Die Entwicklung dreidimensionaler Designsoftware bietet günstige Voraussetzungen, kurzzeitig, und Konstruktion von Positioniervorrichtungen. Und es kann CNC-Bearbeitungsteile zur Überprüfung simulieren. Figur 1 zeigt ein typisches Metallteil mit einem Winkel von 45° zur YZ- und ZX-Ebene:
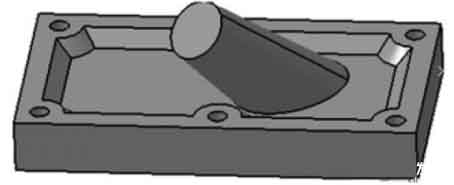
CNC -Bearbeitungsteile mit besonderer Struktur
Figur 1 Auswahl des Plans der Teile CNC -Bearbeitung
Diese Art von Teilen mit besonderer räumlicher Struktur hat im Allgemeinen im Allgemeinen 2 Arten von CNC -Bearbeitungsmethoden:
① Verbessern Sie die Leistung des Werkzeugmaschinens, das ist, Erhöhen 5 Achsen;
② Entwerfen Sie eine geeignete Positionierungsanlage und verwenden Sie vorhandene Geräte zur Verarbeitung.
Berücksichtigung der Verarbeitungskosten, Die zweite Option ist offensichtlich eine idealere Wahl. Das Folgende ist, eine Positionierungsanlage für diesen Teil zu entwerfen, und verwenden Sie Catia -Software, um eine solide Modellierung durchzuführen, Montage, Interferenzerkennung, und Genauigkeitsanalyse der einzelnen Komponenten der Leuchte. Importieren Sie das entworfene Gerät in das CNC -Bearbeitungsmodul für die virtuelle Bearbeitung, um die Machbarkeit und Korrektheit des Designs zu überprüfen.
Design- und 3D -Modellierung der Positionierungsbehandlung
Berücksichtigung der Eigenschaften der verarbeiteten Teile, Gewährleistung der Genauigkeit der Verarbeitung, und um den Anwendungsumfang des Geräts zu verbessern, Die Positionierungsbehandlung ist als modulare kombinierte Gerät ausgelegt, wie in der Abbildung gezeigt 2. Die Vorrichtung besteht hauptsächlich aus 4 Teile: Positionierungshalterung, Positionierungsplatte, Leitmodul und Positionierungsklemme. Die Positionierungshalterung ist der Eckpfeiler der gesamten Leuchte, die direkt die Neigung der Positionierung bestimmt, und andere Teile werden auch darauf installiert.
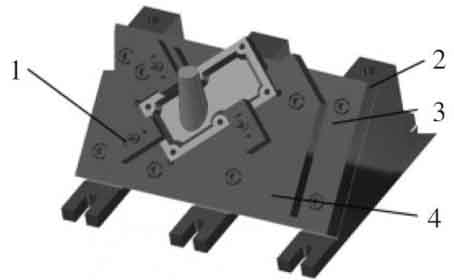
3D solides Modell der Positionierungsvorrichtung
Figur 2 Dreidimensionales festes Modell der Positionierungsbehandlung
1. Positionierung des Clips
2. Positionierungshalterung
3. Positionierungsplatte
4. Leitmodul
Die Positionierungsplatte wird verwendet, um das Führungsmodul an der Positionierungshalterung zu installieren, und wenn die Größe und Form der Grundfläche des Werkstücks mit einer Neigung von 45 ° verarbeitet werden soll, Nur die Struktur und Größe des Führungsmoduls müssen geändert werden. Wenn Sie eine geeignete Position auf der Positionierungsplatte zum Befestigen auswählen. Das Design des Führungsmoduls und die Positionierungsklemme sollten auf der Struktur und Form des verarbeiteten Teils basieren, so dass es der äußeren Oberfläche des zu verarbeitenden Teils entspricht, und die Höhe sollte gleich sein, um die Installation der Positionierungsklemme zu erleichtern. Die Positionierungsklemme ist im Allgemeinen mit Dreipunktpositionierung ausgelegt und installiert, und kooperiert mit der Positionierungsplatte, um die Einschränkung von zu realisieren 6 Grad der Freiheit der zu verarbeitenden Teile.
