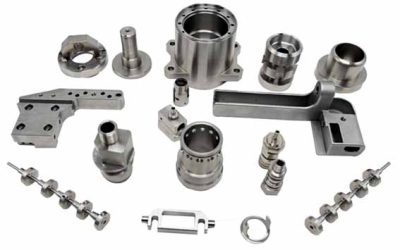
ステンレス部品
ステンレス部品の加工方法? CNC加工技術とステンレス部品の応用
ステンレス鋼は、強度、耐熱性、耐腐食性が重要な場所で広く使用できる汎用性の高い機械加工材料です。. しかし, ステンレス鋼合金を優れた構造材料にするのと同じ特性により、それらの機械加工に使用されるプロセスも複雑になります. 切削工具の特性を慎重に組み合わせる, 形状と切削パラメータの適用により、ステンレス鋼の機械加工作業の生産性が大幅に向上します。.
AUSTENITIC STAINLESS STEELS
They make up the 200 そして 300 series. Their general characteristics are:
Excellent corrosion resistance.
Highly formable.
Not magnetic.
Cold work hardened (Cannot be heat treated).
Excellent weldability.
They have the ability to be functional in extreme temperatures.
They are prone to corrosion cracking.
Composition:
They are obtained by adding elements such as nickel, manganese and nitrogen. The chromium content generally varies between 16 そして 26%. The carbon content is in the range of 0.03 に 0.08%. Chromium provides part of the oxidation resistance and also molybdenum in some of its alloys.
They are used in:
Shafts, valves, ネジ, bushings, nuts, chemical equipment, equipment for hospitals, marine applications, aviation components, food and beverage processing equipment, architectural ornaments, cryogenic vessels, temporary prosthetics, 等.
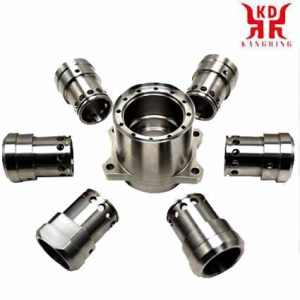
304 ステンレス鋼部品
Alloy evolution
Basic stainless steel alloys are classified as ferritic or martensitic. Ferritic alloys with a chromium content of 10-12 percent cannot be quenched. Martensitic alloys have a higher chromium and carbon content than ferritic stainless steels, as well as manganese and silicon content, resulting in an alloy that can be tempered by heat treatment. 今日, ferritic and martensitic stainless steel alloys are not widely used generally in industrial settings, but rather in household items such as kitchen or garden tools.
As the use of stainless steel has evolved, alloys are frequently applied in situations that require mechanical strength as well as resistance to corrosion. To improve the strength of alloys, metallurgists have added nickel to alloys, so that iron / chromium alloys have been converted to iron / chromium / nickel alloys. These materials are called austenitic stainless steels and are now common in industrial applications where strength and resistance to corrosion and heat are required. These alloys are normally used in the petrochemical industry, in the food sector, since hygiene standards require resistance to corrosion and in general machinery designed for use in harsh environments.
Inevitably, increasing the performance capabilities of an alloy, such as stainless steel, also multiplies machining problems. The corrosion resistance characteristics of martensitic and ferritic stainless steel alloys are basically chemical properties, and as a result these alloys are not much more difficult to machine than plain steels. しかし, the additions of nickel and other elements to austenitic stainless steels produce higher hardness, toughness, resistance to deformation, and thermal properties that decrease machinability.
zero stainless steel 304 vs stainless steel 316
They are the most common stainless steel options. On a mechanical level they are quite similar to each other.
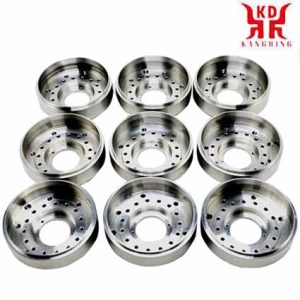
316 ステンレス鋼部品
316 モリブデンを添加すると得られます, これにより、従来のものと比較して高温での機械的抵抗が向上します。 304 (融点は若干低いですが) さまざまな攻撃的な化学薬品に対する耐腐食性, 酸と塩分を含んだ雰囲気. しかし, 304 少し安いです (大規模シリーズの製造において重要).
