En usinage CNC, l'usinage sur grand tour fait partie de l'usinage CMC. Cette pièce est très appréciée des clients, and even many regions rely on this technology to achieve rapid economic development. What are the advantages of large-scale lathe processing, which can attract so many people to engage in this industry?
The primary reason why people favor the technology of large lathe processing is that it is easy to ensure the accuracy of each processing surface of the workpiece. This is equivalent to guaranteeing the quality of the work piece and having a better degree of coordination in the application. During processing, the workpiece rotates around a fixed axis, and each surface has the same axis of rotation, so the coaxiality requirements between the processing surfaces can be guaranteed. During the cutting process, the lathe processing is relatively stable. Dans des circonstances normales, the process of lathe processing is continuous, and there will be no impact, so it is stable.
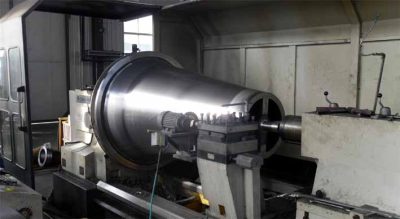
CNC turning of large lathe
Analysis of Process Difficulties of Slender Hole Processed by Large Lathe
Large lathe machining is a relatively common technology, but this technology is not suitable for all workpieces. Parmi eux, the use of this technology to process slender holes is a difficult problem in workpiece processing. The manufacturer will analyze the main difficulties for you in detail.
The precise positioning of the workpiece is the first problem encountered when using large lathe processing technology to process slender holes. The reason for this problem is that the rigidity of the drilling tool, the size of the machining axial force, and the clamping and positioning of the workpiece will affect its machining accuracy. Considering these contents, special fixtures should be designed according to the size requirements of the workpiece in combination with specific processing equipment and process methods during construction. Long-stem cutting drills suitable for ordinary lathes are also one of the problems, because it is difficult to find suitable ultra-deep hole drilling tools in the market, so it is necessary to design suitable long-stem drilling tools according to the size requirements of the workpiece.
During the turning process, cooling and chip removal problems are also encountered. During processing, ensuring effective cooling of the cutting part and continuous discharge of chips is the key to the processing process. The conventional cooling method cannot be directly injected into the cutting area, and the cooling and chip removal effect is not guaranteed, so this problem should be considered when designing long-stem drilling tools.
The last problem is the cutting process parameters. The rotation speed of the workpiece, the feed rate of the tool, and the flow pressure of the cutting fluid are based on the effect of chip removal, and it is necessary to consider the tool retraction and chip removal. Both are important process parameters that need to be carefully considered and studied.
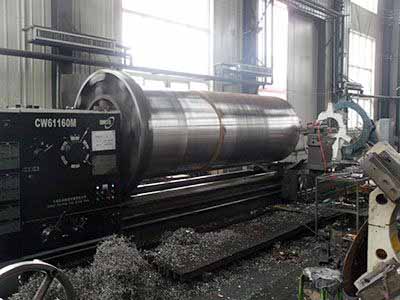
Technologie de tournage de pièces d'arbre
Common CNC machining methods of conical surface
To process the conical surface, it is necessary to ensure the dimensional accuracy and the cone angle, and there are many commonly used processing methods. Large lathe processing manufacturers today introduce you to several more commonly used methods.
Method 1: Turning cone by rotating the small slide method. The operation of this method is relatively simple, but the cone angle is generally only accurate to half a degree. Because of the limitation of the stroke of the small slide plate, the processing of too long tapered surface cannot be realized. In actual operation, the worker tries to cut the conical surface of the part. Before the size does not meet the requirements, repeatedly use a cone plug gauge or ring gauge and other measuring tools to test the cone surface. This method is time consuming and the accuracy is not very high.
Method 2: Turning cone by offset tailstock method. This method can realize automatic feeding and is suitable for processing long conical surfaces. Cependant, the workpiece is limited by the top support, and the workpiece with a large taper angle cannot be machined, and the machining accuracy is not very high.