ステンレス鋼部品のCNC加工, 業界で広く使用されている, 工具業界に大きな課題をもたらす. 新しい旋削インサート材料と切りくず分断形状を開発する場合, 機械加工性を考慮する必要があります. 化学薬品の腐食環境下でも長寿命を実現するステンレス鋼材群, 食べ物, 紙およびパルプ産業での使用はますます増加しています. これらの材料は通常、優れた耐食性を備えたクロムベースの鉄または炭素鋼です。. 比重の異なるクロムとニッケルを含む他のグループのステンレス鋼材料は、高い引張強度と耐食性が必要な航空宇宙産業で使用されています。. 中程度の加工難易度の低ニッケル合金から、加工が難しい高温合金まで多岐にわたります。.
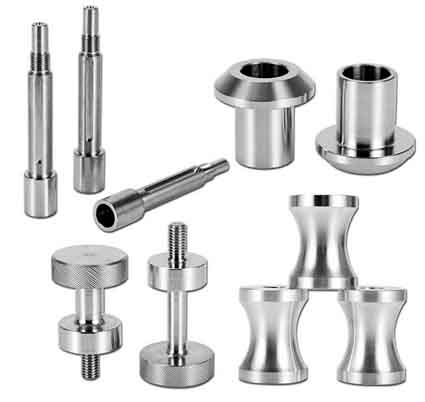
精密ステンレス部品のCNC旋削加工
Machining challenges
Although the machinability of stainless steel is very challenging, they are very sticky and produce sticky chips, built-up edge and coating particles caused by the cutting tool. There are even potential problems such as particle extraction at the junction of the coating and the substrate. しかし, major turning tool companies consider these failure modes when designing the latest core carbide grades and chipbreakers. 最近では, economical solutions for mass production of stainless steels that are easy to turn to medium-difficulty processing range are easily available.
Reorganize cemented carbide materials according to toughness
Seco Tools is one of a complete series of cutting tool suppliers that design new core turning tool materials to improve performance in a wide range of stainless steel processing conditions and applications (including close to the final shape and stainless steel processing). In terms of cemented carbide, Seco has completely reorganized its core turning materials for general machining (TP200) and heavy roughing (TP300). It provides better adhesion between the substrate and the underlying coating and a cutting edge with better toughness. Both materials are coated with a composite coating composed of titanium carbonitride (TiCN), aluminum oxide (Al2O3) and titanium nitride (錫) on a substrate with a cobalt-rich zone.
According to Bob Goulding, Carboloy’s fixed product manager, the restructured material provides important properties for improving machined stainless steel materials. They consist of a very tough coating that can effectively resist pull-out and a smooth and hard top coating that can better resist sticking chips and built-up edge.
Seco Tools is one of a complete series of cutting tool suppliers that design new core turning tool materials to improve performance in a wide range of stainless steel processing conditions and applications (including close to the final shape and stainless steel processing). In terms of cemented carbide, Seco has completely reorganized its core turning materials for general machining (TP200) and heavy roughing (TP300). It provides better adhesion between the substrate and the underlying coating and a cutting edge with better toughness. Both materials are coated with a composite coating composed of titanium carbonitride (TiCN), aluminum oxide (Al2O3) and titanium nitride (錫) on a substrate with a cobalt-rich zone.
According to Bob Goulding, Carboloy’s fixed product manager, the restructured material provides important properties for improving machined stainless steel materials. They consist of a very tough coating that can effectively resist pull-out and a smooth and hard top coating that can better resist sticking chips and built-up edge.
