Qu'est-ce qu'un tour CNC? Comment configurer le tournage du tour CNC?
Le tour à commande numérique ou tour CNC fait référence à une machine-outil de type tour utilisée pour usiner des pièces de révolution à l'aide d'un logiciel informatique utilisant des données alphanumériques., suivant le cartésien X, Axes Y. Il sert à produire en quantité et avec précision, parce que l'ordinateur qui intègre le contrôle est en charge de l'exécution de la pièce.
A CNC lathe can do all the jobs that are normally done by different types of lathe such as parallel, copier, revolving, automatic and even vertical ones. Its profitability depends on the type of part that is machined and the number of parts that have to be machined in a series.
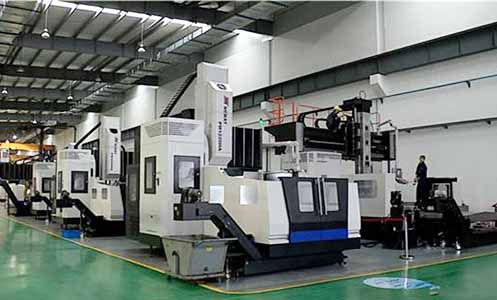
tour CNC
Numerical control
The first development in the area of numerical control was carried out by the American inventor John T. Parsons together with his employee Frank L. Stulen, in the 1940s. The numerical control (CN) is an automation system for machine tools in which numbers, letters and symbols are used. When the task to be performed changes, the instruction program is changed.
The characters established for these programs are governed by DIN 66024 et 66025 standards. Some of the characters are:
N – corresponds to the block or sequence number. Après la lettre, le nombre de blocs à programmer est placé. Le nombre de blocs doit être compris entre 1 et 999.
Fonctionnement
Le “X” et “Z” les axes peuvent se déplacer simultanément entrelacés, aboutissant à un usinage conique ou sphérique selon la géométrie des pièces.
Les outils sont placés dans des porte-outils fixés sur une tête pouvant accueillir jusqu'à 20 différents porte-outils qui tournent selon le programme choisi, faciliter la réalisation de pièces complexes.
Dans le programme d'usinage, la vitesse de rotation de la tête de la pièce, l'avance des chariots longitudinaux et transversaux et les coordonnées d'exécution de la pièce peuvent être saisies en paramètres. La machine fonctionne à des vitesses de coupe et d'avance bien supérieures à celles des tours conventionnels., des outils en métal dur ou en céramique sont donc utilisés pour réduire la fatigue du matériau.
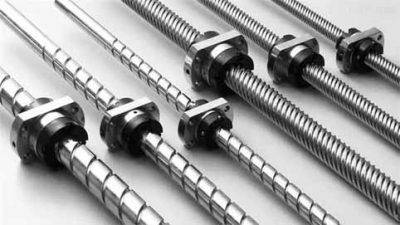
Ball screw with ground rounded thread
General architecture of a CNC lathe
The characteristics of CNC lathes compared to a normal universal lathe are the following:
Motor and main head
This motor limits the real power of the machine and is what causes the rotating movement of the parts. Normally, current CNC lathes are equipped with a direct current motor, which acts directly on the spindle with a transmission by pulleys interposed between the location of the motor and the spindle, being unnecessary any type of transmission by gears.
These DC motors provide an almost infinite range of rotation speeds from zero to a maximum determined by the characteristics of the motor, which is programmable with the execution program of each part. Many engines incorporate two speed ranges, one for slow speeds and the other for fast speeds, in order to obtain the most favorable torque. The spindle has at its end the adaptation for the corresponding claw plates and a hole to be able to work with a bar.
The characteristics of the motor and main spindle of a CNC lathe can be the following:
Main spindle bore diameter: 100 mm
Main spindle nose: DIN 55027 No. 8 / Camclock No. 8
Morse cone No. 2
Speed range: 2
Variable spindle speed: I: 0-564 rpm II: 564-2000 tr/min
Motor power: 15 kW
Movable bench and trolleys
In order to facilitate the rapid movement of the longitudinal and transverse carriages, the guides on which they slide are tempered and ground with a hardness of the order of 450 HB. These guides have an automated permanent greasing system.
