1. Manual programming of CNC machining
Manually complete all the work of programming (including computer-aided numerical calculation) for manual programming.
For parts with simple geometric shapes, the numerical calculation is simpler and there are not many program segments. Manual programming is easier to complete, economical and timely. Donc, manual programming is still widely used in point processing and contour processing composed of straight lines and arcs. But for parts with complex shapes, especially parts with non-circular curves, tabular curves or curved surfaces, manual programming is difficult. The possibility of errors increases, the efficiency is low, and sometimes even the program cannot be compiled. Donc, automatic programming must be used to compile the program.
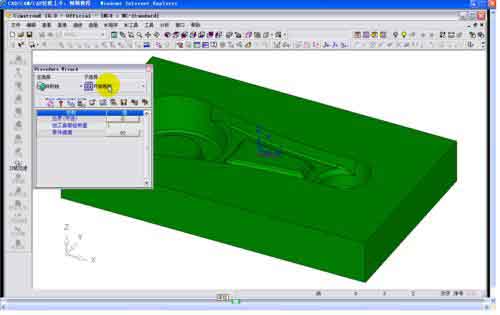
The process of NC programming
2. Automatic programming of CNC machining
The automatic programming of CNC machining is also called computer-aided programming, c'est, most or all of the programming is done by the computer. Such as completing the calculation of coordinate values, compiling part processing procedures, automatically outputting and printing processing procedures and preparing control media. The self-programming method reduces the labor intensity of the programmer, shortens the programming time, improves the programming quality, and at the same time solves the programming problems of many complex parts that cannot be solved by manual programming. The more complex the surface shape of the workpiece and the more complicated the process, the more obvious the advantages of automatic programming.
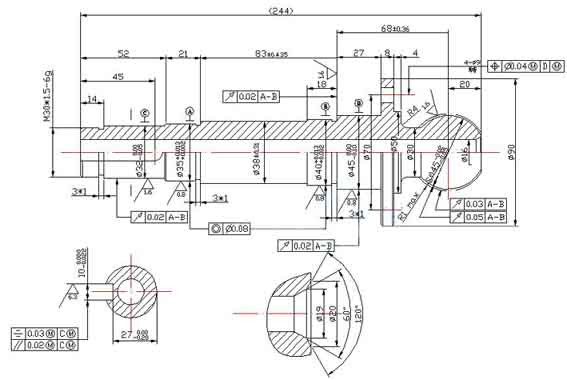
CNC automatic programming method
Steps of CNC programming
1. Determine the process
Analyze the part drawing, determine the processing plan, determine the processing sequence, design the fixture, select the tool, determine the tool path, quantité de coupe, etc.. Correctly select the tool setting point and cutting method.
2. Numerical calculation
According to the determined processing route and the allowable part processing error, the required data input to the numerical control device is calculated, which is called numerical calculation. The main content of numerical calculation is to calculate the coordinate value of the part contour and the tool motion path in the specified coordinate system.
Contour machining for parts with simple shapes (such as parts composed of straight lines and arcs). It is necessary to calculate the coordinate values of the start point, end point of the geometric element, the center of the arc, the intersection or tangent point of the two geometric elements. Contour processing for parts with complex shapes (such as parts composed of non-circular curves and curved surfaces). It needs to be approximated by a straight line segment or a circular arc segment, and the node coordinate value is calculated according to the required accuracy. In this case, computers are generally used to complete numerical calculations.
3. Write the program table for parts processing
Write the program according to the code and format specified by the CNC system used.
4. Programmable preparation control medium
In the past, perforated tape was used as the medium and fed into the numerical control system through a paper tape reader. Now you can directly use the keyboard to input, or program in the computer through the corresponding software and interface.
5. Program verification and trial cutting
The program must be checked, verified and cut before it can be used.
You can check whether the trajectory is correct through the dry run program, and you can also use the graphic simulation function.