低炭素「L」タイプ (304Lと316L) 基本形に比べて耐食性が高く、腐食割れの可能性を低減します。. 溶接にも適していますが、機械的耐性は劣ります。. の “H” 炭素量が多いタイプは高温に適しています。.
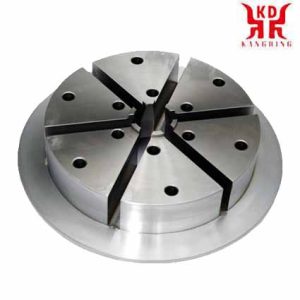
416 ステンレス鋼部品
マルテンサイト系ステンレス鋼
それらは、 400 series (他の部分はフェライトに相当します).
その主な特徴は次のとおりです。:
They can be hardened by heat treatment therefore high levels of mechanical resistance and surface hardness can be developed.
They have greater mechanical, wear and fatigue resistance than austenitics.
Moderate corrosion resistance (less than austenitics).
Good ability to be machined.
They are magnetic.
Due to the high carbon content and the nature of its hardness, it is poorly weldable.
Composition:
They are essentially alloys of chromium and carbon. The chromium content is generally 10.5 に 18% and the carbon content is high, reaching values of up to 1.2%.
They are used in:
Machinery parts, pump shafts, ネジ, bushings, cutlery, ハードウェア, jet engine parts, mining machinery, rifles, valves, aircraft accessories, inserts for fire extinguishers, parts for gas or steam turbines, rivets, 等
416 ステンレス鋼
It is a version of type 410 (most common martensitic stainless steel), where sulfur and phosphorus are added to achieve better machining characteristics (の 400 series is already easier to machine than the 300 series). It has less ductility and formability than 410. It is more economical than the 300 series. They are for use in moderately corrosive environments. It can develop an excellent combination of mechanical resistance and hardness through adequate heat treatment.
440C stainless steel
It is possible to increase the hardness with respect to 410 by adding Carbon and the corrosion resistance is increased thanks to the chromium. Therefore they have high hardness, resistance to abrasion and wear, and good resistance to corrosion. Low machinability. This stainless steel achieves the highest hardness once hardened and the greatest resistance to wear of any steel resistant to corrosion or heat. It is widely used to make knives, bearings, measuring instruments, valve seats, 等.
PRECIPITATION HARDENED STAINLESS STEELS
This family offers an alternative to austenitic stainless steels when it is desired to combine high mechanical characteristics, good corrosion resistance and good machinability. Precipitation-hardenable steels are patented and are often designated by the initials of the manufacturing company.
その主な特徴は次のとおりです。:
Good corrosion resistance.
Good weldability.
They are magnetic.
Very high mechanical strength obtained from hardening by heat aging treatment.
They maintain a high mechanical resistance even at high temperatures.
Composition:
They are mainly iron-chromium-nickel alloys. The chromium content is generally 12 に 18% and the nickel content is between 4% そして 9%.
They are used in:
Mainly in the aerospace and military industry (missiles) for structural components and in motor shafts, instruments, 歯車, 等.
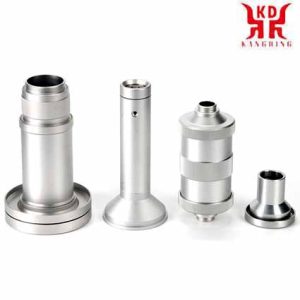
440C stainless steel parts
630 ステンレス鋼 (17-4PH)
It offers high mechanical strength and toughness with excellent corrosion resistance. It can be hardened by aging in a simple way and at a low temperature, which avoids deformations. It is easy to machine before being heat treated.
It has a better behavior in all corrosive environments than 400 series stainless steels, and similar to 304 ステンレス鋼. It can be welded. It may lose the high mechanical strength if heated above the precipitation hardening temperature (495-620 ° C).