Les axes des chariots sont constitués de billes trempées et rectifiées assurant une grande précision dans les mouvements, ces broches fonctionnent selon le principe de recirculation des billes, au moyen duquel une vis sans fin est couplée aux chariots respectifs. Quand la vis sans fin tourne, le chariot se déplace longitudinalement à travers les guides du lit. Ces vis n'ont aucun jeu lors du changement de sens de rotation et offrent peu de résistance. Pour éviter les dommages dus à une collision du chariot avec un obstacle, ils intègrent un embrayage qui débraye l'ensemble et arrête la force d'avance.
Chaque voiture dispose d'un moteur indépendant qui peut être des servomoteurs ou des moteurs encodeurs caractérisés par une puissance et un couple élevés à bas régime.. Ces moteurs fonctionnent comme un moteur AC conventionnel, but with an encoder connected to it. The encoder controls the exact revolutions given by the motor and brakes at the exact point that marks the programmed position of the tool.
D'autre part, the structure of the bed determines the maximum dimensions of the pieces that can be machined. Example of the specifications of the bed of a CNC lathe:
Height between points: 375 mm
Diameter admitted on bed: 760 mm
Diameter over longitudinal carriage 675
Diameter admitted on cross slide. 470 mm
Z, X axis working feed. 0-10000 mm / min
Rapid movements Z, X axes 15/10 m / min
Longitudinal thrust force 9050 N
Transverse thrust force 9050 N
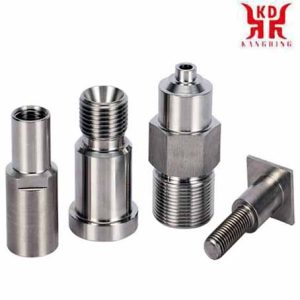
Fasteners turned on CNC lathes
Fasteners turned on CNC lathes
Trolley positioning adjustment
Despite the quality of the elements that intervene in the mobility of the longitudinal and transversal carriages, there is no total guarantee of being able to achieve the position of the tools in the programmed position.
To correct possible positioning errors there are two electronic systems, one of them direct and the other indirect. The direct positioning adjustment system uses a measurement ruler located in each of the bench guides, where an optical reader acts that accurately measures the position of the carriage. transferring existing deviations to the CPU (Central Processing Unit) where it is automatically reprogrammed until the correct position is achieved.
Tool holders
The CNC lathe uses a drum as a tool holder where six to twenty different tools can be located, depending on the size of the lathe, or its complexity. The tool change is controlled by the machining program, and at each change, les chariots reviennent dans une position où s'effectuent la rotation et la sélection de l'outil approprié pour continuer le cycle d'usinage. Lorsque l'usinage de la pièce est terminé, les chariots reviennent à la position initiale de retrait de la zone de travail afin qu'il soit possible de changer de pièces sans problème. Le tambour porte-outils, connu sous le nom de revolver, intègre un servomoteur qui le fait tourner, et un système hydraulique ou pneumatique qui verrouille le revolver, donnant ainsi une précision qui se situe normalement entre 0.5 et 1 micron d'un millimètre. Les outils doivent être ajustés aux coordonnées appropriées dans un accessoire externe aux tours selon les dimensions indiquées par le programme.. Dans la plupart des cas, des inserts en carbure interchangeables sont utilisés, ce qui signifie que lorsque l'insert doit être remplacé, il n'est pas nécessaire de retirer le porte-outil de son logement.
RÉGLEUR D'OUTILS
Cet accessoire nous permet de faciliter le réglage des outils à utiliser en usinage. Les palpeurs de réglage d'outils s'installent facilement sur les centres d'usinage CNC et les centres de tournage, permettant un fonctionnement automatisé avec les avantages suivants:
Gain de temps significatif grâce à une réduction des temps d’arrêt des machines
Mesure précise de la longueur et du diamètre de l'outil
Calcul et correction automatiques de la compensation d'outil
Élimination des erreurs de configuration manuelle
Accessoires et périphériques
Les accessoires de machine sont connus comme les équipements qui, dans le cadre de celui-ci, sont acquis auprès d’un fournisseur externe, parce qu'ils sont universellement applicables pour ce type de machine. Par exemple, une batterie de voiture en est un accessoire.
