¿Qué es la fundición a alta presión?? Costo del producto y precio de las piezas fundidas a presión fabricadas en masa.
Fundición a presión a alta presión (HPDC) Es un proceso de fundición para producción en serie o en masa.. Para ello se suelen utilizar aleaciones fundidas con un punto de fusión bajo..
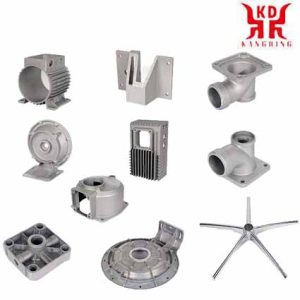
China Fundición a presión
En fundición a presión, el líquido fundido se presiona en un molde de fundición a presión (molde de fundición, cavidad) bajo alta presión de aprox.. 10 a 200 MPa y a una velocidad de llenado del molde muy alta de hasta 12 metro / s, donde luego se solidifica. Lo especial del proceso de fundición a presión es que con un molde permanente, es decir. h. sin modelo. Como resultado, El molde sólo se produce una vez para una serie de componentes idénticos., pero con un esfuerzo de producción significativamente mayor. De este modo, se logra un alto rendimiento, especialmente en una máquina de fundición a presión de cámara caliente en la que el recipiente de fundición y el pistón de fundición están constantemente en la masa fundida.. En el caso de aleaciones con un punto de fusión más alto., Se utiliza el proceso de fundición a presión en cámara fría.; El conjunto de fundición se encuentra fuera de la masa fundida metálica..
¿Cómo funciona el proceso de fundición a alta presión??
En el proceso de fundición a alta presión., Se inyecta metal fundido o aleación de metal en el molde a alta velocidad y alta presión..
Las máquinas de fundición a presión horizontales de alta presión garantizan que el troquel esté completamente cerrado.. Se clasifican según la cantidad de fuerza de sujeción que pueden aplicar y pueden variar desde 550 a 5700 montones.
Dependiendo del metal utilizado, La unidad de inyección que llena el molde puede ser una cámara caliente o una cámara fría.. En fundición a presión en cámara caliente, El metal se mantiene dentro de la propia máquina de fundición a presión., luego es aspirado hacia la cámara y la acción del pistón de inyección lo introduce en el molde. Estas partes de la máquina están siempre en contacto con el metal fundido..
En el proceso de cámara frigorífica, El metal se funde primero en un horno separado y se transfiere a un horno de mantenimiento.; luego se vierte en una cámara de llenado y se inyecta en el molde.. ofrece una amplia gama de máquinas de fundición de alta presión con cámara fría.
La fundición a presión compite con el moldeo por inyección de plásticos. Los materiales metálicos presentan en casos concretos ventajas que aseguran el mercado de los artículos de fundición a presión.
Los materiales más utilizados son
Aluminio (aluminio fundido)
Zinc (zinc fundido a presión)
Magnesio (fundición a presión de magnesio)
tabaco de silicona
![]() Fundición a presión de la carcasa del motor |
![]() Fundición a presión de farola |
![]() Distribution box die casting |
Die-cast parts properties
Die-cast parts have smooth, clean surfaces and edges. Además, this method allows wall thicknesses to be thinner than other methods. With zinc, Por ejemplo, the parts can have a wall thickness of 1 mm and with aluminum of 1.4 milímetros, in exceptional cases even less than 1 milímetros.
The achievable tolerances are ± 0.05 to ± 0.15 milímetros, so that one speaks of an exact or finished casting. For large cast parts, sin embargo, slightly larger tolerances are required.
It is possible to use parts made of other materials, como. B. sockets, threaded bolts or pins to be poured in. Internal threads are produced directly with rotatable steel cores, which can then be removed again later. In contrast to other processes, the casting is called “shot” here. It is possible to carry out up to 1000 shots per hour (depending on the size of the machine). Depending on the casting material, the mold life is up to 2,000,000 shots (aleaciones de zinc).
