En un clin d'œil, J'utilise des tours CNC depuis plus de dix ans, et avoir accumulé des compétences en usinage et une expérience des tours CNC. Y compris le tournage de différents matériaux (acier inoxydable, aluminium, acier au carbone cuivre, titane, carbure cémenté, etc.). En raison du remplacement fréquent des pièces traitées et des conditions d'usine limitées, depuis dix ans nous nous programmons, paramétrer nous-mêmes les outils, débogage et finition des pièces en traitement nous-mêmes. En résumé, les compétences opérationnelles sont divisées en les points suivants.
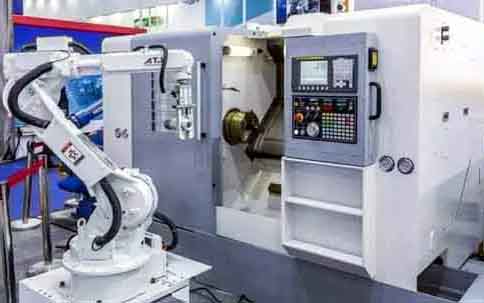
Tour CNC en fonctionnement
Un, Compétences en programmation du tour
Parce que notre usine a des exigences élevées en matière de précision des produits transformés, les éléments à prendre en compte lors de la programmation:
1. Séquence de traitement des pièces:
Percez d’abord, puis tournez l'extrémité plate (c'est pour éviter le retrait pendant le perçage);
Tournage grossier d'abord, puis bon tournage (c'est pour garantir l'exactitude des pièces);
La position avec une grande tolérance est traitée en premier, et le traitement final avec une petite tolérance (ceci permet de garantir que la surface de petite taille de tolérance n'est pas rayée et d'éviter la déformation des pièces).
2. Choisissez une vitesse raisonnable, avance et profondeur de coupe en fonction de la dureté du matériau:
1) Sélectionnez un matériau en acier au carbone à grande vitesse, avance élevée et grande profondeur de coupe. Tel que: 1Gr11, sélectionnez S1600, F0.2, et profondeur de coupe 2 mm;
2) Faible vitesse, une faible vitesse d'avance et une faible profondeur de coupe sont sélectionnées pour les alliages durs. Tel que: GH4033, sélectionnez S800, F0.08, et profondeur de coupe 0,5 mm;
3) Choisissez une vitesse faible, avance élevée et faible profondeur de coupe pour l'alliage de titane. Tel que: Ti6, sélectionnez S400, F0.2, and cut depth 0.3mm.
Take the processing of a certain part as an example: the material is K414, which is a very hard material. After many tests, the final selection is S360, F0.1, and the depth of cut 0.2, in order to process qualified parts.
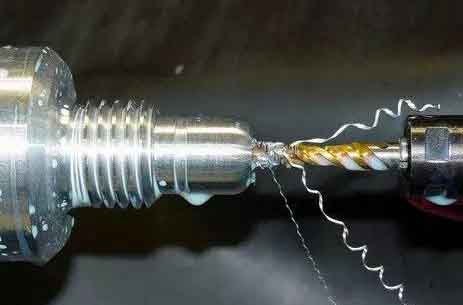
Processus de perçage au tour CNC
two, Tool setting skills of lathe
Tool setting is divided into: tool setting with tool setting instrument and direct tool setting. The tool setting technique mentioned below is direct tool setting.
First select the center of the right end face of the part as the tool setting point and set it as the zero point. After the machine tool returns to the origin, each tool that needs to be used is set with the center of the right end face of the part as the zero point;
When the tool touches the right end face, enter Z0 and click to measure, and the measured value will be automatically recorded in the tool compensation value, which means that the Z-axis tool is set. X tool setting is a trial cutting tool setting, and the outer circle of the part is turned with a tool. Measure the value of the turned outer circle (Par exemple, x is 20mm) and enter x20, click Measure, the tool compensation value will automatically record the measured value, and then the x axis will also complete the tool setting;
This tool setting method will not change the tool setting value even after the machine is powered off. It is suitable for mass production of the same part for a long time, during which the lathe does not need to recalibrate the tool after restarting.
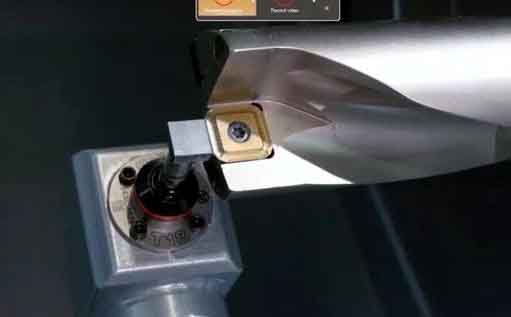
Common tool setting instruments for CNC lathes
three, Debugging skills of lathe
After the parts are programmed, test cutting and debugging are required after the tool is adjusted. In order to prevent errors and tool setting errors in the program from causing collision accidents, we should first perform idle stroke simulation processing. In the coordinate system of the machine tool, move the tool to the right by 2-3 times the total length of the part; Then start simulation processing. After the simulation processing is completed, confirm that the program and tool setting are correct, and then start processing the parts. After the completion of the first pieces of machining parts, the first self-test, to confirm eligibility, check to find full-time inspectors, qualified full-time inspectors confirmed this indicates the end of commissioning.
