Qu'est-ce que l'usinage de l'aluminium et quelles sont ses principales fonctions? Application des pièces en aluminium et analyse de la technologie d'usinage CNC.
Réaliser un procédé d'usinage de pièces en aluminium, il est nécessaire de connaître les caractéristiques physiques du matériau à usiner, qui sont importants lors de la sélection des outils, angles de coupe, vitesses, entre autres paramètres. Certains aspects importants de l’usinage de l’aluminium sont décrits ci-dessous.
Physical characteristics of aluminum
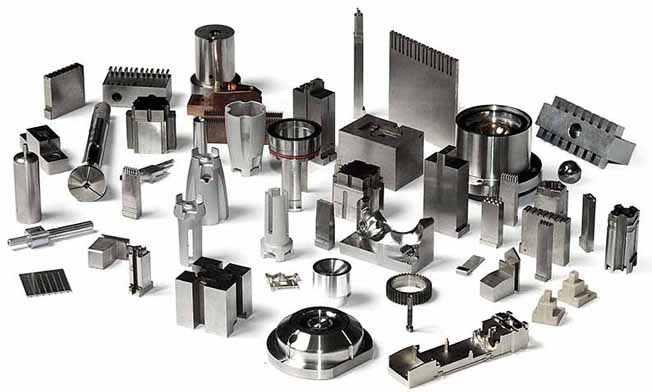
Pièces en aluminium
Aluminum is one of the most used metals due to its special physical characteristics:
– Excellent thermal conductivity, which can reach up to 230 W / m K., This characteristic allows it to perform very well in heat dissipation tasks, used for the manufacture of auto parts such as radiators for cars in the automotive industry, also in Component heat sinks in the mechanical, electrical and especially electronics industries.
– Highly resistant to corrosion in humid environments, except in the presence of hydrochloric acid or alkalis. When it is in the open air a layer of aluminum oxide is formed which prevents its corrosion process, this property allows aluminum an excellent performance in mechanical and architectural industries.
– It is a good electrical conductor, its electrical conductivity is approximately 35 m / Ω mm2, which makes it an excellent candidate for applications of generation, transport and use of electrical energy.
– It is also a low-density metal (2,700 kg / m3), it has low mechanical resistance but is easily improved by alloying processes, allowing it to reach up to 690 MPa. Its weight is close to a third of the weight of steel, these characteristics make it especially useful in the aerospace and automotive industry, since its lightness contributes to energy savings in transport.
– The hardness of aluminum ranges from HB = 15 for very pure soft aluminum to approximately HB = 110 for 7075 alloyed (AlZnMgCu) and thermally hardened aluminum.
– The ductility or elastic limit of aluminum is approximately 0.2%, it is highly deformable, a very useful property in the production of electrical conductors, mechanical systems to absorb impact energy, among others.
– The excellent malleability of aluminum makes it useful in the production of thin sheets used as aluminum foil, tin cans for the food industry.
– Its melting point is rather low, around 660ºC, therefore it requires little energy to manufacture parts through injection processes and metal extrusion.
Because it is very abundant in nature and its easy recovery in the recycling process, it is an inexpensive metal.
Thanks to its characteristics, aluminum has become a metal highly used in the industry to produce parts through the use of different production and manufacturing processes such as injection, extrusion and machining.
To machine aluminum, relatively little energy is required, since to achieve the cut of the material thanks to its mechanical characteristics, it uses a third of the energy compared to the energy used in the machining of steel. Machining of aluminum can be achieved with high speeds and starting cups without generating excessive stresses between the material and the cutting tool. High machining speed means higher productivity and better surface finishes.
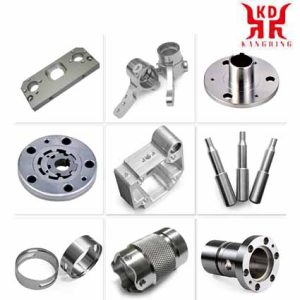
Machining of aluminum parts
Cutting tools for machining aluminum
Machining aluminum requires that the tool have certain special characteristics. It is desirable that the cutting tools used for this type of materials allow the efficient evacuation of the material to avoid blunting that can ruin the part and the cutting tool, likewise, the rake angles should be greater than those used to machine steels.
Thanks to the high thermal conductivity of aluminum, the cooling process of the cutting tool does not require too much cooling liquid flow, just enough to evacuate detached material.