Know the alloys
Until recently, machining of austenitic stainless steel was not well understood. The tool manufacturers assumed that since the alloys were stronger, the mechanical cutting forces would be higher and therefore stronger negative geometry tools would have to be applied that would lower the cutting parameters. しかし, this method produced tools with short life, long chips, frequent burrs, unsatisfactory surface roughness, and unwanted vibrations.
In reality, the resulting mechanical cutting forces in austenitic stainless steel are not much greater than those normally used when machining traditional steels. Most of the additional energy consumption required to machine austenitic stainless steels is the result of their thermal properties. Machining is a deformation process, and when machining a strain-resistant austenitic stainless steel, the operation generates excessive heat.
Evacuating that heat from the cutting area is vital. Unfortunately, in addition to being resistant to warping, austenitic stainless steel also has low thermal conductivity. Chips created during the machining of plain steels absorb and transport heat, but austenitic stainless steel chips absorb heat only to a limited extent. また, since the part itself has poor thermal conductivity, excess heat enters the cutting tool, resulting in a short tool life.
Tool manufacturers created carbide substrates to provide enough toughness to withstand the high temperatures that are generated during machining of stainless steel. 同時に, the composition of the substrate is just as important as the edge preparation. A sharper-edged tool cuts stainless steel more than warps it, thereby reducing heat generation.
Aggressive cutting parameters
In the interest of heat removal from the cutting zone, the most efficient way to machine stainless steel is to employ the greatest depths of cut and feeds. The goal is to maximize the amount of heat that is removed from the chips. Since the poor thermal conductivity of stainless steel limits the amount of heat that can be absorbed by each cubic millimeter of chip material, creating longer chips, with more cubic millimeters in volume, will remove more heat. Using greater depths of cut will also reduce the number of passes required to complete a part, an important aspect since austenitic stainless steel has a tendency to warp or harden when machined.
There are practical limitations to these aggressive machining methods. Surface finish requirements, 例えば, will limit maximum feed. The available power of the machine, as well as the force of the cutting tool and the piece, also impose limitations on the aggressiveness of the parameters that can be used.
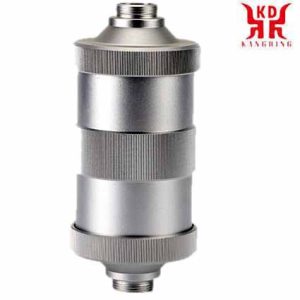
Surface finishing of stainless steel parts
Refrigerant strategies
The problematic thermal properties of austenitic stainless steel alloys suggest that the application of coolant is almost always critical to successful machining. The coolant must be of high quality, with a minimum oil content of eight to nine percent in a water / oil emulsion, compared to the three to four percent oil content typical of many machining operations.
How the coolant is applied is also important. The higher the pressure when applying the coolant to the cutting zone, the better it will do its job. Technologies like Seco’s Jetstream Tooling®, which apply a high pressure coolant flow directly to the cutting zone, are even more effective.
Coatings vs. tool wear
工具基材の表面に堆積された硬質コーティングは、工具表面の高温硬度を強化し、高温環境での耐用年数を向上させます。. しかし, コーティング, 一般的に, ツール基板を熱から絶縁するには厚くする必要があります, 厚いコーティングは非常に鋭利な形状にはうまく接着しません。. 切削工具メーカーは、薄いながらも熱に対する優れたバリアを提供するコーティングを設計する責任があります。.
オーステナイト系ステンレス鋼は延性が高く、切削工具に固着する傾向があります。. コーティングを施すことでボンドの摩耗を防ぐこともできます, 加工された材料が刃先に付着して堆積するときに発生する現象. 付着した材料により刃先の一部が破損する可能性があります, 表面仕上げの低下や工具の故障につながります. コーティングは潤滑性を提供し、スティックの摩耗を制限します, 一方で、より高い切断速度はスティックの摩耗メカニズムを軽減するのにも役立ちます。.
