What are the characteristics of medical device parts and the difficulty of CNC machining? Turning and milling of common medical Micro parts. The characteristics of titanium and stainless steel of medical parts materials.
![]() Medical stainless steel parts |
![]() Implant screw of medical titanium alloy |
![]() Medical titanium alloy implants |
Manufacture medical parts using CNC machining
To manufacture CNC-machined parts, the machining company must comply with the ISO 9001 quality requirements, but in the case of the manufacture of medical parts, other types of requirements must be met, complying with the standard of the International Organization for Standardization.
According to this organization, companies involved in the design, production, development, distribution or services of medical parts must demonstrate the ability to provide medical devices that consistently meet customer and regulatory requirements.
このために, the standard used is ISO 13485, recognized by the most important regulators.
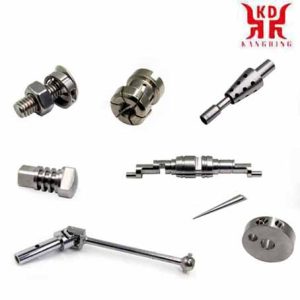
医療用NiTi形状記憶合金の加工
Another factor that increases the complexity of CNC machining is the high tolerance accuracy range. The material, processing accuracy, and surface finish requirements of medical equipment parts and components are very high, which require high reliability of the processing system. したがって, extremely high requirements are also placed on machine tools, 備品, cutting tools, and CAM software.
Requirements for medical CNC machining
Manufacturers that use CNC machining, in addition to complying with all standards and certifications, must take a series of measures. The basic requirements to meet the demands in medical CNC machining are:
Precision machining to very tight tolerances
4 そして 5 axis machining for complex geometries
A demanding level of cleanliness, especially when it comes to implant manufacturing
Wide variety of materials of manufacture, from stainless steel to medical plastics
A surface finish at the highest level
Medical implants by CNC machining process
Without a doubt, one of the most important applications of medical CNC machining is the fabrication and production of body implants.
CNC machining is very suitable for the patient and the creation of specific implants, since the response time is short and there is no cost of tools for the creation of custom implants and not in mass.
Implants are created from metals like titanium and special plastics like PEEK. These materials are strong and biocompatible.
It is essential that they are materials that do not decompose within the human body and that they do not suffer from corrosion.
In any case, there are materials that are difficult to machine since they accumulate heat and the coolant due to contamination issues is prohibited in most cases.
The most common implants created through CNC machining are hip, spine and knee implants.
The most commonly used materials for the manufacture of machined implants are titanium and cobalt-chromium alloys, stainless steels and polyether ether ketone (ピーク).
Manufacture of surgical instruments through CNC machining
CNC machining can be used to create surgical instruments for medical professionals. Surgical scissors, biopsy tubes, cutters, forceps, クランプ, and many more instruments can be created through this manufacturing process.
Without a doubt, CNC machining is the appropriate manufacturing process for this type of instrument, since it can provide the necessary precision and meet the necessary safety requirements.
Manufacturers of medical devices use CNC machining for precision and because tools must be manufactured in small quantities, sometimes even for individual patients. 加えて, perfect surface finishes can be guaranteed to avoid defects.
The most widely used materials for the manufacture of surgical instruments are stainless steels and titanium alloys.
CNC machining to create parts for electronic medical equipment
CNC machines can be used to create parts for more complex equipment than surgical instruments, which consist of one or two metal parts.
There are medical equipment that can comprise many individual parts and many of them can be created from CNC machining.
These pieces can be very small items like switches or larger pieces.
All these parts must be of the highest standard so that the machine of which they are part does not present any subsequent failure. As they are not implants or surgical tools, many more materials can be used because they do not come into direct contact with the patient.
Among the medical equipment that use CNC machined parts we can find: ultrasound equipment, magnetic resonance imaging, diagnostic equipment, monitors …
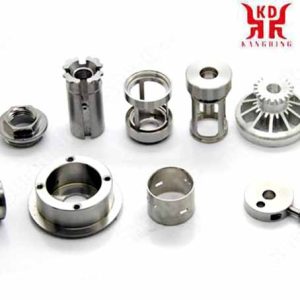
Medical Micro machining parts
Micro machining
Within the medical industry, it is sometimes necessary to manufacture very small parts. For these cases, CNC machining can manufacture very small parts with the necessary precision. Many times the size of these components is much less than 50 microns.
It can be used to manufacture catheters, pacemaker components, miniature screws for implants or devices, ophthalmic components among other uses.
Keep in mind that not all machining centers are suitable for creating this type of component. It requires using especially fine cutting tools and meeting all tolerances for small parts.
Workpieces are usually processed on internationally advanced machining equipment such as Swiss automatic lathes, multi-spindle machine tools and 5-axis rotary tables. These machine tools are mostly characterized by very small size and very compact structure.
The characteristics and requirements of medical device parts processing undoubtedly promote the development of processing technology and solutions. Improve the competitiveness and production efficiency of small and medium-sized enterprises in processing medical accessories.
The manufacturing process by CNC machining is of vital importance for the medical industry due to its perfect precision, versatility in materials and speed. It is useful from the manufacture of surgical tools, to hip implants and numerous medical applications.
Many of the specialized medical machine shops manufacture the parts through the CNC machining process. This is due to the requirement to manufacture these parts with very strict tolerances and with safe and compatible materials. 加えて, they are capable of manufacturing the parts to meet all international requirements and standards.
Parts such as body implants, which require tight tolerances and a perfect level of precision, use CNC machining due to the ideal characteristics that this type of manufacturing presents.
Any workshop with machining machines can manufacture medical parts meeting the established requirements.