In the market there are a variety of cutting tools with different properties and costs. For the machining processes of aluminum, like steel, it is desirable that the tools are very efficient and durable over time. Thanks to technological advances, it is possible to find tools with hard coatings such as DLC (diamond like carbon). that provide hardness and tribological properties to the tool, up to complex coating processes such as PVD (vapor deposition) treatments, with which titanium nitride coatings capable of protecting the tool with surface layers with titanium are achieved. Some materials for cutting tools for aluminum are:
High-speed steels are special high-performance steels with high hardness up to 500 ºC and high resistance to wear thanks to alloying elements such as tungsten, molybdenum, vanadium and chromium, capable of forming carbides. Cobalt is added to increase hardness. HSS tools are suitable for machining low-silicon aluminum alloys. Supports the use of large rake angles for better cutting conditions.
Carbide is a mixture of tungsten carbide and cobalt (CW + Co). This coating provides longer tool life. They are used in the machining of aluminum with high silicon content and for machining at high cutting speeds.
Diamond, polycrystalline diamond (PCD) is obtained by sintering fine powders of granulated diamond crystals at high temperatures and pressures into the desired shape. Diamond tools are characterized by their long life, even when used in the machining of alloys with a high silicon content. They are normally used for finishing work on aluminum alloys that generate long chips, or for automatic machines working with aluminum that generate short chips.
In conclusion, it can be said that thanks to the physical and mechanical properties of aluminum, it is one of the metals most used by humanity in numerous fields of industry, therefore it is one of the metals that are most mechanized in production processes. Aluminum machining processes require much less energy than that used in steel machining, it is carried out at high cutting and feed speeds, providing quality surface finishes.
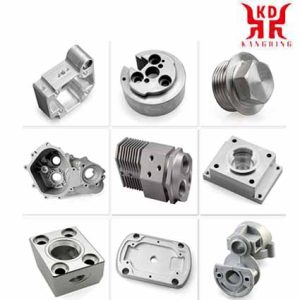
Die-cast aluminum parts
Mechanical properties
Aluminum is a relatively soft and tough metal. The tensile strength of absolutely pure aluminum is 45 N / mm², the yield point is 17 N / mm² and the elongation at break is 60%. while the tensile strength of commercially pure aluminum is 90 N / mm², the yield point is 34 N / mm² and the elongation at break is 45%. The tensile strength of its alloys, on the other hand, is up to 710 N / mm² (alliage 7068). Its modulus of elasticity is around 70 GPa, a value that is often quoted. A value of 66.6 GPa is given for pure aluminum, but the values vary from 60 à 78 GPa. The G-module is 25.0 kN / mm², the Poisson’s ratio is 0.35.
Thermal properties
The melting temperature is 660.2 ° C and the boiling temperature is 2470 ° C. The melting temperature is significantly lower than that of copper (1084.6 ° C), fonte (1147 ° C) and iron (1538 ° C), which makes aluminum a good cast material.
At a transition temperature of 1.2 K, pure aluminum becomes superconducting.
The thermal conductivity is relatively high at 235 W / (K m). The thermal conductivity of copper is about twice as high, but its density is about four times greater, which is why aluminum is used for heat exchangers in vehicles. The coefficient of thermal expansion is quite high due to the very low melting point of 23.1 µm • m − 1 • K − 1.
The shrinkage, c'est à dire. the decrease in volume when solidifying, is 7.1%.
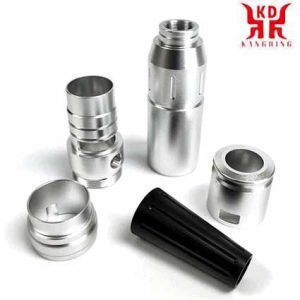
Turning aluminum and aluminum alloy parts
Aluminum alloys
Aluminum alloys are alloys that mainly consist of aluminum.
Aluminum can be alloyed with numerous metals to promote certain properties or to suppress other undesirable properties. With some alloys, the formation of the protective oxide layer (passivation) is severely disturbed, which means that the components made from them are sometimes at risk of corrosion. Almost all high strength aluminum alloys are affected by the problem.
There are wrought aluminum alloys that are intended for further processing by rolling, forging and extrusion, and cast materials. These are used in foundries.
En général, aluminum alloys are divided into two large groups of wrought and cast alloys:
Cast aluminum alloys. Typical cast aluminum alloys contain silicon as the main alloying element (AlSi), but there are also types with copper or magnesium as cast alloys. [48] [63]
Wrought aluminum alloys, they have a share of about 75% and are further subdivided according to the main alloy element (s) into
Pure aluminum with an aluminum content of 99.0% à 99.9%. They are very easy to work with, have low strength and good corrosion resistance.
Aluminum-copper alloys (AlCu): They have medium to high strength, can be hardened, but are susceptible to corrosion and difficult to weld. They can contain magnesium or manganese additives.
Aluminum-manganese alloys (AlMn): They have low to medium strength, are corrosion-resistant and easy to process.
Aluminum-magnesium alloys (AlMg, without AlMgSi): They have medium strengths, cannot be hardened, are corrosion-resistant, easy to form and weld. Most types also contain manganese (AlMg (Mn)).