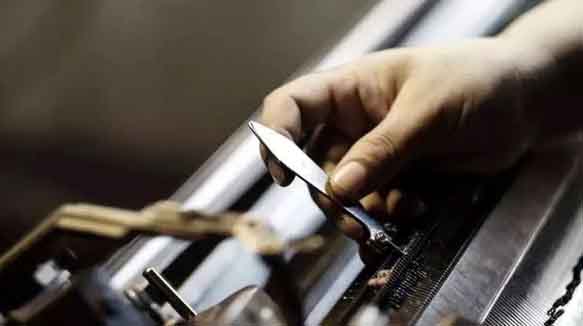
Trial cutting and debugging of CNC lathe
four, Finition de l'usinage des pièces
Une fois le montage d'essai du premier prototype terminé, les pièces seront produites en série. Cependant, le produit qualifié du prototype ne signifie pas que l'ensemble du lot de pièces sera qualifié, parce que dans le processus de traitement, l'outil s'usera en raison de la différence dans les matériaux de traitement. Lorsque le matériau de traitement est mou, l'usure de l'outil est faible, et le matériau de traitement est dur et l'outil s'use rapidement. Donc, en cours de traitement, il faut vérifier davantage, augmenter et diminuer la valeur de compensation de l'outil dans le temps pour garantir les pièces qualifiées.
Prendre une part à titre d'exemple, le matériau de traitement est K414, et la longueur totale de traitement est de 180 mm. En raison du matériau extrêmement dur, l'outil s'use très rapidement pendant le traitement. From the start point to the end point, an angle of 10-20mm will be generated due to tool wear. Donc, we must artificially add a compensation value of 10-20mm in the program, so as to ensure the qualified parts.
The basic principles of lathe processing: Rough machining first, remove excess material from the workpiece, and then finish machining; Avoid vibration during processing; Avoid the thermal denaturation of the workpiece during processing. There are many reasons for the vibration caused by the excessive load; It may be the resonance of the machine tool and the workpiece, or the rigidity of the machine tool may be insufficient, or it may be caused by the passivation of the tool. We can reduce vibration by the following methods; Reduce the transverse feed and processing depth, vérifier si la pièce à usiner est bien serrée, augmenter la vitesse de l'outil et réduire la vitesse pour réduire la résonance. En outre, vérifier s'il est nécessaire de remplacer un nouvel outil.
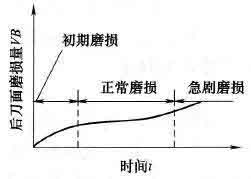
Processus d'usure des outils de tournage et norme émoussée
Cinq, L'expérience de la prévention des collisions de machines
La collision de la machine-outil nuit gravement à la précision de la machine-outil, et cela a des effets différents sur différents types de machines-outils. En général, il a un plus grand impact sur les machines-outils à faible rigidité. Donc, pour tours CNC de haute précision, les collisions doivent être absolument éliminées. A condition que l'opérateur soit prudent et maîtrise certaines méthodes anti-collision, les collisions peuvent être évitées et évitées.
La principale raison de la collision:
1> Entrez le diamètre et la longueur de l'outil de manière incorrecte;
2> La taille de la pièce et les autres dimensions géométriques associées sont saisies de manière incorrecte, et la position initiale de la pièce est mal positionnée;
3> Le système de coordonnées pièce de la machine-outil est mal réglé, ou le point zéro de la machine-outil est réinitialisé pendant le processus d'usinage, ce qui provoque un changement. La plupart des collisions de machines-outils se produisent lors du mouvement rapide de la machine-outil.. Les collisions qui se produisent à cette époque sont également les plus dangereuses et doivent être absolument évitées.. Donc, l'opérateur doit accorder une attention particulière à la machine-outil dans la phase initiale de l'exécution du programme et lorsque la machine-outil change d'outils. En ce moment, une fois que le programme est mal édité et que le diamètre et la longueur de l'outil sont mal saisis, des collisions sont susceptibles de se produire. A la fin du programme, si l'axe CN retire l'outil dans un mauvais ordre, alors des collisions peuvent également se produire.
Afin d'éviter la collision mentionnée ci-dessus, l'opérateur doit faire jouer pleinement les fonctions sensorielles lors de l'utilisation de la machine-outil. Observer s'il y a un mouvement anormal de la machine-outil, s'il y a une étincelle, s'il y a du bruit et du bruit anormal, s'il y a des vibrations, s'il y a une odeur de brûlé. Le programme doit être arrêté immédiatement lorsqu'une situation anormale est détectée, et la machine-outil peut continuer à fonctionner une fois le problème du lit de veille résolu.