Toutes les machines dotées d'un fonctionnement CNC intégré nécessitent une série d'accessoires qui, dans le cas d'un tour, sont spécifiés ci-dessous.:
CPU (Unité de contrôle de processus)
Graphiques dynamiques de solides et de chemins
Éditeur de profil
Périphériques d'entrée
Périphériques de sortie
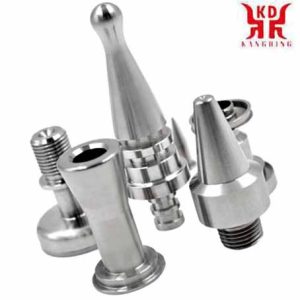
Pièces en acier inoxydable tournées par tours CNC
Pièces en acier inoxydable tournées par tours CNC
UCP (Central Processing Unit)
Article principal: Unité centrale de traitement
Le CPU ou CPU est le cerveau de calcul de la machine, grâce au microprocesseur qu'il intègre. La puissance de calcul de la machine est déterminée par le microprocesseur installé. N'importe quel processeur du marché peut être installé sur chaque machine, Par exemple: FAGOR, FANUC, SIEMENS, etc.. La chose normale est que le client choisit les caractéristiques de la machine qu'il souhaite puis choisit le CPU qui lui convient le mieux en termes de performances, prix, service, etc..
The main functions entrusted to the PCU is to develop the command and control orders that the machine must have in accordance with the machining program that the programmer has established. such as calculating the exact position that the tools must have throughout the work process, by controlling the displacement of the corresponding longitudinal and transverse carriages. You must also control the technological factors of machining, that is the spindle revolutions and the work and rapid travel feeds as well as the tool change.
D'autre part, the CPU integrates the different memories of the system, which can be EPROM, ROM, RAM and BUFFER, which serve to store the programs and act as a hard disk of any computer.
Le périphérique d’entrée le plus important et le plus important est le clavier installé sur le panneau de commande de la machine., d'où vous pouvez apporter des corrections et des modifications au programme initial, développer même un programme d'usinage individuel. Il existe de nombreux types de périphériques d'entrée avec plus ou moins de complexité, qui, s'ils doivent être construits, résistent aux environnements agressifs tels que ceux que l'on trouve dans les ateliers.
Le périphérique de sortie le plus important est le moniteur, c'est là que nous sommes informés du processus d'exécution de l'usinage et que nous pouvons voir toutes les valeurs de chaque séquence. Nous pouvons également contrôler le mouvement manuel des chariots et autres pièces mobiles de la machine..
Numéro de séquence N
Sequence refers to the set of non-contradictory orders that can be given to the machine at once. They are identified by the letter N, and up to 9999 successive orders can be given on a normal lathe. If the program is not very long, they can be numbered from 10 à 10, in case it is necessary to introduce an unforeseen complementary order, so we will have N10, N20, N30, etc.. or we could have, N10, N11, N20, etc..
Preparatory functions G
Under the letter G accompanied by a number are grouped a wide variety of functions that allow the lathe to perform the appropriate and necessary tasks for its work.
There are five basic types of preparatory functions:
Mobility functions.
Technological functions.
Conversion functions.
Special machining functions.
Modal functions.
1- Mobility functions The most important mobility functions are the following:
G00. Fast scrolling. Indicates the fastest possible movement of the tool carriage, from the reference point to the point where each tool starts work. Special care must be taken in the use of this function since the trajectory is not controlled by the user but rather the lathe acts based solely on the maximum travel speed. You never mechanize with it. It only acts at the beginning of the program, each time there is a tool change, and at the end of the program when returning to the reference point.
G01. Linear interpolation. Indicates that the tool is moving at the programmed work feedrate, allowing classic turning and facing operations as well as cone machining.
G02 Circular interpolation to the right (clockwise) It is used when it is necessary to machine spherical or radial areas with controlled speed.
G03. Circular interpolation to the left (counterclockwise). It is used when it is necessary to machine empty spherical areas, or left-hand radii.
There are other G mobility functions, less important and depending on the equipment that is installed in the machine.
2- Technological functions The technological functions are those that refer to the way of programming the spindle speed and the work advance. The spindle rotation speed can be programmed at the desired revolutions per minute, for which function G97 will be preceded, or it can be programmed to rotate at a constant cutting speed in m / min. In this case it is indicated with function G96. The same happens with the work feedrate, if you want to program the feedrate in mm / rev, the G95 function is prepended and if you want to work in mm / min the G94 function is prepended.