一部のオーステナイト系ステンレス鋼合金には、硬質で摩耗性の介在物が含まれています。, 切削工具の耐摩耗性が向上します, ハードコートとの組み合わせで, 工具の寿命を延ばすことができる.
合金によりチッピングが発生します’ 機械加工中に反りや剪断による自己硬化が発生する傾向がある.
チッピングは、高度に局所的な極度の摩擦摩耗として説明できます。, 適切なコーティングを適用したり、切込み深さを変更して刃先の摩耗ゾーンを広げるなどのその他の操作を行うことで軽減できます。.
ツール開発
Tool builders focus current cutting tool development on finding a balance between tool properties that will provide optimum performance on a specific material to be machined. Carbide quality research seeks a balance between hardness and toughness, so that a tool is not so hard that it fractures but is tough enough to resist deformation.
Similarly, a sharp edge geometry is preferable, although it is not as strong as a rounded edge. したがって, the goal of developing cutting edge geometries is to create tools with a balance between sharp edge and maximum possible robustness.
As part of the development process, tool manufacturers are reviewing their guidelines on tool applications.
Current recommendations on machining parameters are based, for the most part, on the toughness and hardness of traditional steels, オーステナイト系ステンレス鋼やその他の高級合金の加工時に非常に重要な熱要因が考慮されていない. パフォーマンス. 最近, 工具メーカーは学術機関と協力して、特定の材料の熱特性を考慮した工具試験手順を見直し始めています。.
新しいガイドラインには、新しい参考資料の作成が反映されています. 伝統的に, 参考資料に基づいて被削性基準を設定, 合金鋼, 加工中に発生する機械的負荷に応じて. オーステナイト系ステンレス鋼用の別の基準材料セットが存在します。, 速度に関して基準値が設定されているもの, 送りと切込み深さ. 参考資料に関しては, バランスまたは校正係数は、異なる加工特性を持つ材料で最適な生産性を達成するための基本値の変更を決定するために適用されます。.
特定の材料に対する特定の形状
多くの切削工具は、さまざまな材料、さまざまな切削条件および加工パラメータの下で非常に許容可能な性能を提供します。. 中程度の生産性と品質要件を伴う 1 回限りのジョブ向け, これらのツールは費用対効果の高いオプションとなる可能性があります. 最大限のパフォーマンスを達成するには, しかし, 工具メーカーは、特定の材料を加工する場合に高い生産性とプロセスの信頼性を提供する工具を作成するために、さまざまな切削要素を操作してバランスを取る試みを続けています。.
ツールの基本要素には基板が含まれます, コーティング, と幾何学. Each of them is important, and in the best tools they work as a system that produces results beyond the sum of all the separate pieces.
There are differences between the functions that the parts of the tool have. The substrate and coating have passive functions and are designed to offer a balance between hardness and toughness, as well as to resist high temperatures, chemicals, adhesion and abrasive wear. Tool geometry, on the other hand, plays an active role because by altering the geometry you can change the amount of metal that can be removed in a given period of time, the amount of heat that is generated, how chips are formed, and what surface finish can be achieved.
Some basic examples of how performance changes according to different geometries include inserts with traditional Seco turning geometry called e.g. M3 and M5, which have negative cutting edge geometries (0˚ angular distance) and -T edges between the cutting edge and cutting area of the tool. The M3 geometry is a versatile semi-roughing geometry that offers good wear life and chip breakage on a wide range of machining materials. The M5 geometry is designed for demanding high feed roughing applications, combining high cutting edge strength with relatively low cutting forces.
Although versatile, M3 and M5 geometries are robust, not completely sharp-edged, and generate a fair amount of heat as they deform during machining of austenitic stainless steels. In comparison, the tool designs that can be most effective in machining stainless steel include Seco’s MF4 and MF5 geometries, which have the sharpest edge, with positive T-edges. The geometries have been designed to be open and easy to machine to facilitate medium roughing and finishing operations on steels and stainless steels. The MF5 geometry is especially effective in high feed applications.