La calibrazione degli utensili per macchine utensili CNC è un'abilità importante nella lavorazione. La precisione dell'impostazione dell'utensile determina la precisione della lavorazione del pezzo, e l'efficienza dello strumento di calibrazione influisce direttamente sull'efficienza di lavorazione della parte. Il presetting utensile è molto importante per le operazioni di lavorazione della macchina utensile.
Dopo aver acceso il tornio CNC, il rendimento pari a zero (Punto di riferimento) l'operazione deve essere eseguita. Il suo scopo è stabilire un riferimento unificato per la misurazione della posizione, controllo, e visualizzazione del tornio CNC, questo è, l'utensile ritorna all'origine della macchina utensile. L'origine della macchina utensile è solitamente alla massima corsa positiva dell'utensile, e la sua posizione è determinata dal sensore di posizione della macchina utensile. Dopo che la macchina utensile ritorna a zero, la distanza tra la posizione dell'utensile (punta dello strumento) e l'origine della macchina è fissa. Perciò, per facilitare la calibrazione e la lavorazione degli utensili, la posizione della punta dell'utensile dopo il ritorno allo zero macchina può essere considerata come l'origine della macchina.
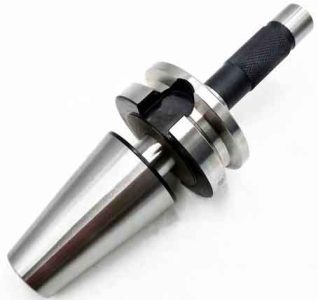
Metodo di calibrazione utensile per lavorazione CNC
La calibrazione dell'utensile è il processo di definizione del sistema di coordinate del pezzo nel sistema di coordinate della macchina utensile CNC, e far coincidere l'origine del sistema di coordinate del pezzo con l'origine della programmazione. Misurare la distanza tra il punto di programmazione della punta dell'utensile nel sistema di coordinate della macchina utensile e l'origine della lavorazione nelle direzioni X e Z mediante taglio di prova o metodi senza contatto, e impostare il valore sui parametri macchina. Attraverso la chiamata del programma, viene stabilito il sistema di coordinate del pezzo. Il valore assoluto delle coordinate del punto base nel programma si basa sull'origine del sistema di coordinate del pezzo stabilito, e il contorno della parte viene elaborato.
Esistono molti modi per calibrare il coltello sul tornio CNC, e il metodo del taglio di prova è comunemente usato nel lavoro. Di seguito viene presentato FANUC-0Il metodo dello strumento di calibrazione comunemente utilizzato per il tornio CNC.
1. Misurare e inserire il metodo di offset utensile
1) Tagliare di prova il cerchio esterno del pezzo con l'utensile selezionato, e allineare lo strumento nella direzione X. Nella modalità di funzionamento manuale, prova a tagliare il cerchio esterno, mantenere invariata la direzione X, e l'utensile esce lungo l'asse Z. Utilizzare un calibro a corsoio per misurare il valore del diametro α del cerchio esterno tagliato, e fare clic su “COMPENSAZIONE” per accedere all'interfaccia di impostazione dei parametri di compensazione della forma. Spostare il cursore sulla posizione X della compensazione utensile, inserisci Xα, e fare clic sul tasto funzione [Misurare]. Il controllo numerico calcola automaticamente le coordinate della punta attuale dell'utensile in direzione X nel sistema di coordinate della macchina utensile, e la direzione X completa la calibrazione dello strumento.
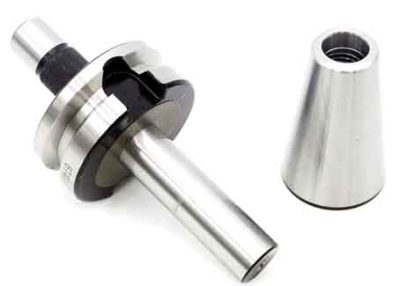
Calibrazione della macchina utensile
2) Utilizzare l'utensile selezionato per tagliare la faccia finale e calibrare l'utensile nella direzione Z. Nella modalità di funzionamento manuale, l'utensile taglia la faccia finale del pezzo al centro. Quindi la direzione Z rimane immobile, e lo strumento esce nella direzione X. Accedere all'interfaccia di impostazione dei parametri di compensazione della forma, spostare il cursore nella posizione corrispondente della coordinata Z della compensazione utensile, inserisci Z0, premi il [Misurare] tasto programmabile, il correttore utensile corrispondente viene immesso automaticamente, e l'impostazione dello strumento è completata. Questo metodo consiste nell'impostare l'origine della lavorazione al centro dell'estremità destra del pezzo, che è un metodo comune per le parti generali dell'albero. Se è una parte simmetrica sinistra-destra, l'origine della lavorazione deve essere impostata al centro simmetrico del pezzo, quindi inserire Zβ, β è la metà della lunghezza assiale della parte.
Quindi inserire il valore del raggio dell'arco della punta dell'utensile R e il numero di posizione dell'utensile T in base alla dimensione geometrica e alla posizione di installazione dell'utensile, Per esempio:
Per il n. 1 attrezzo, il raggio dell'arco della punta dell'utensile è R=0,8 mm, spostare il cursore nella posizione corrispondente al n. 1 strumento sotto R, digitare 0.8, immettere il numero di posizione dell'utensile nella posizione corrispondente di T, e premere “INGRESSO” immettere, quindi può essere utilizzato per l'elaborazione.
