Nella produzione di utensili e stampi compaiono contorni complessi, e sono prodotti di serie. Prima dell'emergere delle macchine utensili CNC, gli stampi per forgiatura e quelli utilizzati nell'industria automobilistica erano realizzati principalmente a mano. Dopo gli anni '70, Le macchine utensili CNC sono state ampiamente utilizzate nella produzione di utensili e stampi. I contorni di base di profili complessi vengono solitamente lavorati mediante fresatura, e le macchine utensili CNC circostanti sono inizialmente impostate sul collegamento a tre assi.
Dopo essere entrati negli anni '80, Le fresatrici a cinque assi sono state ampiamente utilizzate nella lavorazione di superfici complesse. Il contorno del pezzo dopo la fresatura è molto vicino alla forma finale del pezzo, ma l'ultimo processo di finitura è ancora manuale. Alla fine degli anni '80, la tecnologia di taglio ad alta velocità si è gradualmente sviluppata e maturata, e la sua applicazione nella produzione industriale è stata continuamente migliorata in termini di macchine utensili, utensili da taglio e altre tecnologie correlate. Poiché il taglio ad alta velocità può raddoppiare la velocità di avanzamento, il passo di alimentazione può essere ridotto senza ridurre l'efficienza produttiva. This provides a prerequisite for improving the shape accuracy of the workpiece and reducing the surface roughness. Attualmente, most of the workpieces processed by high-speed milling no longer need the last manual processing procedure, but can be directly put into use.
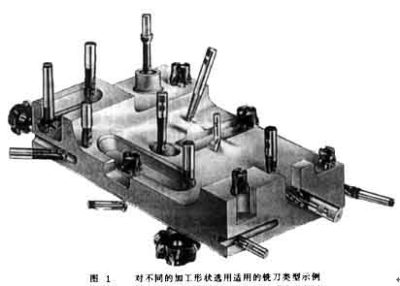
5-lavorazione assiale di profili complessi
New tool materials: such as alumina-based ceramics, silicon nitride-based ceramics, cermets, carburo cementato, especially the continuous development of superhard coatings, making hard face milling possible. The mold surface can be milled to shape after quenching, thereby avoiding deformation caused by quenching after milling. This not only simplifies the machining process, but also improves the accuracy of the workpiece.
Inoltre, with the application of precision forging in die manufacturing, the die blank after forging already has its designed basic shape, e il sovrametallo residuo è insignificante rispetto alla fresatura dell'intero pezzo grezzo. In questo caso, oltre alla fresatura, può anche essere lavorato mediante macinazione ad alta efficienza. Rispetto alla fresatura di spianatura dura, la rettifica ad alta efficienza non solo può migliorare la precisione della forma del pezzo, ma migliora anche la rugosità superficiale del pezzo. Esistono molti metodi di macinazione ad alta efficienza, solitamente rettifica ad alta velocità con mole sferiche e rettifica a nastro con mole a nastro di piccolo diametro.
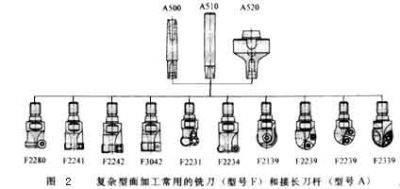
Tipo di fresa
Le superfici tridimensionali a forma libera di utensili e stampi vengono solitamente lavorate su un centro di lavoro a 5 assi. Poiché il materiale del pezzo è principalmente acciaio legato o acciaio per utensili, la struttura della macchina utensile e del sistema di controllo numerico devono considerare i requisiti di produttività e precisione del pezzo nel processo di lavorazione, e realizzare il layout e l'ottimizzazione appropriati in base a ciò. Per garantire che la macchina utensile non subisca troppa deformazione durante il taglio di vari materiali per stampi, la rigidità della macchina utensile dovrebbe essere la prima priorità quando si determina il layout della macchina. Centro di lavoro ad assi più grandi, la maggior parte di una struttura a portale, alcuni centri di lavoro a cinque assi di piccole dimensioni vengono talvolta utilizzati anche con strutture a colonne alte.
Dall'inizio degli anni '90, quasi tutte le forme complesse sono state elaborate mediante taglio ad alta velocità in produzione. Lo scopo è migliorare l’efficienza produttiva, ridurre il costo del prodotto, and at the same time improve the shape accuracy of the workpiece and reduce the surface roughness. In order to meet the needs of high-speed cutting, the spindle of the machine tool almost without exception uses an electric spindle. The spindle speed is continuously variable according to the diameter of the tool used, and the speed ranges from several thousand revolutions per minute to tens of thousands of revolutions per minute. The drive system of the sliding table is also different from conventional machining centers in high-speed cutting. Commonly used system with high-speed drive nut screw assembly and linear motor drive, a maximum feed speed can reach 100m / min or more.
