製品カテゴリ
- CNCフライス加工サービス 31
- CNCスタンピングサービス 0
- CNC板金 0
- ラピッドプロトタイピング 12
- スタンピングダイ 0
- チタン合金部品 4
- ステンレス鋼部品 5
- アルミフライス部品 14
- CNC旋削サービス 16
中国のCNCフライス加工サービス
CNC フライス加工は、事前にプログラムされたコンピューター ソフトウェアが工場のツールや機械の動きを制御する製造プロセスです。. 迅速なプロトタイプまたは生産部品 – 当社は、プラスチックまたは金属部品の生産ニーズに適した CNC フライス加工オプションをご用意しています。. このメソッドは、多数の複雑なマシンを制御するために使用できます。, 研削盤や旋盤からミルやルーターまで. CNCフライス加工あり, 3D 切断タスクは単一のプロンプト セットで実行できます。.
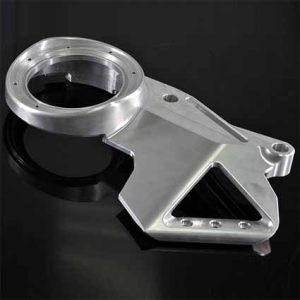
CNC finishing of aluminum alloy parts
CNC Milling a vital role in modern manufacturing.
What is CNC Milling? How does it play a role in manufacturing, and what does CNC machinist do?
CNC フライス加工は、事前にプログラムされたコンピューター ソフトウェアが工場のツールや機械の動きを制御する製造プロセスです。. Rapid Prototypes or Production Parts – We have the right CNC Milling options for your plastic or metal part production needs. このメソッドは、多数の複雑なマシンを制御するために使用できます。, 研削盤や旋盤からミルやルーターまで. CNCフライス加工あり, 3D 切断タスクは単一のプロンプト セットで実行できます。.
Short for “Computer Numerical Control”, the CNC process stands in contrast to the limitations of manual control, which requires live operators to query and guide commands from machining tools via levers, knobs and wheels. To the viewer, a CNC system may resemble a normal set of computer components, but the software programs and consoles used in CNC Milling set it apart from all other forms of computation.
Before NC and CNC Milling
NC machining and later CNC made it possible to control machine tools without the high proportion of manual intervention that had to take place until then to machine a part.
例えば, before CNC and NC machining, the drilling of a tube was done by placing the tube in the press of the machine tool to hold it, selecting in this machine the rotation speed of the drill (generally with belt pulleys) and activating the spindle. These actions had a high proportion of manual manipulation (placing the bit on the axis, activating the axis, placing the workpiece under the drill, machining the hole and shutting down the axis), something that did not pose major problems with small quantities , but as it was required to machine a greater number of parts and carry out more complex machining actions, the probability of fatigue of the person due to the tedium of the operation increased, and therefore decreased productivity and increased the margin of error.
NC machining represented a breakthrough in this sense because it allowed the machine tool to be controlled by means of a perforated belt containing the movements of the machine in relation to the coordinate axes that specified the movement of the cutting tool. このようにして, the intervention of the person was not needed at each step, they could do other tasks, and productivity was greatly increased.
Before numerical control, machining processes had a high component of manual manipulation. Today some isolated operations are carried out manually, with few parts.
Subsequently, this control went from being done with a perforated tape to being done by computer, including the placement of the drill on the shaft, activation, 等. This had several advantages.
Main advantages of CNC Milling
Improved automation compared to numerical control without a computer: This means that the intervention of the person in each step can be reduced or even eliminated, although some type of manual action always takes place for specific tasks, such as repair and prototyping. That allows for higher production in the same time, since CNC machines are capable of running 24 hours a day.
Greater precision and consistency of the pieces obtained: Today’s CNC machines have astonishing precision and repeatability specifications, with two, ten, or a thousand identical workpieces easily achievable once the program is verified. That was critical in mass production.
Greater flexibility: Being machine tools controlled by a computer program, carrying out a new machining that only contains a few small changes compared to a previous job only requires loading a saved project, making certain changes and saving it separately, as in any other software. This allows quick changes and adaptation to any type of part, and eliminates most prototypes.
Greater security: to have a minimal interaction of the operator with the machine in most of the movements. Previously, when intervening in actions such as changing heads, loading material, stopping a movement, 等, there were more chances of having accidents.
Main challenges of CNC Milling
High operating costs: Although CNC machines reduce the number of manual workers required in a manufacturing plant, the machines are more expensive to operate. しかし, the costs associated with running the machines are gradually decreasing.
Training need: Initially, the generalization of CNC Milling led to high unemployment, as the need for manual workers was reduced. しかし, with proper training, this system creates new opportunities for specialized employment. as it requires CNC machine tool operators, programmers, maintenance personnel, as well as machine tool manufacturing engineers and technicians and trainers to teach its operation.
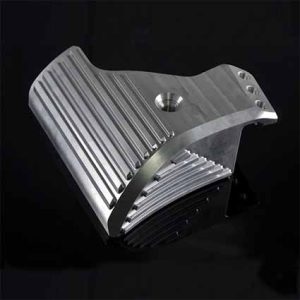
CNC finishing parts
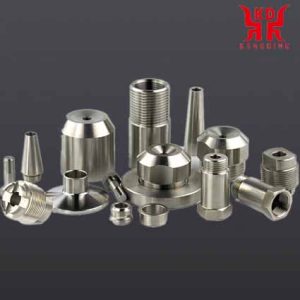
ステンレススチール部品のCNC仕上げ
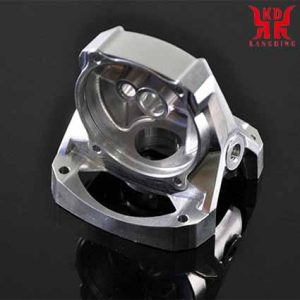
5-軸仕上げパーツ
How CNC Milling Works
Broadly speaking, CNC Milling allows doing practically everything that was previously done manually: placing the drill bit on the axis, activating it, placing the part to be machined on the machine, machining it and turning off the axis. Once the machine tool is configured by CNC and put to work, it requires little intervention from the operators. You can even automate the part loading process.