Aluminum-magnesium-silicon alloys (AlMgSi): They have medium to high strengths, are easy to process by welding and extrusion, can be hardened and are corrosion-resistant.
Aluminum-zinc-magnesium alloys (AlZnMg): Copper-free types have medium to high strengths and are easy to weld. Grades containing copper (AlZnMg (Cu)) have high strengths – in the case of 7075 over 500 MPa – cannot be processed by fusion welding, but can be machined (fraisage, forage).
Special alloys, for example aluminum-lithium alloys with a particularly low density, or free-cutting alloys that are particularly easy to machine.
A distinction is also made between naturally hard alloys – which cannot be hardened by heat treatment – and hardenable alloys:
Typical naturally hard wrought aluminum alloys are: AlMg, AlMn, AlMgMn, AlSi
Hardenable wrought alloys – increase in strength through precipitation hardening of alloy elements with additional aging annealing at 150 à 190 ° C. Typical hardenable wrought aluminum alloys are: AlMgSi, AlCuMg, AlZnMg. The first high-strength, hardenable aluminum alloy AlCuMg was given the trade name Duraluminium, or “Dural” for short, dans 1907.
Economical meaning
After steel, aluminum is the second most important metallic material. In 2016, 115 million tons were produced worldwide.
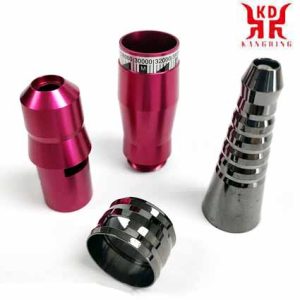
Finition de surface des pièces en aluminium
Machinability of aluminum and aluminum alloys
Turning aluminum
Machining includes turning, drilling and milling. Aluminum materials are easy to machine. Cependant, their exact properties depend on the alloy and the state of the structure. It should be noted that the temperatures occurring during processing can quickly be in the range of the melting point. With the same cutting parameters as with steel, cependant, aluminum results in lower mechanical and thermal stress. Tungsten carbide is often used as a cutting material for hypoeutectic alloys or diamond for hypereutectic alloys that wear heavily. The machining of anodized workpieces in particular requires hard tools in order to avoid wear and tear from the hard anodized layer. The grinding dust generated when grinding aluminum can lead to an increased risk of explosion.
Aluminum and aluminum alloys are considered to be easy to machine. It is an important construction material, especially in the aerospace industry and in vehicle construction, which is well suited for lightweight construction. Up to 90% of the raw parts are machined. Cependant, low-strength grades can form long chips and tend to stick to the cutting edge. The cutting forces are generally low, the wear depends on the structure. Aluminum and its alloys are well suited for high-speed machining. The temperatures that occur are only around 300 ° C, which is very low compared to temperatures that occur with steel, but relatively high compared to the melting point of aluminum alloys (580 ° C to 660 ° C). The cutting speed can vary within wide limits; downwards it is limited by the built-up edge formation and upwards by the melting temperature. Despite the low cutting forces, drives are required due to the high cutting speeds, which have to provide about five times the power than is necessary for machining steel. High-speed steels are used as cutting materials for simple machining such as drilling. Often the hard metal types are based on tungsten carbide. D'autre part, grades with titanium or tantalum are not suitable, as these elements enter into chemical reactions with aluminum. Coatings are therefore not suitable either. The cutting ceramics are also not chemically resistant and wear out very quickly. Diamond, on the other hand, is well suited for machining aluminum and is used because of its very long service life and high surface quality. This is particularly advantageous when machining mirrors. The wear is usually low, but some alloys contain hard, abrasive additives that increase wear but improve chip breaking. The wear almost always occurs on the open space; Crater wear only occurs with highly abrasive structural components at high cutting speeds.
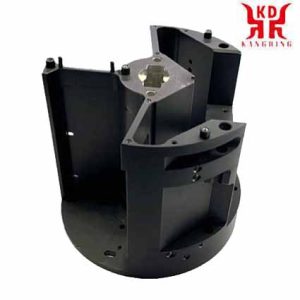
Precision aluminum parts
The exact conditions depend heavily on the alloy.
Soft materials such as the non-hardenable wrought alloys and the hardenable in the soft state tend to produce long chips and the formation of built-up edges. The surface quality is rather poor, at high cutting speeds it can be improved. If possible, such materials are machined after cold forming, as the work hardening leads to more favorable chip shapes and surfaces.
Stronger materials such as hardened wrought alloys are usually easier to machine
Cast alloys often contain silicon which has an abrasive effect. The higher the silicon content, the higher the tool wear. The chip shapes are good.
Since aluminum tends to stick, it is often machined with a large rake angle.