Ruostumattoman teräksen jyrsinnän ominaisuudet ovat: ruostumattomalla teräksellä on vahva tarttuvuus ja fuusio, ja lastut tarttuvat helposti jyrsimen hampaisiin, mikä pahentaa jauhatusolosuhteita;
Ylösjyrsinnässä, leikkurin hampaat liukuvat ensin kovetetulla pinnalla, mikä lisää taipumusta työskennellä; Jyrsinnässä, isku ja tärinä ovat suuria, jonka ansiosta jyrsimen terän hampaat on helppo hakea ja kulua.
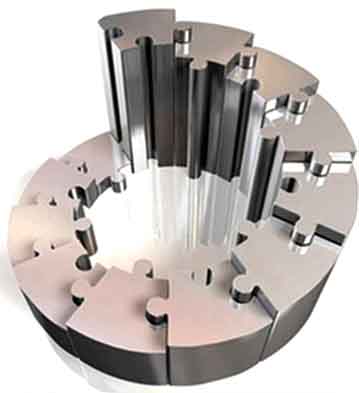
Ruostumattoman teräksen tarkkuusosien NC-jyrsintä
For milling stainless steel, in addition to end mills and some end mills, cemented carbide can be used as milling cutter tooth materials. Other types of milling cutters are made of high-speed steel, especially tungsten-molybdenum series and high-vanadium high-speed steel with good results. The tool durability can be 1-2 times higher than W18Cr4V. Cemented carbide grades suitable for making stainless steel milling cutters are YG8, YW2, 813, 798, YS2T, YS30, YS25, jne.
When milling stainless steel, the milling edge must be sharp and able to withstand impact, and the chip pocket must be large. Large helix angle milling cutters (cylindrical milling cutters, end milling cutters) can be used, the helix angle b is increased from 20° to 45° (gn=5°), and the tool durability can be increased by more than 2 ajat. Because the working rake angle g0e of the milling cutter is increased from 11° to more than 27° at this time, the milling is brisk. But the value of b should not be too large, especially for end mills with b≤35°, so as not to weaken the teeth.
Using wave-edge end mills to process stainless steel pipes or thin-walled parts, cutting is brisk, vibration is small, chips are fragile, and the workpiece is not deformed. High-speed milling with cemented carbide end mills and stainless steel with indexable end mills can achieve good results.
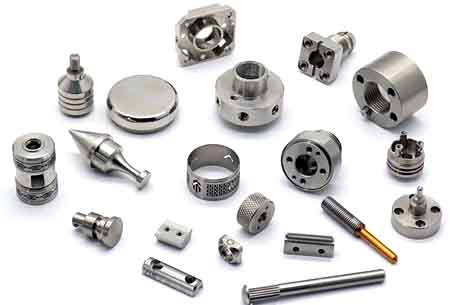
Quick quotation for machined parts
Milling 1Cr18Ni9Ti with silver chip end mill (SWC), its geometric parameters are gf=5°, gp=15°, af=15°, ap=5°, kr=55°, k′r=35°, g01= -30°, bg=0.4mm, re=6mm. When Vc=50-90m/min, Vf=630-750mm/min, a′p=2-6mm, and the feed per tooth reaches 0.4-0.8mm, the milling force is reduced by 10%-15%, and the milling power A reduction of 44%, efficiency has also been greatly improved. The principle is to grind a negative chamfer on the main cutting edge, and artificially generate a built-up edge during milling, so that it can replace the cutting edge for cutting, and the rake angle gb of the built-up edge can reach 20~-302. Due to the effect of the entering angle, the built-up edge is subjected to a thrust parallel to the cutting edge generated on a rake face and becomes a secondary chip flowing out, thereby taking away the cutting heat and reducing the cutting temperature.
When milling stainless steel, down milling should be used as much as possible. The asymmetric down milling method can ensure that the cutting edge is smoothly cut away from the metal, and the chip bonding contact area is small, and it is easy to be thrown off under the action of high-speed centrifugal force. In order to prevent the cutting chips from impacting the rake face when the cutter teeth re-cut into the workpiece, spalling and chipping will occur, and the durability of the cutter can be improved.
The spray cooling method is the most effective, which can increase the durability of the milling cutter by more than double; If a general 10% emulsion is used for cooling, the cutting fluid flow rate should be ensured to achieve sufficient cooling. When the carbide milling cutter mills stainless steel, take Vc=70-150m/min and Vf=37.5-150mm/min. Samaan aikaan, make appropriate adjustments according to the alloy grades and workpiece materials. The cutting amount of high-speed steel milling cutter is shown in Table 1
Jyrsintyyppi | Milling cutter diameter d0 (mm) |
Spindle speed n (rpm) |
Feed amount f (mm/min) |
Remarks |
End mill | 3-4 | 1180-750 | Manual | When the cutting width and cutting depth are small, the feed amount f takes a large value; Päinvastoin, when milling 2Cr13 and other martensitic stainless steel with a small value, the milling amount should be adjusted according to the actual hardness of the workpiece material When milling concentrated nitric acid resistant stainless steel, the milling speed and feed rate should be appropriately reduced |
5-6 | 750-475 | |||
8-10 | 600-375 | |||
12-14 | 375-235 | 30-37.5 | ||
16-18 | 300-235 | 37.5-47.5 | ||
20-25 | 235-190 | 47.5-60 | ||
32-36 | 190-150 | 47.5-60 | ||
40-50 | 150-118 | 47.5-75 | ||
Wave edge end mill | 36 | 190-150 | 47.5-60 | |
40 | 150-118 | |||
50 | 118-95 | |||
60 | 95-75 | 60-75 | ||
Saw blade milling cutter and face milling cutter | 75 | 235-150 | 23.5 or Manual | |
110 | 150-75 | |||
150 | 95-60 | |||
200 | 75-37.5 |
Taulukko 1, Milling amount of stainless steel processed by high-speed steel milling cutter