Monimutkaiset ääriviivat näkyvät työkalujen ja muottien valmistuksessa, ja ovat massatuotettuja tuotteita. Ennen CNC-työstökoneiden syntymistä, taonta- ja autoteollisuudessa käytettävät meistit valmistettiin pääasiassa käsin. 1970-luvun jälkeen, CNC-työstökoneita on käytetty laajalti työkalujen ja muottien valmistuksessa. Monimutkaisten profiilien perusääriviivat käsitellään yleensä jyrsimällä, ja ympäröivät CNC-työstökoneet on alun perin asetettu kolmiakseliselle vivustolle.
1980-luvulle siirtymisen jälkeen, viisiakselisia jyrsimiä on käytetty laajasti monimutkaisessa pintakäsittelyssä. Työkappaleen ääriviiva jyrsinnän jälkeen on hyvin lähellä työkappaleen lopullista muotoa, mutta viimeinen viimeistelyprosessi on edelleen manuaalinen. 1980-luvun lopulla, nopea leikkaustekniikka kehittyi ja kypsyi vähitellen, ja sen käyttöä teollisessa tuotannossa on jatkuvasti parannettu työstökoneiden osalta, leikkuutyökalut ja muut niihin liittyvät tekniikat. Koska nopea leikkaus voi kaksinkertaistaa syöttönopeuden, syöttöväliä voidaan pienentää tuotannon tehokkuutta heikentämättä. Tämä on edellytys työkappaleen muototarkkuuden parantamiselle ja pinnan karheuden vähentämiselle. Nykyisessä, suurin osa nopealla jyrsinnällä käsitellyistä työkappaleista ei enää tarvitse viimeistä manuaalista käsittelyä, mutta voidaan ottaa suoraan käyttöön.
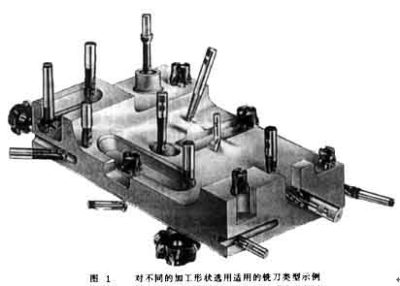
5-monimutkaisten profiilien akselikoneistus
Uudet työkalumateriaalit: kuten alumiinioksidipohjainen keramiikka, piinitridipohjainen keramiikka, kermetit, sementoitu kovametalli, erityisesti superkovien pinnoitteiden jatkuva kehittäminen, mahdollistaa kovan pintajyrsinnän. Muotin pinta voidaan jyrsiä muotoon karkaisun jälkeen, Näin vältetään jyrsinnän jälkeisen karkaisun aiheuttamat muodonmuutokset. Tämä ei ainoastaan yksinkertaista koneistusprosessia, mutta myös parantaa työkappaleen tarkkuutta.
Lisäksi, käyttämällä tarkkuustaontaa muottien valmistuksessa, takomisen jälkeen aihiolla on jo suunniteltu perusmuoto, ja jäljelle jäävä työstövara on merkityksetön verrattuna koko aihion jyrsintään. Tässä tapauksessa, jyrsinnän lisäksi, se voidaan myös käsitellä tehokkaalla hiomalla. Verrattuna kovapintajyrsintään, Tehokas hionta ei voi vain parantaa työkappaleen muodon tarkkuutta, mutta myös parantaa työkappaleen pinnan karheutta. On olemassa monia tehokkaita hiontamenetelmiä, yleensä nopea hionta pallomaisilla hiomalaikoilla ja nauhahionta pienihalkaisijaisilla hihnapyörillä.