With aluminum, service lives of approx. 80,000 a 200,000 shots are achieved. Por mucho tiempo, die-cast aluminum was considered unsuitable for fusion welding and heat treatment. In the meantime, extensive investigations have made it possible to manufacture die-cast aluminum that is suitable for fusion welding and heat treatment. The particularly low-warpage beam welding processes (electron beam and laser beam welding) should be emphasized here – for optimum strength properties. Sin embargo, for optimal results it is necessary and advisable to consider the requirements of the process when designing. Además, sin embargo, die-cast aluminum can also be welded very well using friction welding processes such as friction stir welding.
Die casting machine
Die casting machines usually consist of a mold clamping unit that is used to open and close the die casting mold. Components of the mold clamping unit (also called the closing part) are:
a fixed machine plate (also called a fixed plate) to hold the fixed casting mold half and, in the cold chamber process, the casting set
a movable machine plate (also mobile plate) to accommodate the hydraulic ejector and the movable mold half
the four guide pillars on which the movable machine platen is guided
the toggle lever system (consisting of a cylinder plate (also called crosshead), short and long lever and cross head)
the lock cylinder
The liquid metal is pressed from the casting chamber into the mold with a casting piston. Depending on the type of machine used, a distinction is made between the warm and cold chamber processes. The casting piston is driven by the casting unit’s drive. The drive piston is usually acted upon by a hydraulic pressure accumulator. In some cases the plunger is driven electrically.
Die casting machine peripherals
The peripheral units work in the vicinity of the die casting machine. These are process engineering devices that are necessary for the automatic process to run.
Mold spray machine or manipulator for mold spray or fixed nozzles
Heating and cooling devices
Extraction devices
Dosing oven or ladle
Vacuum-assisted die casting process
The vacuum-assisted die-casting process with forced ventilation enables workpieces with little or no gas inclusions. The cavity and the filling chamber are evacuated at the start of casting, so that the air contained therein and the gases produced are sucked out during casting and so fewer or no air inclusions can form in the melt.
Die casting recompression
A similar effect is achieved here by high compression in the phase before the final solidification of the workpiece. Pores and air pockets are significantly reduced.
As during the solidification of the melt. h there is a jump in volume during the transition from liquid to solid, volume deficits inevitably occur in the interior of thick-walled components.
In order to compensate for this effect of liquid shrinkage, the so-called squeeze process can be used to compress the solidifying melt. For this purpose, the pulpy melt is compressed by means of a “squeeze pin” in the die casting mold in areas where a volume deficit is expected.
Die casting mold and tool
The die-casting tools required in the die-casting process are manufactured in the tool shop or in the mold shop. Special materials or high-strength hot-work steels in accordance with DIN EN ISO 4957 are usually used as the material for the casting molds. A selection is shown in the following table.
Short material name | Material number |
32CrMoV 12-28 | 1.2365 |
X37CrMoV 5-1 | 1.2343 |
X40CrMoV 5-1 | 1.2344 |
Die casting phase sequence
En fundición a presión, a pre-tempered (100 a 300 grados Celsius) permanent mold (two or more parts) is filled with molten metal under pressure at high speed. The actual casting process can be divided into three phases.
The pre-filling phase is used to convey the melt in the casting chamber up to the gate. El aire comprimido en el sistema de bebedero durante la primera fase puede escapar a través de los canales de ventilación y a través del plano de moldeo debido a la velocidad relativamente baja del pistón. (0.05–0,7 metros / s).
Durante la fase de llenado del molde, El pistón de fundición presiona la masa fundida en el molde a una velocidad muy alta. (0.4–6 metros / s). El tiempo de llenado del molde es extremadamente corto, de 5 a 60 ms.. Por tanto, es prácticamente imposible ventilar el molde..
En la fase de mantenimiento de la presión al final del llenado del molde., Se genera una presión final estática muy alta.. El aire atrapado cuando se llena el molde se comprime y la pieza fundida se repone.
