Il centro di lavoro esegue multiprocesso (girando, fresatura, perforazione, noioso, toccando, eccetera.) e lavorazione composita multifaccia su parti prismatiche tramite cambio utensile automatico e indicizzazione della tavola. La pratica ha dimostrato che il centro di lavoro composito è effettivamente utile per risolvere le carenze dei lunghi tempi di consegna, basso utilizzo delle risorse, più prodotti in lavorazione e rallentamento del turnover del capitale delle piccole e medie imprese produttrici di macchinari. La lavorazione combinata di tornitura e fresatura ha quindi trovato applicazioni sempre più comuni nella produzione industriale.
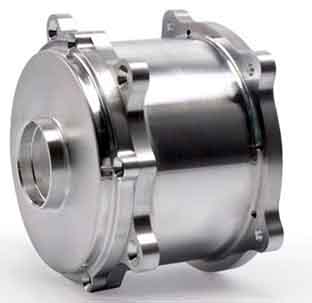
Lavorazione CNC di parti prismatiche
After that, the spindle head of the CNC machining center was automatically rotated 90 degrees to convert the vertical and horizontal modes. The CNC machining center can not only process the 4 sides of the box part, but also process the 5th surface-the top surface. Di conseguenza, the so-called 5-face machining center has been introduced, which can also be regarded as an improvement in the composite processing function of the machining center. Negli ultimi anni, with the price reduction and popularization of 5-axis linkage CNC equipment and programming software, 5-axis linkage (or multi-sided) machining centers have become a new hot spot in the recent international machine tool exhibition. Recentemente, a machining center was introduced, which can mill and drill the 6 faces of the bar in one clamping. The CNC machining center for bar materials is a new development of multi-faceted compound machining capabilities.
In terms of composite processing of prismatic parts with different processing methods, the current eye-catching trend is the combination of milling processing and laser processing or ultrasonic processing. The German DMG company added a laser processing head to the high-speed milling machine a few years ago, and launched the DMU60L (the current model is DML60HSC) for milling and laser combined processing. The machine is equipped with a Q-switched YAG laser with a power of 100W, a beam diameter of 0.1mm, and a processing efficiency of 20mm3/min. After the workpiece (mainly the mold) is clamped on this machine tool, the high-speed milling head is used to complete most of the work, and then the laser is used for finishing in layer cutting. Remove the milling traces of the profile and process the fine parts, including engraving patterns and patterns.
Hard and brittle materials such as glass, ceramica, carburo cementato, eccetera., are difficult to process with traditional techniques. Tuttavia, if high-frequency vibration motion is added to the traditional milling, perforazione, and grinding processes, questo è, ultrasonic technology is combined with cutting processing technology, the processing efficiency will be significantly improved. The DMS series ultrasonic processing machine tool of DMG company in Germany uses the converter on the spindle to convert the electrical high frequency signal of the ultrasonic generator into 20KHz mechanical vibration motion (longitudinal motion). Then the vibration amplitude is amplified and controlled by the voltage regulator, and then all the vibration is transmitted to the milling cutter, drill or grinding wheel made of diamond particles through the patented Sauer conical tool holder. During the machining process, the tool is continuously tapped on the surface of the workpiece 20,000 times per second to separate the surface material of the part in the form of tiny particles. Not only its processing efficiency is increased by 5 times compared with the traditional method, but also the surface roughness can reach Ra<0.2µm. DMS series ultrasonic processing machine tools have two types: 3-axis linkage control and 5-axis linkage control. The spindle speed is 20~6000r/min, and the tool magazine and automatic tool changer are also optional. So it becomes a machine tool that not only has the function of ultrasonic processing, but also can perform multi-process compound processing such as drilling, fresatura, and grinding.