The 5-axis machine tool with trunnion and planetary structure usually adds a two-axis rotary table on the basis of the standard three-axis machine tool. The advantage of this structure is that the parts are fixed on the centerline of rotation. According to different sizes, the linear coordinate compensation stroke is the shortest when the rotary axis changes its angle during the linkage processing. In this kind of operation and at the end of each machining cycle, the feed is all restricted by the running state of any one of the 5 coordinate axes. Yleensä, it is restricted by the linear axis due to the excessive compensation stroke. Due to its large weight and offset effects, it cannot effectively increase the acceleration of the linear coordinate. Verrattuna, due to the direct drive technology, the rotary coordinate can easily achieve high dynamic performance. Combining this with a short stroke will help shorten the machining cycle time and improve machining accuracy.
The short compensation stroke is usually not related to the 5-axis positioning. Only when high-speed machining requires linear coordinates and rotary coordinates to reach the target position almost at the same time will there be a problem. As 5-axis machining parts are becoming more and more complex and require more types of tools, a lot of tool change time will be generated during the machining cycle.
Toisaalta, due to the fact that the casting of the processed part is very close to the actual shape, and the application of high-performance cutting technology, the cutting time is shortening. As shown in the figure, when processing aluminum car steering knuckles, using an innovative 5-axis machining concept, the chip cutting time is only 1.9s. Since all the tools only need to be changed once when processing two parts on the left and right sides, the tool change time is reduced by 50%.
Adopting more efficient loading and unloading technology. The standardized robot unit cooperates with the overall raw material and finished product storage device, effectively reducing non-production time. In addition to loading and unloading materials for the two machine tools, the robot can also perform tasks such as cleaning, marking, and measurement. Due to the planetary table that can be equipped with jointless fixtures, the adjustment time between different processing applications is very short. With high-speed direct drive, two worktables can be mirrored. This is of great significance for the processing of symmetrical parts, such as the processing of symmetrical parts on the left and right sides of a car, truck or airplane.
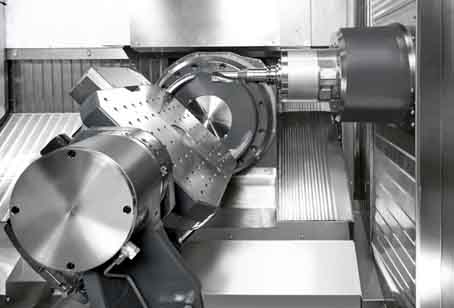
5-akselin työstö planeettarakenteella