Presión de lanzamiento
Los diferentes materiales de fundición requieren cada uno una presión de fundición diferente.. Las aleaciones de aluminio y magnesio se funden a 300-1200 bar., zinc a 130-250 bar y latón a 300-1000 bar. La resistencia de una pieza de trabajo es mayor a alta presión de fundición..
![]() Tratamiento superficial de piezas fundidas a presión. |
![]() Fundición a presión de la carcasa del radiador. |
![]() Fundición a presión de la carcasa de la picadora de carne. |
Comportamiento de contracción de las masas fundidas de aluminio y silicio.
Si vierte aluminio líquido a aproximadamente 700 ° C en la cavidad del molde de tal manera que el molde se llene exactamente, luego el volumen del metal disminuye a temperatura ambiente en un total de aproximadamente 1.3% debido a su contracción. De este total, 0.05% se debe a la contracción del líquido, 0.75% a la solidificación y 0.5% a la contracción sólida.
Este déficit de volumen de 1.3%, que no es mucho más pequeño con aleaciones de aluminio que con metal puro, se hace visible en la pieza fundida que se solidifica en forma de defectos de volumen. Además de la contracción normal, Estos defectos ocurren en parte como marcas de hundimiento., partly as macro-blowholes or as shrinkage pores.
The shrinkage cannot take place as unhindered in a die casting mold as it is in a sand casting mold, Por ejemplo. In foundry technology, the term “shrinkage” means, in addition to a process, a measure, namely the percentage dimensional deviation of the cooled casting from the dimensions of the mold at operating temperature. Whether shrinkage can take place freely or with hindrance depends almost exclusively on the geometric shape of the cast part. It is therefore possible that the shrinkage rate of 0.5% that is generally used today can be used for many dimensions on one and the same cast part, while 0.4% could still be too much for other areas. The mold dimensions are to be determined taking into account a shrinkage drawing of the die-casting alloys concerned.
Shrinkage for die casting
Die-cast alloy | Shrinkage in% |
Aleaciones de aluminio | 0,5–0,7 |
Magnesium alloys | 0,5–0,8 |
Zinc alloys | 0,4–0,6 |
Influence of the alloying elements in aluminum casting alloys
Silicon
structure
With 12.5% silicon, aluminum forms a eutectic1 that melts at 577 °C. In the binary system there is no connection between aluminum and silicon. The solubility of silicon in solid aluminum is 1.65% in equilibrium at 577 ° C., drops to 0.22% at 300 °C. and even further at lower temperatures. If an alloy has more silicon than the solubility corresponds, the structure contains not only aluminum mixed crystals but also silicon crystals. If the cooling rate is not particularly fast, the silicon solidifies in the eutectic mixture in the form of angular crystals, needles and plates. These forms of training are made possible by small admixtures of z. B. sodium, strontium, antimony or phosphorus influenced. Die casting causes similar effects due to the rapid solidification.
Eutectic1 is a mixture of alloying elements, which of all possible compositions has the lowest melting point. The eutectic point, e.g. P.ej .: an Al-Si alloy, es 12.5% y 577 °C.
Casting properties
The higher the Si content, the more advantageous it has on the flow and mold filling capacity. The flowability deteriorates as the Si content decreases.
Influence of silicon on the feeding behavior
With an increasing Si content, encima 11%, the macro-void volume increases sharply. The incidence volume runs in the opposite direction to the macro void volume. With less than 9% Y, thick-walled parts tend to have suction cavities. The feeding options for macro-blowholes are limited in die casting (thick-walled cast parts lying from the gate cause some problems, since accumulations of material during the shot are filled last and then solidify). In hypoeutectic alloys, coarse grain becomes noticeable as a result of overheating from suction points.
