切削は旋削に大別される, フライス加工, 中心刃ベースの切削 (ドリル、エンドミルの端面切削, 等). これらの切削加工の切削熱は刃先にさまざまな影響を与えます。. 旋削とは連続切削です, 刃先にかかる切削抵抗はほとんど変化しません, 切削熱が刃先に継続的に作用します。; フライス加工は断続的な切削の一種です, 刃先にミーリング力が断続的に作用します。, フライス加工中に振動が発生します. 刃先への熱影響は、切削時の加熱と非切削時の冷却が交互に起こります。, 旋回時よりも受ける熱量が少なくなります。.
フライス加工時の切削熱は断続的な加熱現象の一種です。, カッターの歯は、切断していないときに冷却されます。, 工具の寿命を延ばすのに役立ちます. 物理化学研究所が旋削とフライス加工の工具寿命の比較試験を実施. フライス加工に使用する工具はボールエンドミルです。, 旋削工具は一般的な旋削工具です. 両者は同じ加工材質、同じ切削条件です (切断方法の違いにより, 切断深さ, 送り速度, 切断速度, 等. ほぼ同じにしかならない) 切削比較試験も同様の環境条件で実施. 結果は、工具寿命を延ばすにはフライス加工の方が有益であることを示しています。.
ドリルやボールエンドミルなど中心刃の工具で切削する場合 (あれは, 切断速度 = 0m/min), 中心刃付近の工具寿命は短縮されることが多い, でも回すよりはまだマシです.
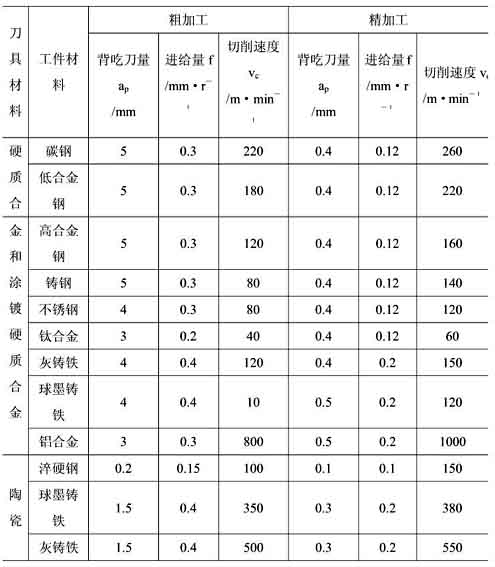
難削材を CNC 加工する場合は、別のツールを選択してください
難削材を切断する場合, 刃先は熱の影響を大きく受けます, 多くの場合、工具寿命が短くなります. 切削方法がフライスの場合, 工具寿命は比較的長くなります. しかし, 難削材は最初から最後まで加工できない. 旋削や穴あけが必要になる場合が常にあります. したがって, 加工効率を向上させるために、さまざまな切断方法に対応する技術的措置を講じる必要があります。
難削材を切断する場合, 工具形状の最適化により工具素材の性能を最大限に発揮. すくい角などの工具形状の選択, 逃げ角, 難削材の特性に合わせた切込み角と適切な刃先処理は、切削精度の向上と工具寿命の延長に大きく影響します。. したがって, 工具の形状を軽視してはなりません. しかし, 高速フライス加工技術の普及と応用により, 最近, 段階的に小さな切込み量を採用し、カッター刃への負担を軽減, アップカットミーリングを採用し、送り速度を向上させました。. したがって, 刃先形状の設計思想も変わった.
難削材の穴あけ時に, トルクと切削熱を低減するには、ドリルの先端角度を大きくして十字研削を行うことが効果的です。. 切削物と切削面の接触面積を最小範囲に制御可能, これは工具寿命を延ばし、切削条件を改善するのに非常に有益です。. ドリルで穴あけ中, 切削熱が刃先付近にこもりやすい, 切りくずの除去も非常に困難です. 難削材を切断する場合, これらの問題はより顕著です, そして十分な注意が払われなければならない.
切りくずの除去を容易にするため, 通常、ドリルの刃先の裏側にクーラントスプレー出口があります。, 十分な水溶性クーラントまたはミストクーラントを供給できる. 切りくずの排出をよりスムーズに, この方法は刃先の冷却効果にも最適です。. 近年では, 優れた潤滑特性を備えたいくつかのコーティング材料が開発されています. これらの材料をドリルビットの表面にコーティングした後、, 加工時に乾式穴あけが可能 3 5D浅穴まで対応.
穴の仕上げにはボーリングを使用します, しかし、最近では従来の連続切断法から輪郭切断などの断続切断法に徐々に変化してきています。. この方法は、切りくず除去性能を向上させ、工具寿命を延ばす上でより有益です。. したがって, 不連続切削用ボーリング工具の設計後, 自動車部品のCNC切断にすぐに適用されました。. ネジ穴加工に関して, 現在はスパイラルカット補間も使用されています, ねじ切り用エンドミルも多数発売.
上記のように, 本来の連続切削から不連続切削への転換は、CNC切削への理解を深めながら行われます。, それは段階的なプロセスです. この切削方法で難削材を切削する場合, 切断の滑らかさを維持することができます, 工具の寿命を延ばすのにも有益です.