Statische Interferenzinspektion der Positionierungsbehandlung
Um sicherzustellen, dass die Komponenten des entworfenen Geräts verarbeitet und zusammengestellt werden können, und kann seine Positionierungsfunktion erreichen, Die Interferenzerkennung muss an der Leuchte durchgeführt werden.
Die statische Interferenzanalyse umfasst die Interferenz zwischen den Geräteeinheiten und der Interferenz zwischen der Gerät und dem Werkstück. Jedes Gerät besteht aus mehreren Einheiten, und die Fertigstellung beinhaltet die Positionierung und Klemmung. Aufgrund des begrenzten Raums und der komplexen Struktur jeder Einheit, und das Design der Gerät wird im Allgemeinen Schicht für Schicht entworfen, Es ist schwierig, den Rand des Raums zu kontrollieren und leicht zu stören. Zusätzlich, Die Form des Werkstücks ist komplex, und das Werkstück darf aufgrund der Position oder Struktur der Geräteeinheit möglicherweise nicht korrekt installiert werden.
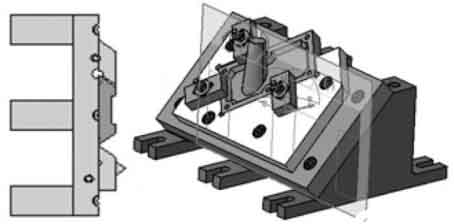
Dynamische Kollisionserkennung von Geräten
Figur 3 Schematisches Diagramm der statischen Interferenzerkennung
Unter dem “Dmuspaceanalyse” Modul in Catia, Führen Sie eine statische Interferenzanalyse auf dem Spiel durch, und verwenden Sie die Kollisionserkennung “Checkclash” und das Abschnittstool “Abschnittdefinition” die Leuchte erkennen.
Dynamische Interferenzanalyse
Verwenden Sie das “Dumfitting” Modul von Catia zur Inspektion der zusammengestellten Produkte bereitgestellt. Es kann den Übertragungsweg der Teile während der Montage aufzeichnen, Analysieren Sie den dynamischen Raum, der durch Bewegung von Teilen beim Zusammenbau von Teilen benötigt wird, und die Störung zwischen Teilen erkennen. Zuerst schalten Sie die “Montagedesign” zu dem “Dumfitting” Modul, und geben Sie jedem Montageweg gemäß der Gerätebaugruppe, Dies enthält die Übertragungsentfernungsinformationen jeder Komponente. Ziel ist es, die spezifische Interferenzposition und Tiefe bei der Einführung der Interferenz zu erhalten, Stellen Sie dann die Montagesimulation in der Reihenfolge fest, und schließlich die öffnen “Kollision” Analyse. Das Analyseergebnis ist in Abbildung dargestellt 4.
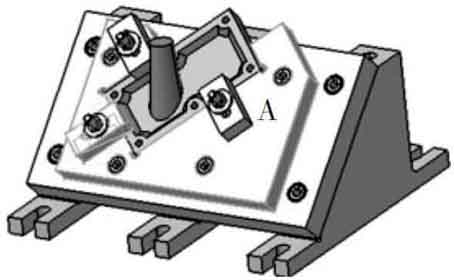
Schematisches Diagramm der statischen Interferenzerkennung von Fixture
Figur 4 Dynamische Kollisionserkennung
Bereich A in Abbildung gezeigt 4 ist der Ort, an dem Störungen auftreten, und seine spezifische Anzeige ist in Abbildung dargestellt 5. Zwischen der Positionierungsklemme und dem Führungsmodul tritt eine Störung auf. Durch die Analyse der Interferenzinformationen, Es wird der Schluss gezogen, dass der Positionierungsclip während des Montageprozesses mit dem Montagepfad des Führungsmoduls kollidiert. Für Störungen erscheint, Nehmen Sie die folgenden Änderungen an der Fixture vor: Unter der Prämisse, den Positionierungspunkt und den Klemmpunkt unverändert zu halten, Ändern Sie die räumliche Position oder einige Größenparameter anderer Teile in der Einheit.