3- Conversion functions The most important function of this group is the one that corresponds to the zero offset to locate the part zero that is carried out by means of the G59 function. There are also functions if the dimension is in inches or millimeters. Although the one that is going to be used normally has already been preset. Another case of conversion is if it is programmed with absolute dimensions or incremental dimensions.
4- Special machining functions. The most popular of these functions is the one corresponding to a threading cycle represented by function G33. Other functions of this type are facing, forage, tapotement, alésage, etc..
5- Modal functions. In CNC programs, there are functions that, once programmed, remain active until a contrary function is programmed, or the program is terminated. These functions are called modal functions. As many functions as you want can be programmed in a block, as long as they are not incompatible with each other. Par exemple, functions G00 and G01 cannot be programmed in a block.
Advantages and disadvantages of CNC lathes compared to conventional ones
Avantage:
They allow to obtain greater precision in machining.
They allow machining more complex parts.
It can be easily changed from machining one part to another.
Operator errors are reduced.
CNC lathes are getting cheaper.
Machining times are reduced.
As disadvantages the following can be indicated:
Need to carry out a program prior to machining the first part.
High cost of tools and accessories, which implies a high investment.
Convenience of having a large occupation for the machine due to its high cost.
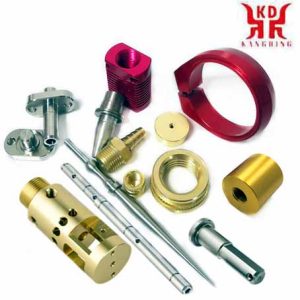
Pièces en laiton traitées par tour CNC
Pièces en laiton traitées par tour CNC
Chip formation
The lathe has evolved so much that it is no longer just a matter of removing material at high speed, but the parameters that make up the process have to be closely controlled to ensure the final results of economy, quality and precision.
The way to treat the chip becomes a complex process, where all the technological components of machining intervene, so that it can have the size and shape that does not disturb the work process. Failure to do so would rapidly build up masses of long, stringy chips in the machining area, forming tangled and uncontrollable skeins.
The shape that the chip takes is mainly due to the material being cut and can be ductile as well as brittle and brittle.
The advance with which one works and the depth of the pass are quite responsible for the shape of the chip, and when it cannot be controlled with these variables, it is necessary to resort to choosing the tool that incorporates an effective chip breaker. 16 greater efficiency than a normal lathe is faster
Dry and coolant machining
Today dry turning is completely viable and is used in many applications. There is a recent trend to carry out dry machining whenever the quality of the tool allows it. A higher cut-off temperature zone can be a positive factor in many cases.
However dry machining is not suitable for all applications, especially for drilling, tapping and boring to ensure chip evacuation.
Operations, matériaux, les pièces, quality requirements, and machinery need to be carefully evaluated to identify the benefits of removing the refrigerant supply.
Technological fundamentals of turning
In turning there are six key parameters:
Due to their operating mechanisms, CNC lathes allow machining conditions to be adjusted to the maximum and therefore achieve the best possible turning time.
Cutting speed (Vc). It is defined as the linear speed in the periphery of the area that is being machined. Your choice is determined by the material of the tool, the type of material of the part and the characteristics of the machine. A high cutting speed allows machining in less time but accelerates tool wear. The cutting speed is expressed in meters / minute.
Part rotation speed (N). Usually expressed in revolutions per minute. It is calculated from the cutting speed and the largest diameter of the pass being machined.
Advance (F). Defined as the penetration speed of the tool in the material. In turning it is usually expressed in mm / rev. Cependant, in order to calculate the turning time, it is necessary to calculate the feedrate in mm / min for each pass.
Depth of pass. It is the radial distance that a tool covers in its working phase. It depends on the characteristics of the piece and the power of the lathe.
Machine power. It is expressed in kW, and it is what limits the general machining conditions, when it is not limited by other factors.
Turning time (T). It is the time it takes for all the tools to perform the machining without taking into account other issues such as possible control stops or the time to put and remove the part from the head, which can vary depending on each part and machine. It is calculated based on adding the partial times of each tool.