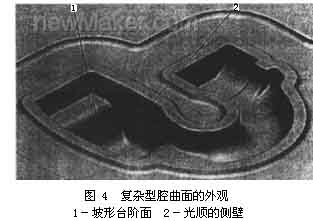
The appearance drawing of CNC machining complex cavity surface
When processing complex surfaces, anche il sistema CNC della macchina utensile deve soddisfare alcuni requisiti particolari. Per esempio, I programmi di lavorazione CNC per superfici complesse vengono generalmente generati su software CAD/CAM. Un programma profilato richiede spesso diversi megabyte (Byte) di spazio di archiviazione, e non è più possibile trasferire programmi NC tramite dischetto. Perciò, il sistema CNC deve avere la funzione di collegamento in rete con altri sistemi informatici per ricevere il programma CNC direttamente dal CAD/CAM. Inoltre, il sistema di controllo numerico deve inoltre adottare una tecnologia di controllo avanzata, Prima di tutto, richiede la funzione di LookAhead. In altre parole, prima che la macchina utensile elabori una determinata traccia, il sistema dati analizza preventivamente la superficie da lavorare. According to the curvature of each point of the curved surface and the connection relationship of each adjacent point, the feed speed of the machine tool is appropriately adjusted to achieve the highest productivity under the premise of ensuring the accuracy of the workpiece. In order to reduce dynamic errors during processing, the new servo error correcting data using a conventional tandem system is no longer proportional integral derivative (PID) controller, instead of using the state regulator by compensating for the position and speed state parameters. Using this kind of regulator can completely eliminate the drive hysteresis error, compensate for the nonlinear error caused by the gap or friction, and even offset certain vibrations of the machine tool. In modo da soddisfare i requisiti di miglioramento della precisione della forma del pezzo e di riduzione della rugosità superficiale.
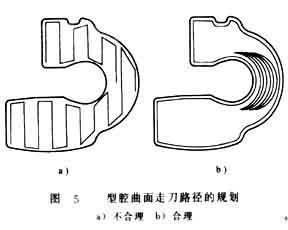
Impostazione del percorso di taglio della superficie della cavità
Il sistema di utensili svolge un ruolo decisivo nell'efficienza produttiva e nella qualità della lavorazione durante la lavorazione di profili complessi. Quando si seleziona un sistema di utensili da taglio, dobbiamo innanzitutto partire dalla geometria dei pezzi da lavorare, e utilizzare ragionevolmente i tipi di utensili da taglio. Come mostrato in figura 1, la geometria di ciascuna parte è molto diversa. Se per la lavorazione viene utilizzata solo una fresa con testa sferica, è necessario selezionare una fresa a testa sferica di diametro piccolo, il che rende difficile migliorare l’efficienza del trattamento. Inoltre, il raggio dell'arco di alcune parti è così piccolo che non può essere lavorato nemmeno con una piccola fresa a sfera. Perciò, taking into account the requirements of both production efficiency and workpiece shape, other types of milling cutters must be equipped on the five-axis machining center for processing complex profiles, such as end mills and three-face milling cutters.
Figura 2 shows some types of milling cutters. As long as the size permits, regardless of the shape of the tool, the cutting edge should be a milling insert with a convertible clamp. Such knives can be combined in a variety of ways because of the blade and the body, and the blade and the body can be produced by different companies. Perciò, large-scale specialized production can be formed, which not only helps to improve the quality of the tool, but also helps to reduce the production cost of the tool.
Attualmente, most of the indexable blades on the market use CVD coated carbide blades. In order to achieve higher pseudo-abrasion resistance, the indexable inserts are all multi-layered coatings. Bizhi Al2O3 can improve the chemical stability of the blade. TiN and TiCN can enhance the wear resistance of the blade. In order to enhance the sharpness of the blade, in addition to the low-temperature CVD method, the coating can also be produced by the PVD method. Some processing has very strict requirements on the blade. The blade must have a sharp cutting edge to reduce the roughness of the finished surface, but also have a high wear resistance to ensure the shape accuracy of the workpiece. In questo caso, a combination of multiple coatings must be used. In order to ensure that the use of some blades is foolproof, il numero di strati di rivestimento può essere pari a 100.
La durata dell'utensile è strettamente correlata alla velocità di avanzamento, velocità di taglio e profondità di taglio. La quantità di taglio ottimale è spesso un intervallo limitato, che dovrebbe essere determinato in base allo strumento specifico e al materiale del pezzo.
Inoltre, strategie di taglio come: La pianificazione del percorso utensile, il vettore normale della superficie dell'asse dell'utensile (la direzione normale della superficie in questo punto) oppure i diversi metodi lungo il vettore tangente alla superficie (la direzione tangente della superficie in questo punto), eccetera., sono un fattore chiave anche per la lavorazione di superfici complesse . Non influisce solo sulla rugosità superficiale del pezzo lavorato, ma influisce anche sulla forma e sulla precisione dimensionale del pezzo. Figura 3 mostra le diverse strategie di taglio utilizzate durante la lavorazione di una superficie cilindrica. Per tagliare in direzione circonferenziale, il percorso utensile deve essere interpolato nel collegamento a due assi. Quando si taglia lungo la direzione della generatrice, lo strumento deve eseguire solo l'interpolazione ad asse singolo. Inoltre, metodi di taglio diversi comportano grandi differenze nell'usura dell'utensile. L'usura dell'utensile durante la fresatura concorde è notevolmente inferiore rispetto a quella della fresatura discorde, e l'usura durante la fresatura alternativa è molto maggiore di quella della fresatura unidirezionale.
Al fine di migliorare la stabilità del processo di lavorazione, quando si ottimizza la strategia di taglio, deve essere garantita la continuità del taglio, inoltre il movimento di taglio e la corsa a vuoto devono essere ridotti il più possibile per abbreviare il tempo di taglio. When the rough milling of steel, must ensure continuous climb milling, to minimize the peak of the cutting blade during cutting of the amount of fluctuation.
When processing the workpiece shown in Figure 4, if the row cut trajectory section processing shown in Figure 5a is used; The movement of the tool is very unreasonable, the cutting conditions are very unsatisfactory, the processing time is 33min, and the surface roughness of the workpiece is 6-9μm. If you switch to the circle-cutting path shown in Figure 5b for processing, the processing time is about 27 minuti. Allo stesso tempo, the roughness of the workpiece can also be reduced to 2 ~ 4μm.