What is an eccentric shaft?
CNC-Bearbeitung von Exzenterwelle bzw. Exzenterscheibe und Exzenterhülse
Die Achsen des Außenkreises und des Außenkreises sind parallel, aber die Werkstücke, die sich nicht überlappen, werden Exzenterwellen genannt. Die Exzenterwelle ist im Allgemeinen durch ein Exzenterloch an der rotierenden Welle des Motors befestigt. Wenn der Motor gestartet wird, Führen Sie eine Nockenbewegung durch. daher, Es wird häufig in Automobilen verwendet, Motoren, Pumps, usw.
CNC machining of eccentric workpieces
An eccentric workpiece is a workpiece whose outer circle and outer circle or the axis of the outer circle and the inner hole are parallel and not coincident, and offset a certain distance. The distance between these two parallel axes is called the eccentricity. The outer circle and outer circle eccentric parts are called eccentric shaft or eccentric disc; Parts with eccentric outer circle and inner hole are called eccentric sleeve
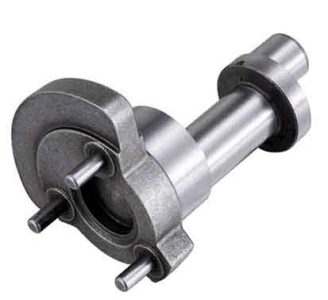
Eccentric crankshaft machining of motorcycle
Machining of eccentric shaft
The processing of eccentric parts is a difficult point in mechanical processing. For the processing of large parts such as eccentric bearings and cams, three-jaw and four-jaw chucks are commonly used for processing on ordinary machine tools. With the continuous development of science and technology, the demand for eccentric parts is increasing, and the accuracy is getting higher and higher. daher, the demand for this type of eccentric fixture has also increased correspondingly, and its application prospects are broad. Eccentric shaft parts are one of the common and typical turning parts. According to the different structure of eccentric shaft parts: Generally can be divided into: optical axis eccentricity, stepped shaft eccentricity and special-shaped eccentric shaft, usw.; Or solid eccentric shaft, hollow eccentric shaft, usw. They are also used to support transmission parts such as gears and pulleys in the machine to transmit torque or movement.
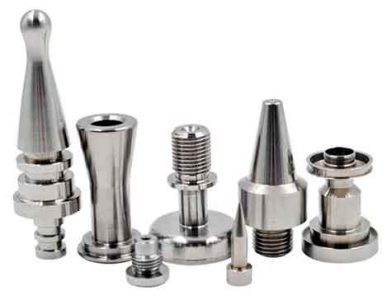
CNC-Bearbeitung eines Exzenterrades aus Edelstahl
Method of machining eccentric shaft
Turning eccentric shafts mainly take measures in terms of clamping, to align the axis of the eccentric part to be processed and coincide with the axis of the main shaft of the lathe.
1. Turning an eccentric workpiece on a 4-jaw single-action chuck
Turning For eccentric workpieces with a small number of machining and low precision, the four-jaw chuck is generally used for clamping. When turning an eccentric workpiece on a four-jaw chuck, you must first mark the workpiece. It is to draw an eccentric circle and a cross line to ensure the horizontal and vertical directions. In order to determine its position in the four-jaw chuck based on these lines.
2. Machining eccentric workpieces on a 3-jaw self-centering chuck
When the machining eccentricity is small (e≤5-6mm), the length is short, and the number of eccentric workpieces is large. It can be processed by the three-jaw self-centering chuck. Beim Wenden, the outer circle and length are turned first. Then it is clamped on a three-jaw chuck, and a shim is placed on one of the jaws to make the workpiece eccentric for turning. The thickness of the pad can be calculated by the following formula. X=1.5e×(1-e/2d) (X = gasket thickness; e = the eccentricity of the workpiece; d = the diameter of the gripping part of the three jaws). In actual turning, due to the deviation of the contact position between the long claw and the workpiece, a correction constant needs to be added to the deformation after the shim is clamped. x real = x+1.5△e (x real = actual gasket thickness; x = calculated thickness; △e = The measured eccentricity error after the test)
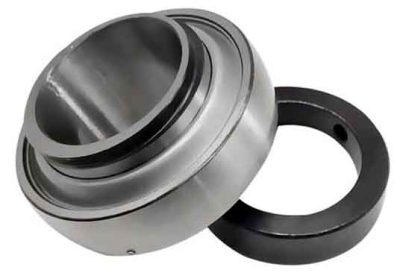
Outer spherical bearing with eccentric sleeve
3. Turning the eccentric shaft workpiece on the double chuck
This method is to clamp the 3-jaw self-centering chuck on the 4-jaw single-action chuck for alignment. After moving an eccentric distance, it is clamped, and the eccentric turning can be done by clamping the workpiece on the three-jaw self-centering chuck. This eliminates the need to correct the workpiece. When moving the position of the 3-jaw chuck, first clamp the optical axis in the 3-jaw self-centering chuck, and use a dial indicator to determine the eccentricity. Finally confirm the position of the 3-jaw chuck in the 4-jaw chuck.
4. Turning eccentric shaft workpiece between two thimble
The longer eccentric shaft workpiece can be clamped between two thimble for turning, and the chicken core clamp is used to drive the workpiece to rotate. The center of the two ends of the eccentric shaft workpiece processed between two thimbles, and the eccentric center hole is generally processed on a boring machine. Because it is difficult to ensure that the eccentric shaft at both ends of the eccentric shaft and the direction of the eccentric hole are consistent and parallel on a lathe.
5. Load the eccentric workpiece on the eccentric chuck
The eccentricity of the eccentric chuck is easy to adjust, has strong versatility and high precision. It is an ideal turning eccentric tool.
6. Turning eccentric workpieces on special fixtures
When the machining length is short, the precision is high, and the number of eccentric workpieces is large, it can be turned on a special fixture.
7.When actually processing eccentric workpieces with large eccentricity and low precision requirements.
Sum up another clamping method, three-jaw boring position plus gasket clamping: When the three-jaw self-centering fixture is used to set the jaws, first move the No. 1 jaw, and then lightly adjust the chuck, so that the end face of the chuck rotates about one or two turns. Then put on the 2 Und 3 jaws to make the 3 jaws of the chuck naturally eccentric. Since this eccentricity is not adjustable, it is necessary to add a gasket to adjust it. The advantage of this method is that it is simple, bequem und schnell, but the disadvantage is that the positioning accuracy is not high.