La technologie de traitement du tour CNC est similaire à celle du tour ordinaire. Cependant, parce que le tour CNC est un serrage unique, traitement continu et automatique pour compléter tous les processus de tournage. Donc, les aspects suivants doivent être pris en compte:
1. Choix raisonnable de la quantité de coupe
Whether the selection of cutting parameters (ap, f, v) is reasonable, plays a very important role in whether the machine tool can fully utilize the potential of the machine tool and the cutting performance of the tool to achieve high quality, high yield, low cost and safe operation.
When rough turning, first consider choosing a turning depth ap as large as possible, then choosing a larger feed amount f, and finally determining an appropriate cutting speed v. Increasing the turning depth ap can reduce the number of passes, and increasing the feed f is beneficial to chip breaking. Donc, it is beneficial to select the rough turning amount according to the above principles to improve production efficiency, reduce tool consumption, and reduce processing costs.
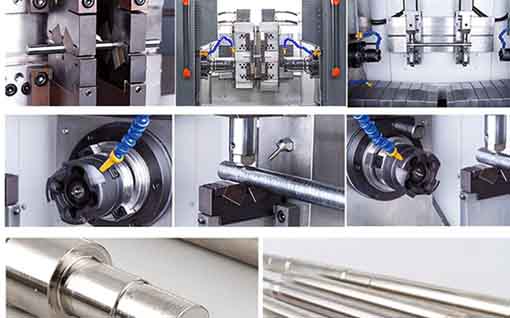
Conception de serrage du tour CNC
In fine turning, the machining accuracy and surface roughness are required to be high, and the machining allowance is not large and more uniform. Donc, when choosing the amount of cutting for finishing, it is important to consider how to ensure the quality of the machining, and on this basis, maximize the productivity. Donc, a smaller (but not too small) turning thickness ap and feed f should be used for fine turning. And choose high cutting performance tool materials and reasonable geometric parameters to increase the cutting speed v as much as possible.
2. Choose a tool reasonably
1) When rough turning, choose a tool with high strength and good durability to meet the requirements of large turning depth and large feed when rough turning;
2) En finissant de tourner, choose tools with high precision and good durability to ensure the requirements of machining accuracy.
3) In order to reduce the time of tool change and facilitate tool setting, machine clamp blades should be used as much as possible.
3. Choose fixtures reasonably
1) Try to use general fixtures to clamp the workpiece, avoid using special fixtures;
2) The positioning datums of the parts coincide to reduce positioning errors.
4. Determine the processing track
The processing route is the movement track and direction of the tool relative to the part during the processing of the index-controlled machine tool:
1) It should be able to ensure the processing accuracy and surface roughness requirements;
2) The processing route should be shortened as much as possible to reduce the tool idle travel time.
5. The relationship between machining track and machining allowance
Maintenant, under the condition that the CNC lathe has not reached the popular use, the excess margin on the blank, especially the margin containing the forged and cast hard skin layer, should be arranged on the ordinary lathe for processing. If you must use a CNC lathe to process, you need to pay attention to the flexible design of the program.
6. Jig mounting points. Maintenant, the connection between the hydraulic chuck and the hydraulic clamping cylinder is realized by a tie rod. The main points of hydraulic chuck clamping are as follows:
First use a moving hand to remove the nut on the hydraulic cylinder, remove the pull tube, and pull it out from the rear of the spindle, and then use the moving hand to remove the chuck fixing screw to remove the chuck.