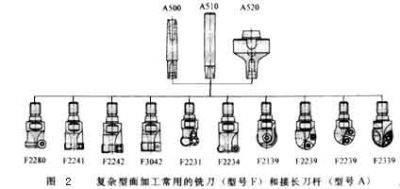
Jyrsintyyppi
Työkalujen ja muottien kolmiulotteiset vapaamuotoiset pinnat käsitellään yleensä 5-akselisessa työstökeskuksessa. Koska työkappaleen materiaali on enimmäkseen seosterästä tai työkaluterästä, työstökoneen rakenteessa ja numeerisen ohjausjärjestelmän tulee ottaa huomioon työstöprosessin tuottavuuden ja työkappaleen tarkkuuden vaatimukset, ja tee asianmukainen asettelu ja optimointi tämän perusteella. Sen varmistamiseksi, että työstökone ei joudu liikaa muodonmuutoksia leikattaessa erilaisia muottimateriaaleja, työstökoneen jäykkyyden tulee olla etusijalla koneen sijoittelua määritettäessä. Suuremman akselin työstökeskus, suurin osa portaalirakenteesta, Joissakin pienikokoisissa viisiakselisissa työstökeskuksissa käytetään joskus myös korkeaa pylväsrakennetta.
1990-luvun alusta lähtien, lähes kaikki monimutkaiset muodot on käsitelty tuotannossa nopealla leikkauksella. Tarkoituksena on parantaa tuotannon tehokkuutta, vähentää tuotteen kustannuksia, ja samalla parantaa työkappaleen muototarkkuutta ja vähentää pinnan karheutta. Täyttääkseen nopean leikkauksen tarpeet, työstökoneen kara käyttää lähes poikkeuksetta sähkökaraa. Karan nopeus vaihtelee portaattomasti käytetyn työkalun halkaisijan mukaan, ja nopeus vaihtelee useista tuhansista kierroksista kymmeniin tuhansiin kierroksiin minuutissa. Liukupöydän käyttöjärjestelmä eroaa myös tavanomaisista nopean leikkauksen työstökeskuksista. Yleisesti käytetty järjestelmä, jossa on nopea käyttömutteriruuvikokoonpano ja lineaarinen moottorikäyttö, suurin syöttönopeus voi olla 100 metriä / min tai enemmän.
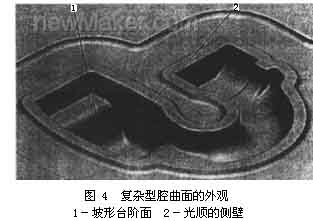
CNC-työstön monimutkaisen ontelon pinnan ulkonäköpiirustus
Kun käsitellään monimutkaisia pintoja, työstökoneen CNC-järjestelmän on myös täytettävä joitain erityisvaatimuksia. Esimerkiksi, CNC-työstöohjelmat monimutkaisille pinnoille generoidaan yleensä CAD/CAM-ohjelmistolla. Profiloitu ohjelma vaatii usein useita megatavuja (Tavu) säilytystilasta, eikä NC-ohjelmia voi enää siirtää levykkeellä. Siksi, the CNC system must have the function of networking with other computer systems in order to receive the CNC program directly from the CAD/CAM. Lisäksi, the numerical control system must also adopt advanced control technology, first of all, it requires the function of LookAhead. In other words, before the machine tool processes a certain track, the data system analyzes the surface to be processed in advance. According to the curvature of each point of the curved surface and the connection relationship of each adjacent point, the feed speed of the machine tool is appropriately adjusted to achieve the highest productivity under the premise of ensuring the accuracy of the workpiece. In order to reduce dynamic errors during processing, the new servo error correcting data using a conventional tandem system is no longer proportional integral derivative (PID) controller, instead of using the state regulator by compensating for the position and speed state parameters. Using this kind of regulator can completely eliminate the drive hysteresis error, compensate for the nonlinear error caused by the gap or friction, and even offset certain vibrations of the machine tool. So as to meet the requirements of improving the shape accuracy of the workpiece and reducing the surface roughness.
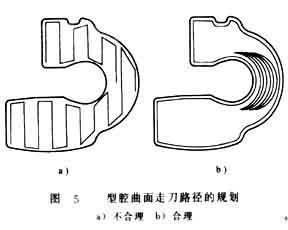
Setting of the cutting path of the cavity surface
The tool system plays a decisive role in the production efficiency and processing quality when processing complex profiles. When selecting a cutting tool system, we must first start from the geometry of the parts to be processed, and reasonably use the types of cutting tools. Kuten kuvasta näkyy 1, the geometry of each part is very different. If only a ball-end milling cutter is used for processing, a ball-end milling cutter with a small diameter must be selected, which makes it difficult to improve processing efficiency. Lisäksi, the arc radius of some parts is so small that it cannot be processed even with a small ball end mill. Siksi, taking into account the requirements of both production efficiency and workpiece shape, other types of milling cutters must be equipped on the five-axis machining center for processing complex profiles, such as end mills and three-face milling cutters.
