En el reciente prototipo de mecanizado de un nuevo producto de una empresa, some of the workpieces are made of stainless steel and other difficult-to-CNC machining materials, such as 3Cr13, 3Cr13Mo, 40CrNiMo, 9CrMoV, etc.. Workpieces of this type have also been processed in the past. Although the production efficiency is low, the batches are small, the quantity is small, and the production cycle is short. After mass production, the problems were exposed, the tools were severely worn, the number of sharpenings increased, and the downtime and machine tool adjustment time increased. The surface roughness of the workpiece is poor, the chips are not easy to curl and break, and the processed surface of the workpiece is scratched, which directly affects the quality of the workpiece.
The material of the workpiece is 3Cr13Mo, and the process requirements are processed by CNC lathe except for the grinding of each outer circle of Ra0.8µm. The strength, elongation, reduction of area, and impact performance of 3Cr13Mo steel are higher than those of 40 steel and 45 acero. It is a medium carbon martensitic stainless steel with high strength and good plasticity. During the trial production of the workpiece, the turning test of 3Cr13Mo steel was carried out according to the technological method of turning ordinary carbon steel. The result is severe work hardening during cutting, high cutting resistance, high cutting temperature, and easy sticking of the tool, resulting in built-up edge. Causes the size of the workpiece to change and affects the shape and position tolerance and surface roughness of the workpiece.
In response to the above problems, measures have been taken from multiple aspects to make the processed surface of the workpiece reach the size and surface roughness required by the pattern, and to ensure high production efficiency.
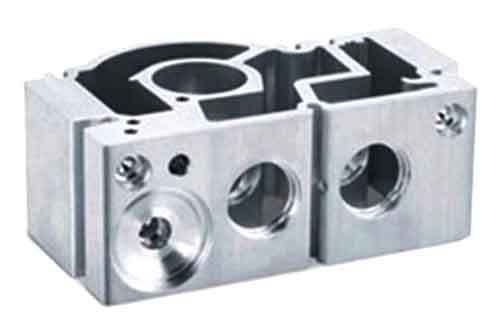
Machining quality control of stainless steel parts
1. Heat treatment changes the hardness of the material
The different hardness of martensitic stainless steel after heat treatment has a great influence on turning processing. Mesa 1 shows the use of YW2 material turning tools after turning and heat treatment of 3Cr13M material workpieces of different hardness. It can be seen from Table 1 that although the annealed martensitic stainless steel has low hardness, its turning performance is poor. This is because the material has large plasticity and toughness, uneven structure, strong adhesion and fusion, and it is easy to produce knife edges during the cutting process, and it is not easy to obtain a good surface quality. After quenching and tempering, the 3Cr13Mo material workpiece with a hardness below 30HRC has better machinability and is easy to achieve better surface quality. Although the surface quality of the workpiece with a hardness greater than 30HRC is better, the turning tool is prone to wear. Por lo tanto, the quenching and tempering treatment is carried out before the machining, the hardness reaches 25-30HRC, and then the cutting is carried out.
2. Cutting tool materials for machining martensitic stainless steel
The cutting performance of the tool material is related to the durability and productivity of the tool. The manufacturability of the tool material affects the manufacturing and sharpening quality of the tool itself.
The principle of selecting materials for the cutting part of the tool is to have high wear resistance and maintain its cutting performance at a higher temperature.
Currently commonly used turning tool materials are: High-speed steel and cemented carbide. Because high-speed steel can only maintain its cutting performance below 600°C, the high temperature generated during stainless steel cutting is often higher than 600°C. And cemented carbide has better heat resistance and wear resistance than high-speed steel, so tools made of cemented carbide materials are more suitable for the cutting of stainless steel. Under the conditions of the same cutting parameters, a turning comparison test was carried out on tools of several alloy materials.
The external turning tool with TiC-TiCN-TiN composite coating blade has high durability, good surface quality and high productivity. This is because the blade coated with cemented carbide material has better strength and toughness. And because its surface has higher hardness and wear resistance, smaller friction factor and higher heat resistance, it has become a good tool material for turning stainless steel. Limited to cutting blades that do not have this material, the comparison test in Table 2 shows that the cutting performance of YW2 cemented carbide is also better, para que pueda elegir las cuchillas de material YW2 como cuchilla de corte.