In den vergangenen Jahren, Im Zivilschutz und in anderen Bereichen nimmt die Nachfrage nach einer Vielzahl von CNC-Bearbeitungsprodukten zur Miniaturisierung weiter zu, die Funktion der winzigen Geräte, die Komplexität der Struktur, Auch die Anforderungen an die Zuverlässigkeit steigen. daher, Es ist von großer Bedeutung, wirtschaftlich realisierbare Mikrobearbeitungstechnologien zu erforschen und zu entwickeln, ist in der Lage, dreidimensionale geometrische Formen und vielfältige Materialien zu verarbeiten, und Strukturgrößen im Mikrometer- bis Millimeterbereich. Derzeit, Mikroschneiden ist zu einer wichtigen Technologie geworden, um die Einschränkungen der MEMS-Technologie zu überwinden. Die Mikrodreh- und Frästechnologie hat sich aufgrund ihrer hohen Effizienz zu einem sehr aktiven Forschungsschwerpunkt entwickelt, hohe Flexibilität, und die Fähigkeit, komplexe dreidimensionale Formen und eine Vielzahl von Materialien zu verarbeiten.
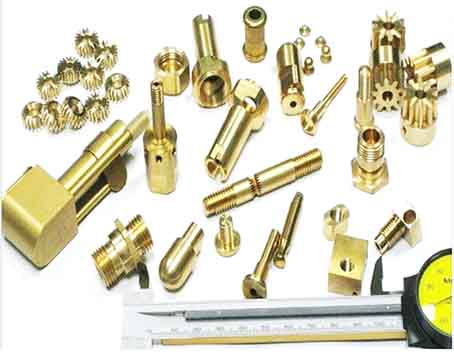
Drehen und Fräsen von Miniatur-Präzisionsuhren, Handyteile
In 1959, Richard P. Feynman (Gewinner des Nobelpreises für Physik in 1965) schlug die Idee von Mikromaschinen vor. Der erste Silizium-Miniaturdrucksensor kam auf den Markt 1962, und das Klima entwickelte Mikromaschinen wie Zahnräder, Zahnradpumpen, pneumatische Turbinen und Kupplungen mit einer Größe von 50-500μm. In 1965, Die Stanford University hat eine Silizium-Gehirnelektrodensonde entwickelt, und später gelang es ihm, Rastertunnelmikroskope und Miniatursensoren herzustellen. In 1987, Die University of California in Berkeley entwickelte eine elektrostatische Miniaturmaschine aus Silizium mit einem Rotordurchmesser von 60–12 μm. Es zeigt das Potenzial der Silizium-Mikrobearbeitungstechnologie zur Herstellung kleiner beweglicher Strukturen und der Kompatibilität mit integrierten Schaltkreisen zur Herstellung winziger Systeme.
Die Erforschung und Anwendung traditioneller Mikrofräs- und Drehtechnologien erfolgt hauptsächlich: Mikroschaftfräser mit Durchmessern im Bereich von mehreren zehn Mikrometern bis 1 mm werden für die Mikrobearbeitung auf konventionellen Ultrapräzisions-Werkzeugmaschinen eingesetzt. Da diese Werkzeugmaschinen hauptsächlich zur Bearbeitung nicht kleiner geometrischer Teile mit hoher Präzision eingesetzt werden, Sie erfordern in der Regel teure Konstruktions- und Herstellungsprozesse, um die gewünschte Zielgenauigkeit zu erreichen. Zur Bearbeitung kleinster Teile, es fehlt die nötige Flexibilität, und die Verarbeitungskosten sind hoch und die Effizienz niedrig. Miniaturisierte Verarbeitungsgeräte haben den Vorteil, Platz zu sparen, Energie sparen, leicht umzuorganisieren, und niedrige Kosten. In den vergangenen Jahren, Der Einsatz von Mikrobearbeitungsgeräten zur Mikrofräs- und Drehbearbeitung hat große Aufmerksamkeit erregt, und der Einsatz von Mikrowerkzeugen auf Mikrowerkzeugmaschinen hat den Mikrobearbeitungsprozess realisiert. In der Forschung der Mikrofräs- und Drehbearbeitungstechnologie, Die Forschung konzentriert sich hauptsächlich auf die Oberflächenqualität, Schnittkraft, Werkzeugverschleiß und Lebensdauer, Chipzustand, und Bearbeitungsfähigkeit von Kleinteilen.
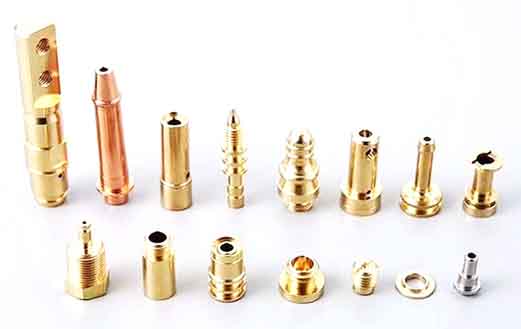
Bearbeitung kleinster Präzisionsteile
Beim Fräsen und Drehen, Der Belastungszustand des Werkzeugs ist äußerst kompliziert, und es ist ständig mechanischen und thermischen Schockbelastungen unterschiedlicher Größe und Position ausgesetzt. Weil der Vorschub pro Zahn beim Mikrofräsen und Drehen geringer ist als (oder gleich) der Radius der Schneidkante des Werkzeugs, Der Schneidvorgang geht von Scherung in Reibung über, Extrudieren oder Pflügen;
Zusätzlich, aufgrund der hohen Schnittgeschwindigkeit und großen Stoßbelastung, Die Mikroschneidkraft unterscheidet sich stark von der herkömmlichen Fräskraft.
