5-El mecanizado de ejes es una abreviatura general de tecnología de mecanizado de cinco caras y tecnología de mecanizado simultáneo de 5 ejes..
In the case of one-time installation and clamping, five-face machining technology is used for complex polyhedral parts. Molienda, perforación, boring and other processing of all planes except the installation base surface can be conveniently completed by the additional machine tool rotary axis; No solo eso, but when machining inclined surfaces, the tool or workpiece can be rotated to make the tool closer to the machined surface. Shortening the extension length of the tool is beneficial to improve the cutting ability and tool life; Además, it can also solve the processing of the concave surface that cannot be solved by the linear axis movement.
Another feature of five-face machining is that the rotary axis only performs indexing positioning, and does not participate in the cutting path interpolation movement. Such as the processing of V-shaped engine block: A horizontal machining center with A/B axis double pendulum table is used. The A-axis swing can complete the processing of the V-shaped inclined surface and the cylinder hole, and then the B-axis indexing can complete the processing of the crankshaft bearing hole and its thrust surface.
Five-axis linkage processing technology refers to the processing technology that a complex shape surface needs to use 5 independent axes to perform numerical control interpolation movement together to obtain a smooth and smooth surface. Although theoretically any complex surface can be represented by X, Y, Z three-axis coordinates, the actual machining tool is not a point, but an entity with a certain size. In order to avoid interference between the tool and the machined surface when twisted surface processing space, and to ensure consistency of cutting conditions for each surface point, need to adjust the angle between the tool axis and the surface normal vectors on the 2D direction. Compared with three-axis linkage, five-axis linkage can reduce machining error and surface roughness to 1/3~1/6.
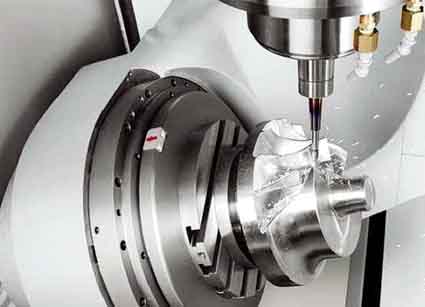
5-fresado simultáneo de ejes