2. Coltello di calibrazione in direzione Z dopo la rotazione del pezzo
Dopo che il pezzo è stato girato, la lavorazione deve garantire la lunghezza totale del pezzo dopo la lavorazione. Perciò, il coltello deve essere calibrato due volte. La direzione X è la stessa del metodo di impostazione utensile precedente. I passaggi per l'impostazione dell'utensile in direzione Z sono i seguenti:
Tagliare la faccia finale del pezzo al centro, mantenere ferma la direzione Z, premi il pulsante X avanti, e lo strumento esce. Misurare la lunghezza totale del pezzo grezzo in direzione Z come Z1, la lunghezza totale richiesta del pezzo è Z, e la differenza di lunghezza è ∆=Z1-Z. Prima di eseguire il programma, è necessario innanzitutto impostare il punto O come origine della lavorazione (Guarda la figura 1), e accedere all'interfaccia di impostazione dei parametri di compensazione della forma. Spostare il cursore sulla posizione della coordinata Z, immettere Z∆, (∆ is the Z coordinate value of the current position of the tool tip in the newly created workpiece coordinates), premi il [Misurare] tasto programmabile, and the corresponding tool offset is automatically input.
3. G92 sets the workpiece coordinate system
1) Use an external turning tool to first try turning the external circle. After measuring the diameter of the outer circle, the tool is withdrawn in the positive direction of the Z axis, and the spindle stops. Note down the absolute coordinate value X1 of the tool in the machine tool coordinate system at this time, and measure the outer circle diameter D at the same time.
2) Cut the end face to the center, X does not move, and exit along the Z direction. Write down the absolute coordinate value Z1 of the tool in the machine tool coordinate system at this time;
3) Select the starting point. The starting point should be selected outside the workpiece. If the starting point is set at 50mm in the X direction and 50mm in the Z direction from the center of the right end face. Then the position of the starting point in the machine coordinate system X = X1-D+100.0 (diameter programming), Z=Z1+50.0;
4) Adjust the tool to reach the point. Before executing the program with the workpiece coordinate system set by G92, the tool must be adjusted to the up-point position. Methods as below:
First move the tool to the position close to the starting point in the manual state, and then adjust the magnification by the handwheel to reach the precise position;
5) In questo momento, the starting point of the program must be: G92 X100.0 Z50.0
Descrizione:
(1) Lo strumento deve essere calibrato prima di eseguire questa istruzione, e la punta dell'utensile deve essere posizionata nella posizione del punto iniziale richiesta dal programma regolando la macchina utensile;
(2) L'esecuzione del comando G92 non provocherà alcun movimento della macchina utensile. Lascia semplicemente che il sistema sostituisca il vecchio valore delle coordinate con il nuovo valore delle coordinate, stabilendo così un nuovo sistema di coordinate.
Quando si utilizza il metodo di taglio di prova per verificare l'utensile, l'errore dello strumento di verifica deriva principalmente dall'errore di misurazione dopo il taglio di prova del pezzo e dall'errore causato dall'ispezione visiva durante l'operazione. Le principali misure per ridurre l'errore di impostazione utensile sono: L'atteggiamento deve essere rigoroso, l'operazione deve essere attenta, e la lettura deve essere accurata; Durante l'elaborazione, considerare l'influenza della precisione di posizionamento ripetuto della macchina utensile sulla precisione di presetting utensile e l'influenza dell'altezza di installazione del punto di posizionamento dell'utensile sulla precisione di presetting utensile; Dopo l'impostazione dell'utensile, il valore di compensazione dell'utensile deve essere corretto in base all'errore tra la dimensione effettiva del pezzo lavorato dall'utensile e la dimensione programmata.
I torni a controllo numerico hanno una varietà di sistemi di controllo. I metodi di calibrazione dello strumento includono la calibrazione manuale, calibrazione del calibratore esterno della macchina utensile, e calibrazione automatica. L'impostazione manuale dell'utensile adotta la modalità di “prova di taglio-misurazione-regolazione”, che è semplice ed economico, impiega molto tempo nella macchina utensile, e ha un grosso errore. Utilizzando il calibratore per il presetting utensile è possibile calcolare automaticamente la differenza tra la lunghezza di ciascun coltello e quella del coltello standard, e memorizzarlo nel sistema. Durante l'elaborazione di altre parti, è necessario solo il coltello standard, che consente di risparmiare notevolmente tempo di assistenza al lavoro. Inoltre, l'uso di uno strumento di presetting utensile per il presetting utensile può eliminare gli errori durante la misurazione e migliorare notevolmente la precisione del presetting utensile. L'impostazione automatica dell'utensile è realizzata dal sistema di rilevamento della punta dell'utensile. La punta dell'utensile si avvicina al sensore tattile ad una velocità impostata. Quando la punta dello strumento tocca il sensore e invia un segnale, il sistema CNC registra immediatamente il valore della coordinata in quel momento e corregge automaticamente il valore di compensazione utensile. Although the principle of inputting parameters of external tool setting instrument and automatic tool setting is similar to that of manual tool setting, the principle and method of measurement are different, the degree of automation is high, and the work efficiency is improved.
Each tool calibration method has its own advantages and disadvantages, and operators can use them flexibly according to their actual needs. In questo modo, the entire tool setting work is simple, and the processing quality can be ensured, and the auxiliary time can be greatly saved, and the production efficiency can be effectively improved.