Bao und Tansel untersuchten die Schnittkraft bei der Verwendung von Schaftfräsern mit Mikrodurchmesser zum Mikrofräsen, und schlug ein verbessertes Schnittkraftmodell vor. Das Modell wird durch die Berechnung der Spandickenänderungen ermittelt, die durch die Bahn der Werkzeugschneide verursacht werden, wenn sich das Werkzeug dreht und vorwärts bewegt. Zusätzlich, der Einfluss des Verhältnisses von Vorschub pro Zahn zum Werkzeugradius, Werkzeugrundlauf und Werkzeugverschleiß werden bei der Schnittkraft berücksichtigt, und Experimente haben bestätigt, dass das Modell genauer ist als das herkömmliche Schaftfräsmodell.
Vogler et al. schlug ein mechanisches Modell für das Mikroendfräsen vor, Berücksichtigung unterschiedlicher Phasen in heterogenen Materialien. Es wurde festgestellt, dass die Mehrphasenigkeit im Metallmaterial die hochfrequente Änderung der Schnittkraft verursacht, Dies erklärt das Hochfrequenzsignal, das in der Schnittkraft auftritt, wenn das mehrphasige Material mikrogemahlen wird.
Derzeit, Es gibt nicht viel Forschung zur Mikrofräskraft, und es ist notwendig, die Eigenschaften der Mikroschneidkraft besser zu verstehen. Und es kann durch Echtzeitüberwachung der Schnittkraft in Betracht gezogen werden, die Schnittmenge dynamisch anzupassen, um die Schnittkraft zu steuern, verbessern die Qualität der bearbeiteten Oberfläche, und verlängern die Lebensdauer des Werkzeugs.
Bei Verwendung eines Schaftfräsers mit kleinem Durchmesser für die Mikrobearbeitung, Es ist sehr schwierig, die bearbeitete Oberfläche nach dem Schneiden zu beschneiden, Daher besteht die Hoffnung, dass der Endbearbeitungsprozess mit einem Fräser abgeschlossen werden kann. Darüber hinaus, Die Schnittzeit für die hochpräzise Formbearbeitung beträgt oft mehrere Stunden, Daher werden höhere Anforderungen an die Standzeit und Schnittleistung gestellt.
Rahman et al. führte Mikrofräsexperimente an reinem Kupfer mit einem Schaftfräser mit einem Durchmesser von durch 1 mm. Verwendung der Antwortflächenmethode in der Statistik, Es wurde ein quadratisches Modell der Werkzeuglebensdauer beim Mikrofräsen von reinem Kupfer erstellt. Daraus lässt sich schließen, dass die Schnittgeschwindigkeit und das Ausmaß des Rückgriffs einen erheblichen Einfluss auf die Standzeit des Werkzeugs haben, während die Vorschubgeschwindigkeit keinen wesentlichen Einfluss hat. Die Schneide zeigt nach dem Abstumpfen einen Anstieg der Schnittkraft. Gleichzeitig, Der Durchmesser und die Schneidengröße des Mikrowerkzeugs sollten berücksichtigt werden. Zhou et al.. Ich habe einen Schaftfräser mit einem Durchmesser von verwendet 2 mm, um Graphitelektroden mit hoher Geschwindigkeit zu fräsen. Es wird darauf hingewiesen, dass der Werkzeugverschleiß durch abrasiven Verschleiß dominiert wird, und die Verschleißmuster sind Flankenverschleiß, Verschleiß der Rechenfläche, Mikrorisse und Brüche. Die Chipformen sind klumpig, säulenförmig, kugelförmig und flockenförmig; Die Lebensdauer des beschichteten Werkzeugs beträgt 1.5 mal so hoch wie beim unbeschichteten Werkzeug; Es wird vorgeschlagen, dass der Einsatz einer Luftstrahldüse und eines Staubsaugers den Verschleiß und die Beschädigung des Werkzeugs wirksam reduzieren kann. Miyaguchi et al. wies darauf hin, dass die Werkzeuglebensdauer durch eine Verringerung der Werkzeugsteifigkeit verlängert werden kann. Aufgrund der geringen Steifigkeit des Werkzeugs, Durch die Biegung des Werkzeugs wird die Schnittkraft ausgeglichen und der Einfluss des Rundlauffehlers ausgeglichen, Dies führt zu einem gleichmäßigen Verschleiß der beiden Schneiden.
Im Mikrofräsprozess von Mikrowerkzeugen, the chip state is an important factor to realize precision machining, control the machining process, and judge the machining ability. Kim et al. conducted an experimental study on chip formation during micro-milling. Milling grooves on brass workpieces with different feed rates, measuring by collecting chips and observing the SEM image of the bottom surface of the groove. When the feed per tooth is less than the blunt radius of the cutting edge, the actual CNC chip volume is several times the nominal chip volume, and the interval of the feed marks is also greater than the feed per tooth. As the feed per tooth increases, the actual chip volume gradually approaches the nominal chip volume. It can be seen that in micro-milling, chips are not always formed during the feed with a small feed per tooth, das ist, Die Bildung von CNC-Spänen erfolgt sporadisch und sporadisch.
Um die Qualität der Mikrofräsbearbeitung zu verbessern, Der Verschleiß und die Lebensdauer des Werkzeugs müssen untersucht werden. Es kann in Betracht gezogen werden, den Verschleiß und Bruch des Werkzeugs durch die Schnittkraft zu untersuchen, Oberflächenrauheit, und Werkzeugvibrationen.