KN95 Mask Machine Roller, Stamping Shaft and Press Wheel
1. The embossing roller cart of the mask machine is made of seamless steel pipe, and then processed by CNC. Processing is divided into turning, milling and welding.
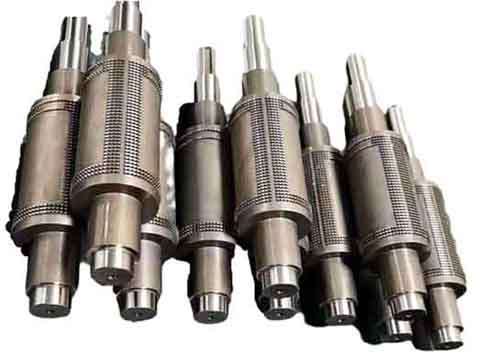
Mask machine embossing wheel
2. Turning and milling: turning and processing the joint surface of the mating parts of the roller body, end plate and shaft head. Rough and fine turning each part of the embossing shaft roller body to the size required by the drawing, then set the center frame, turn the end face, and drill.
3. Welding of the inner tube of the embossing roller: correct the coaxiality between the shaft at both ends and the inner sleeve, and only weld the inner end plate on the shaft head. Put the inner sleeve into the roller body, and weld the mating junction of the inner end plate and the roller body.
4. Install the outer end plate on the shaft at both ends, and weld the junction of the outer end plate and the joint surface with the roller body. The next step is annealing and drilling. The roll blank is annealed to eliminate internal stress; One end of the steel roller is flattened, and a standard center hole is drilled. Then there is the embossing pattern of the engraving roller. The embossing roller can be carved with patterns on the surface of the roller according to the pattern and pattern requirements of the customer. With high-tech laser machines and engraving equipment, the craftsmanship is exquisite and the lines are clearly visible.
5. Enfin, chrome plating and verification are required. The chrome plating needs to be determined according to the purpose, and the verification is mainly to ensure the balance and stability of the steel bars.
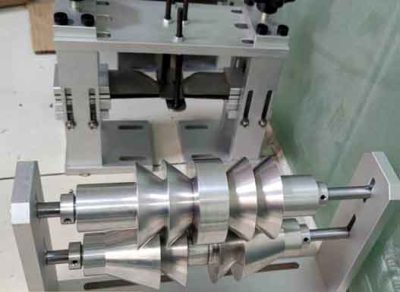
Mask machine folding wheel roller
Par rapport aux tours CNC ordinaires, the turret tool post of CNC turning center is equipped with power tools that can rotate milling cutters, drills, and taps. En même temps, the machine tool spindle also has the C-axis function that can be accurately indexed according to the CNC program and interpolated with the X-axis or (et) Z-axis. This kind of 3-axis (X, Z, C) control turning center can perform turning, fraisage, forage, ennuyeux, and tapping on the rollers of the mask machine in one clamping. So far, it is still the most used face mask machine roller workpiece composite machining machine tool in industrial production.
Cependant, no matter how the single-spindle turning center expands the process range, it still cannot solve the problem of the back side secondary processing (ie, the processing of the workpiece clamping end) of the mask machine roller under one clamping, so it must be completed with a dual-spindle turning center. The two spindles of the dual-spindle turning center are mostly arranged oppositely on the same axis, so that after the main end of the rotating body is processed, la deuxième broche récupère automatiquement la pièce à usiner de la broche pour traiter l'extrémité de serrage.
Étant donné que les tâches d'usinage de l'extrémité de serrage sont généralement relativement simples, la deuxième broche est généralement appelée sous-broche, et sa puissance est relativement faible. Le centre de tournage bibroche peut être équipé d'un poste outil, mais la plupart d'entre eux sont deux postes d'outils, in order to improve the processing efficiency and give full play to the potential of the machine tool equipment. The machine is on the same axis above the bed, equipped with a main shaft and a sub-spindle facing each other. En général, the speed of the dual main shafts is 0~4000r/min, et les deux peuvent être contrôlés par l'axe C. The sub-spindle can also move along the axial direction to pick up the workpiece that has been processed on the main shaft at one end. A turret tool holder with about ten tool positions is provided above the main spindle and below the sub-spindle. Each tool position on the turret tool post can be equipped with a power tool with a certain power and a speed of 80~8000r/min. Le poste d'outil supérieur est contrôlé par 3 axes (X1, Y1, Z1), The lower tool post is controlled by 2 axes (X2, Z2).
The Japanese Okuma TWINSTAR series turning-milling composite CNC machine tools provided by our company have two models: TWIN STAR LT200-M and TWIN STAR LT300-M. Has the following performance characteristics:
• Opposing dual-spindles, the main and sub-spindles have the same power and the same speed, and the upper and lower tool rests have the same power and the same capacity.
• It can do four-axis turning and milling at the same time. The main and sub-spindles can simultaneously transfer and clamp the workpiece without stopping. De cette façon, all the front and back processing from the blank to the finished product can be completed, which greatly shortens the processing cycle of the workpiece and shortens the processing time by about 40%.
• With milling function, the transmission power of the rotary tool spindle is 5.5kW.
• Double tool post, using left and right spindles and upper and lower composite tool posts for machining, which can integrate the machining processes that were previously divided into multiple processes. The use of high-precision linear guides can maintain stable machining accuracy even for long-term continuous machining.