しかし, the task of the operator is still required to make measurement checks and adjustments to keep the CNC machine working properly.
Movement control
Any CNC Milling machine tool allows programming two or more directions of movement (軸, which can be linear-along a straight line- or rotary-along a circular path-). Common linear axis names are X, Y, とZ. Common rotary axis names are A, B, and C. The more axes the machine has, the more complex it is. In drilling, the three linear axes would position the tool over the hole to be machined in the part on the X and Y axes and would machine the hole with the third Z axis.
Programmable accessories
Although the fundamental function that all CNC Milling machines have is to control movement according to axes, what really gives value to each machine is not moving the part in two or more axes. but rather the programmable accessories that it carries, which make them multiply their functions.
例えば, a machining center may have an automatic tool loader to change the cutting instrument without operator intervention. and if necessary, you can choose the tool and automatically place it on the spindle for machining, or programming the axis speed and spindle activation, or the coolant to lubricate and cool the part that can be turned on and off from within of the machine cycle.
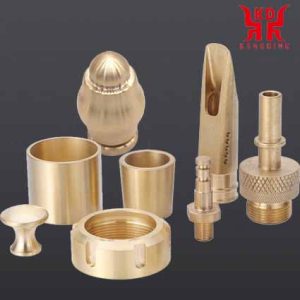
CNC finishing of copper parts
With the CNC Milling system, a part is machined using the following steps:
1) Design of the conceived part: use CAD software to create a 2D or 3D model of the part.
2) CNC programming: use CAM software to convert CAD model to g-code. G-Code is the language used to program CNC machines, which can be edited from a normal text manager (Notepad, Word) or a specialized program.
3) CNC machine setup: In this step, the machine is setup by clamping, suitable tools and G-code editing program (by DNC system), and the tool data is loaded to prepare the machine to machine the part. The operator will also tell the machine where the zero point is to start.
4) CNC Milling of the part: with all the above ready, it is time to start machining the part.
CNC Milling allows doing practically everything that was previously done manually: placing the drill bit on the axis, activating it, placing the part to be machined on the machine, machining it and turning off the axis.
Metal industry and CNC Milling
CNC Milling has revolutionized the metal industry, decisively influencing its economic potential, with higher production at lower cost. Basically we can distinguish three large groups within the metal industry that make CNC Milling machine tools their main work system:
Metal fabrication industry: Thin plates such as steel plates are required in many industries for various purposes, and such plates are machined in the manufacturing industry. generally with CNC machines that carry out various operations such as cutting, flame or plasma cutting, パンチング, laser cutting, contouring and welding and many other applications.
This industry was one of the most used manual machines decades ago (punching machines, disc cutting machines, presses, 等) but today the CNC versions of these same machines are fully extended and are used in a majority way.
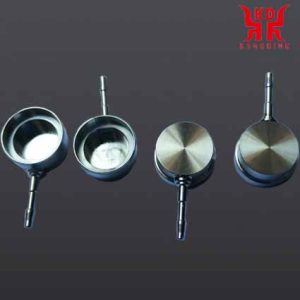
Medical implant titanium alloy cavity
Rapid Prototypes or Production Parts - We have the right CNC Milling options for your plastic or metal part production needs.
Wide range of materials
Meet the Tightest Tolerances
Machining parts directly from 3D CAD models
Standard delivery time between 1 そして 2 weeks, depending on the order
Delivery times may be shorter (2 に 5 営業日), depending on available capacity
Tolerances for the size of the details:
標準: +/- 0.005
Minimum: +/- 0.002 for metal and +/- 0.003 for plastic
Tolerances for hole diameter:
標準: +/- 0.005
Minimum: +/- 0.001 for metal and +/- 0.002 for plastic
Tolerances for flatness, eccentricity, cylindricity, perpendicularity and other geometries:
標準: +/- 0.005
Minimum: +/- 0.001, depending on geometry
The above tolerances do not apply when machining welded assemblies or plates less than 1/4 "thick and greater than 20" thick, または 1/8 "thick with more than 10" length. In these cases, the MFG team will need to review the tolerances.
CNC Milling is a subtractive manufacturing process whereby material is trimmed from the origin to create a finished component. Our standard surface finish is 63 に 125 Rms. しかし, we can grind or polish the part to between 4 そして 8 Rms.
Shot blasting
Electropolished
熱処理
サンドブラスト
Steam polishing
アドバンテージ
Send us your 3D CAD data by email, indicate the specifications of your project and we will present you with a personalized quote in less than 24 時間
旋回, dual revolver lathe with rotary machining, 3-, 4- and 5-axis machining, stress attenuation / heat treatment, 溶接, anodizing and powder coating
CNC machined parts in as little as 6-8 営業日 (depending on geometry)
Dedicated project managers to help you throughout the entire process
お問い合わせ
メールを待っています, 以内に返信させていただきます 12 必要な貴重な情報を何時間も入手できる.