Goulding said that through the coating deposition process-medium temperature chemical vapor deposition (coating at a lower temperature) to improve the toughness and smooth coating, resulting in a long life. He explained, ‘the medium temperature process retains all the hardness and wear resistance of the thicker CVD coating, and also gives you a tougher and smoother coating that minimizes cracks. ’
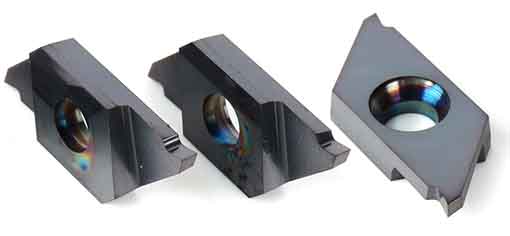
Design high-efficiency stainless steel turning tools
Although both general-purpose and heavy-roughed materials contain a matrix with good toughness and cobalt-rich regions, the ratio of matrix toughness and coating wear resistance is different. According to Goulding, the coating of TP200 material provides excellent wear resistance at higher cutting speeds, while the toughness of the substrate of TP300 material is better, which improves the ability to process high-strength stainless steel at lower speeds. ‘The toughness of our heavy roughing materials is particularly good, combined with the thick MTCVD coating, which makes your cutting edges hard and very tough,’ Goulding said. ‘You get effective wear resistance with outstanding resistance to cutting edge groove wear. Based on these characteristics, Goulding recommends the universal material TP200 for high-speed cutting of free-cutting ferritic stainless steel. The TP300 material is used for low-speed applications of high-strength stainless alloys with medium processing difficulties.
Design a machined stainless steel chipbreaker plan
According to Goulding, there will be models for the correct chipbreaker geometry for stainless steel machining, and Seco’s reorganized core ‘M3’ geometry is used for light to medium load cutting. It can be used for this groove shape for steel finishing and the reorganized core ‘MF2’ groove shape design. The width and angle of the negative chamfer can be varied to provide the cutting edge strength required for effective chip breaking in a wide range of applications including small depth of cut and high feed. The increased cutting edge strength at high feeds helps to control groove wear at the depth of cut when stainless steel is applied and close to the final shape.
According to Goulding, there will be models for the correct chipbreaker geometry for stainless steel machining, and Seco’s reorganized core ‘M3’ geometry is used for light to medium load cutting. It can be used for this groove shape for steel finishing and the reorganized core ‘MF2’ groove shape design. The width and angle of the negative chamfer can be varied to provide the cutting edge strength required for effective chip breaking in a wide range of applications including small depth of cut and high feed. The increased cutting edge strength at high feeds helps to control groove wear at the depth of cut when stainless steel is applied and close to the final shape.
In the entire range of applications, the new geometry design also provides better tool life. One contributing factor is the positive angle of entry, which promotes freer cutting and lower chip temperature. The other is the chip control angle. The strategically placed ‘bump’ on the tool tip replaces a hard chip breaker to control the chip curl required for chip breaking. The straight-pressed bulge helps to limit the contact between the chip and the blade to only two points: the cut-in angle and the bulge itself (cut-out angle). 結果として, the heat and cutting force transferred to the insert are reduced, thereby increasing tool life. The two contact points are also quite wide, so any diffused wear on the rake face caused by the chemical reaction of chips and cemented carbide will not grow up together, causing early failure of the front blade.
In the entire range of applications, the new geometry design also provides better tool life. One contributing factor is the positive angle of entry, which promotes freer cutting and lower chip temperature. The other is the chip control angle. The strategically placed ‘bump’ on the tool tip replaces a hard chip breaker to control the chip curl required for chip breaking. The straight-pressed bulge helps to limit the contact between the chip and the blade to only two points: the cut-in angle and the bulge itself (cut-out angle). 結果として, the heat and cutting force transferred to the insert are reduced, thereby increasing tool life. The two contact points are also quite wide, so any diffused wear on the rake face caused by the chemical reaction of chips and cemented carbide will not grow up together, causing early failure of the front blade.
Although the current core turning materials and chip breakers provide good performance for stainless steel processing in the medium processing difficulty range. しかし, there are no successful cases regarding the extremely difficult to process stainless steel materials. ‘As the nickel/chromium content in stainless steel increases, you usually work at very low speeds,’ Goulding said. ‘You need a strong cutting edge to withstand the extreme pressure required to cut this material. If the cutting edge is too sharp, the blade will chip. ’
To meet these needs under current conditions, Seco provides a tough TP40 cutting material, a ‘MR7’ chipbreaker with high cutting edge strength, and a tough ‘R7’ single-sided geometry. 同時に, the company is studying a new material/chipbreaker combination that resists cracking and provides the required toughness and good wear resistance along the cutting edge in high-alloy stainless steel applications. “We are exploring the possibility of modifying our TP200 and TP300 materials and adding another chipbreaker to meet a wider range of stainless steel materials processing,” Goulding said.