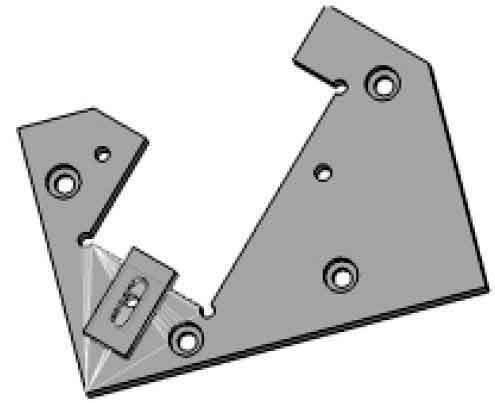
Die Erkennungsstörungsfläche des Geräts
Figur 5, Der Bereich, in dem Störungen auftreten
CNC -Simulationsverarbeitung
Verwenden Sie das “Verarbeitung” Modul von Catia zur Durchführung von CNC -Bearbeitung auf dem Werkstück, um zu überprüfen, ob das Werkzeug bei der Verarbeitung des Werkstücks mit dem Gerät kollidiert, um die Machbarkeit der CNC -Bearbeitung zu überprüfen. Um zu beobachten, ob die Kollision intuitiv auftritt, In diesem Artikel verarbeitet die äußere Kontur des Entwurfszylinders mit räumlicher Neigung im Werkstück. Erste, Schalten Sie das zusammengestellte Gerät auf “Oberflächenbearbeitung” unter dem “Bearbeitung” Modul zur Durchführung “Kontur getrieben” (Contour Driven Finishing) auf der äußeren Oberfläche des bearbeiteten Teils;
Wählen Sie dann den Bearbeitungsbereich als Teil im Popup-Dialogfeld aus, und wählen Sie die entsprechenden Werkzeugpfadparameter aus, einschließlich der Auswahl der Fahranleitungslinie, Die entsprechenden Werkzeugparameter und die Tool -Ausgangsroute;
Endlich, Die CNC -Simulationsverarbeitung wird durchgeführt, um die Werkzeugpfadlinie zu generieren, wie in der Abbildung gezeigt 6.
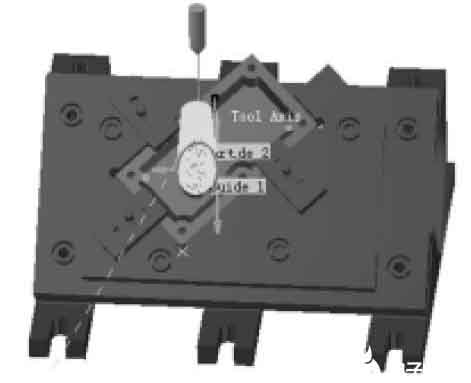
Werkzeugpfadlinien, die von CNC -Bearbeitungsteilen erzeugt werden
Figur 6, die erzeugte Werkzeugpfadlinie
Gesamtpositionierungsfehler der Einrichtung:
(Wobei ΔK = Prozessgrößentoleranz des Werkstücks)
Die oben genannten Fälle können die Kosten effektiv reduzieren und den Design- und Produktionszyklus durch die Verwendung der dreidimensionalen virtuellen Konstruktionsfunktionen von Catia verkürzen, Das Design und die Funktionstests von Positionierungsbehörden; In der gesamten Designkomposition, Der Computer vervollständigt den Vorgang von der Konstruktion über die Montage bis zur Simulationsverarbeitung auf CNC -Werkzeugmaschinen, einschließlich statischer und dynamischer Interferenzanalyse. Dies ist von traditionellen Designmethoden unübertroffen, und es ist auch ein unvermeidlicher Trend in der Entwicklung der modernen Spielindustrie.