;
If the tool clearance angle is large, zone 3 is also small.
Zone 1 is the main deformation zone. If the cutting speed is high, zone 1 becomes very narrow and almost becomes a surface (a line as shown in Figure 4), which is called a shear surface. The angle between the direction of the shear surface and the aspect of the cutting speed is the rake angle Φ.
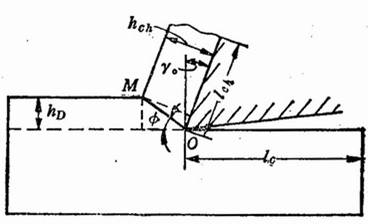
Shear surface and deformation coefficient during milling
形 3. Shear surface and deformation coefficient
The approximate value of shear angle φ can be calculated by the following formula:
M. E. Merchant formula
Φ=π/4-β/2+γo/2
Lee and Shaffer (Lee and Shaffer) formula
Φ=π/4-β+γo
式では, β is the friction angle between the rake face and the chip, and γo is the rake angle.
When the milling speed is increased very high, the material to be cut will not have time to fully deform, the shear angle Φ increases, the amount of deformation decreases, and the milling force also decreases. After the milling speed is increased, the friction coefficient between the front and flank faces and the chip and the workpiece is reduced, which is also conducive to the reduction of the milling force.
There is a simple way to measure material deformation, あれは, to calculate the “deformation coefficient” through measurement. It was called “shrinkage factor” in the past, and the two are the same thing.
図に示すように 3, the original length of the milled layer is lc, and the length after forming chips is lch, then the deformation coefficient Λh=lc/ lch
In the process of milling, the material of the cut layer turns into chips, which undergoes shear slip. According to the principles of material mechanics, it is more scientific to measure the degree of deformation of a material by the amount of shear strain. There is a certain relationship between the shear strain ε and the deformation coefficient. After calculation,
Ε=ΔS/Δy=cosγ0/[sinφ?cos(φ-γ0)]
=ctgφ+tg(φ-γ0)
=(Λh2-2Λh?sinγ0+1)/(Λh?cosγ0)
式では, γo is the rake angle of the tool.
Λh and ε increase, it means that the material deformation is large;
vice versa.
Obviously, during high-speed milling, both Λh and ε decrease, and the milling force decreases.
Perform high-speed milling deformation coefficient tests of 45 steel and aluminum alloy 5A02. Suppose: the tool is a cemented carbide end mill with φ20mm, Cutting ap=0.5~1mm, The feed amount is fz=0.05~0.15mm/z, Cutting speed v=251~1256m/min. The test results are shown in Figure 5 and Figure 6.
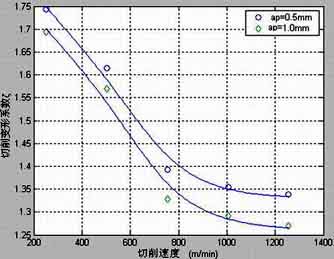
Deformation coefficient of 45 steel during high-speed milling
形 4 Deformation coefficient of high-speed cutting 45 鋼鉄
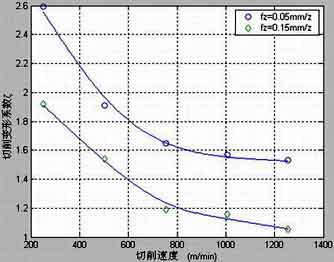
Deformation coefficient of aluminum alloy 5A02 during high-speed milling
形 5 Deformation coefficient of high-speed cutting aluminum alloy 5A02
It can be seen from the figure that when the cutting speed increases, the deformation coefficient decreases significantly.