Kuva 2 shows some types of milling cutters. As long as the size permits, regardless of the shape of the tool, the cutting edge should be a milling insert with a convertible clamp. Such knives can be combined in a variety of ways because of the blade and the body, and the blade and the body can be produced by different companies. Siksi, large-scale specialized production can be formed, which not only helps to improve the quality of the tool, but also helps to reduce the production cost of the tool.
Tällä hetkellä, most of the indexable blades on the market use CVD coated carbide blades. In order to achieve higher pseudo-abrasion resistance, the indexable inserts are all multi-layered coatings. Bizhi Al2O3 can improve the chemical stability of the blade. TiN and TiCN can enhance the wear resistance of the blade. In order to enhance the sharpness of the blade, matalan lämpötilan CVD-menetelmän lisäksi, pinnoite voidaan valmistaa myös PVD-menetelmällä. Joillakin käsittelyillä on terälle erittäin tiukat vaatimukset. Terässä tulee olla terävä leikkuureuna valmiin pinnan karheuden vähentämiseksi, mutta niillä on myös korkea kulutuskestävyys työkappaleen muototarkkuuden varmistamiseksi. Tässä tapauksessa, on käytettävä useiden pinnoitteiden yhdistelmää. Sen varmistamiseksi, että joidenkin terien käyttö on idioottivarmaa, pinnoitekerrosten lukumäärä voi olla niinkin suuri kuin 100.
Työkalun käyttöikä liittyy läheisesti syöttönopeuteen, leikkausnopeus ja leikkaussyvyys. Optimaalinen leikkausmäärä on usein pieni alue, joka tulee määrittää tietyn työkalun ja työkappaleen materiaalin mukaan.
Lisäksi, leikkausstrategioita, kuten: Työkalun polun suunnittelu, työkalun akselin pinnan normaalivektori (pinnan normaali suunta tässä vaiheessa) tai eri menetelmiä pitkin pintatangenttivektoria (pinnan tangentin suunta tässä kohdassa), jne., ovat myös avaintekijä monimutkaisten pintojen käsittelyssä . Se ei vaikuta vain käsitellyn työkappaleen pinnan karheuteen, mutta se vaikuttaa myös työkappaleen muotoon ja mittatarkkuuteen. Kuva 3 näyttää erilaisia leikkausstrategioita, joita käytetään lieriömäisen pinnan työstyksessä. Leikkaamiseen kehän suunnassa, työkalun rata on interpoloitava kaksiakselisessa vivustossa. Kun leikkaat generatrix-suuntaa pitkin, työkalun tarvitsee suorittaa vain yksiakselinen interpolointi. Lisäksi, eri leikkausmenetelmillä on suuria eroja työkalujen kulumisessa. The tool wear during down milling is significantly lower than that of up milling, and the wear during reciprocating milling is much greater than that of unidirectional milling.
In order to improve the stability of the machining process, when optimizing the cutting strategy, the continuity of the cutting must be ensured, and the cutting motion and idle stroke must be reduced as much as possible in order to shorten the cutting time. When the rough milling of steel, must ensure continuous climb milling, to minimize the peak of the cutting blade during cutting of the amount of fluctuation.
When processing the workpiece shown in Figure 4, if the row cut trajectory section processing shown in Figure 5a is used; The movement of the tool is very unreasonable, the cutting conditions are very unsatisfactory, the processing time is 33min, and the surface roughness of the workpiece is 6-9μm. If you switch to the circle-cutting path shown in Figure 5b for processing, the processing time is about 27 pöytäkirja. Samaan aikaan, the roughness of the workpiece can also be reduced to 2 ~ 4μm.