A near-eutectic melt (around 11% Y) causes stronger macro-voids. Eutectic and near-eutectic Al-Si melts, which lead to a “granular” or “refined” structure, solidify with the formation of a peripheral shell (exogenous solidification), so that these melts are not susceptible to sucking holes.
hierro
A higher iron content has a positive effect on die casting (e.g., alloy EN AC-AlSi9Cu3 (Fe) máximo. 1.2%), as it reduces the tendency of the metal to stick to the mold surface. Within the tolerance limits, iron normally has no influence on the casting properties. Unintentional increase due to improper melting or working methods in the foundry can lead to embrittlement of the cast parts and undesired formation of cavities, hot cracks or sink marks. At low holding and pouring temperatures, gravity segregations often occur, which collect on the floor of the furnace. The segregation products consist of iron, manganese and silicon. The hardness of segregation products is 500–1000 Vickers.
cobre
Copper additives reduce the solidification shrinkage. Como resultado, copper-containing Al alloys permit pressure-tight castings more easily. Cu additives have a positive influence on strength and machinability. Copper reduces the corrosion resistance.
manganese
Manganese addition of a few tenths of a% reduces the negative influence of iron on elongation and impact resistance. Sin embargo, si el hierro y el manganeso se encuentran en un contenido mayor, pueden hacerlo en condiciones de fusión desfavorables, e.g. B. por bajas temperaturas de mantenimiento, llevar a una segregación dura.
magnesio
Con la presencia simultánea de silicio., cobre o zinc, El magnesio conduce a una mejora en la maquinabilidad debido a un aumento en la dureza.. El magnesio no tiene ninguna influencia negativa sobre el comportamiento frente a la corrosión.. El magnesio también resulta cada vez más interesante en la industria del automóvil, especialmente por su menor peso.
níquel
La ventaja más importante de la adición de níquel es el aumento de la resistencia al calor.. Especialmente los pistones y las culatas son los principales campos de aplicación de las aleaciones de aluminio que contienen níquel..
zinc
Los diferentes contenidos de zinc dentro de los límites de tolerancia generalmente no influyen. En fundición a presión, El contenido de Zn junto con el magnesio se reduce ocasionalmente en piezas propensas a agrietarse por calor..
titanio
El titanio se añade a las aleaciones de Al principalmente como refinador de grano hasta un máximo de 0.15%. En el caso de arena y aleaciones de fundición en molde permanente., es un componente de aleación para refinar granos.
dirigir
En estado solido, El plomo no se disuelve en forma de finas gotas.. Within the tolerance limits (<0.1%), El Pb no influye notablemente en las propiedades de la aleación..
estaño
Con un contenido de más de 0.02%, El estaño se separa a lo largo de los límites de los granos y tiene un efecto muy negativo sobre el comportamiento de craqueo en caliente si se excede la tolerancia normal. – especialmente en fundición a presión.
Comparación de fundición a presión y moldeo por inyección.
Los costes de inversión en máquinas de fundición y los elevados costes de fabricación del molde son aproximadamente comparables. En ambos procesos, large numbers of pieces have to justify these high investment costs. After that, the raw material costs have priority.
Die-cast metal components have a significantly higher flexural strength (rigidity) than injection-molded ones; it can be up to 20 times higher. The workpieces produced in die casting can still be subjected to loads at higher temperatures (aluminum up to approx. 450 °C). In the case of injection-molded materials, the strength and rigidity decrease sharply at higher temperatures (from 100 °C); the only exceptions are expensive special plastics. Another advantage is that when the components (with the exception of zinc) are stressed, there is no creep, as is the case with many injection-molded workpieces. Die-cast parts have a much better structural stability, es decir. a mechanically processed surface remains a surface, whereby the surface of a plastic part deforms much more easily. Además, some injection-molded plastics change shape under climatic conditions. Die-cast materials have electromagnetic shielding and are resistant to organic solutions. Además, recycling is possible without any loss of quality.
Injection molded components are cheaper if standard materials are used. Además, color can be used for injection molding. Another advantage is the lower weight compared to die-cast workpieces. The latter also have poorer corrosion properties. Además, the production of die-cast metal components is more complex and “complicated” geometries are sometimes not possible.