5-Impulsor del turbocompresor de mecanizado de ejes.
El impulsor del turbocompresor de alta precisión es el componente clave más estricto. Mediante mecanizado avanzado de 5 ejes, Cada día se pueden fabricar cientos de impulsores de turbocompresor.. Usando fresado de aluminio sólido, en comparación con el antiguo sobrealimentador fundido, no sólo tiene la ventaja de precio sino también una mayor precisión de tolerancia.
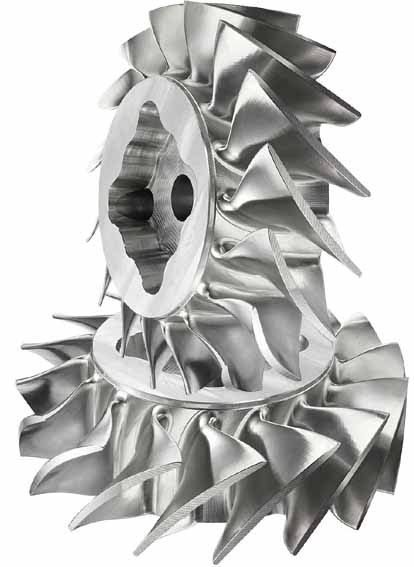
5-Impulsor del turbocompresor de mecanizado de ejes.
El turbocompresor es un 100% 5-pieza de trabajo de mecanizado del eje, sin recorte recto o mecanizado de arco puro. La forma de la rueda es más o menos cónica, con una gran cantidad de cuchillas de perfil que irradian en espiral desde el cubo y a lo largo del eje del cono. En cada momento de procesamiento durante el procesamiento del aumento de la velocidad, La ruta de fresado cambia a lo largo de todos los ejes de procesamiento, Entonces, cada eje siempre está en el modo de aceleración o desaceleración, que causará aceleración de gravedad severa durante el procesamiento.
El procesamiento del impulsor del turbocompresor de una determinada planta de fabricación se completa con cuatro centros de mecanizado de cinco ejes de alta velocidad modelo 300X, que son productos de Mooretoolco de Bridgeport, Conn.. Lo más llamativo de esta máquina es que el huso horizontal de posición fija solo puede moverse a lo largo de los ejes X e Y. Solo restringir el movimiento del eje principal en la dirección horizontal, y no cambia la extensión del eje principal. Esto puede aumentar la rigidez y aumentar la amortiguación de la vibración cuando la fuerza inercial es grande, que es muy común en el procesamiento del sobrealimentador.
El diseño giratorio de la mesa de la pieza de trabajo (mesa superior) Evita la compensación del centro de gravedad del eje de la bisagra durante el corte de contorno complejo, y mejora la respuesta y precisión del camino de corte. Se puede quitar un huso horizontal, sin duplicación doble.
Lo grande, El hierro fundido y la estructura horizontal de caja horizontal de tres puntos mejora la estabilidad y la absorción de vibraciones. La tasa de alimentación de contorno de procesamiento puede alcanzar el 787ipm, la velocidad puede alcanzar 1.181ipm, y la aceleración puede alcanzar 653 pulgadas./SEC2 o 1.7 g en el modo de cinco ejes.
FSP300 también incorpora una alta ganancia, Sistema de servo digital de circuito cerrado que puede posicionarse rápidamente, Alta tasa de alimentación y aceleración en todos los ejes. Moore puede obtener esta ventaja porque captura la esencia del diseño de la máquina herramienta y minimiza los efectos de los efectos armónicos, vibración y choque coordinando máquinas herramientas y sistemas de control. Y haga el sistema de control Siemens Sinumerik840d de la máquina herramienta a un nivel de trabajo normal. Rob Smith, Gerente de Moore, dicho, "Cuando una máquina herramienta de baja rigidez se ejecuta a la velocidad de los grifos, con una ganancia tan alta, El sistema de control debe volverse dinámicamente inestable ".
Piezas de turbocam: Al procesar los impulsores del aluminio sólido, Use MoOREFSP300XHMCS para eliminar más de 50% del peso en el sistema de producción automatizado de TAPS. Y termine el procesamiento del impulsor en aproximadamente 1 hora mientras mantiene el error de volumen dentro 0.001 pulgadas.
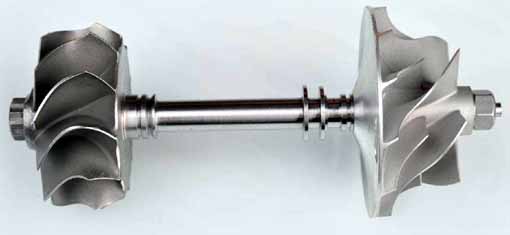
5-impulsor cónico de mecanizado del eje
5-impulsor cónico de mecanizado del eje
Dijo que el sistema de control de Siemens puede proporcionar una alta velocidad de procesamiento y procesamiento y un verdadero mecanizado de cinco ejes.. Y no hay necesidad de detener ningún eje durante el procesamiento. Detener el eje reducirá en gran medida la velocidad de procesamiento en el procesamiento de contornos complejos.
El sistema de control 840D puede controlar 10 canales, 10 grupos de patrones, y 31 ejes. Para satisfacer la alta demanda de ejes y canales, La potencia informática y el área de almacenamiento de la NCU se pueden ampliar y combinar. Esto permite que 840D conecte 248 hachas y husos en un CNC.
Un corte de sobrealimentador de 4 pulgadas de 2618 aluminio. Uso del dispositivo de alimentación al recíprocado diseñado por Moore, la máquina herramienta puede ejecutarse desatendida. Cortar 50% del peso y complete el procesamiento del refuerzo dentro 1 hora, y el error de volumen puede llegar 0.001 pulgadas.
La calidad de la máquina herramienta se verificó mecanizando un turbocompresor de 10 pulgadas. El mecanizado requerido 7 cortes de contorno y 7 La herramienta cambia desde el comienzo de la entidad.
FSP300 terminó el procesamiento en tres horas y todas las superficies cumplieron con los requisitos de tamaño y acabado. Para este corte, la velocidad de alimentación está en el rango de 190 a 282 SFPM, mientras que la velocidad del huso está en el rango de 24,000 a 40,000 rpm.
1005Tapsactivación: El diseño giratorio de mesa en la mesa de la tabla de la pieza de trabajo Moorefsp300XHMCS evita el centro del cambio de gravedad del eje de la bisagra durante el complejo proceso de corte de contorno de los grifos, y mejora la respuesta y precisión del camino de corte.