For machined parts, our commonly used surface treatment methods are mechanical polishing (sandblæsning, polering), chemical treatment (galvanisering, electrophoresis, chemical oxidation), surface heat treatment, spraying surface, and surface screen printing. Surface treatment is to clean, sweep, deburr, degrease, and deoxidize the surface of the workpiece.
The surface treatment of metal parts is a process of artificially forming a surface layer on the surface of the base material that is different from the mechanical, physical and chemical properties of the base.
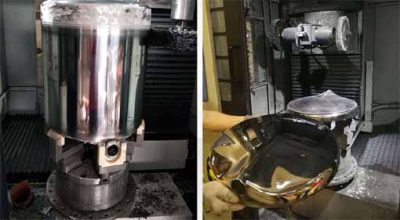
CNC polishing of metal parts
Mekanisk overfladebehandling af dele
Det omfatter hovedsageligt stålbørsterulle-poleringsmetode og shot-peening-metode. Poleringsmetoden er, at børstevalsen drives af motoren, og børstevalsen roterer med høj hastighed på strimlens øvre og nedre overflade i modsat retning af rullestykkets bevægelse for at fjerne oxidskalaen. Den børstede jernoxidskala vaskes væk med et lukket cirkulerende kølevandsvaskesystem.
Shot blasting is a method of using centrifugal force to accelerate the projectile and project it to the workpiece for rust removal and cleaning. Imidlertid, shot blasting has poor flexibility and is limited by the site. It is a little blind when cleaning the workpiece, and it is easy to produce dead corners on the inner surface of the workpiece that cannot be cleaned. The structure of the equipment is complex, there are many wearing parts, especially the blades and other parts wear quickly, the maintenance man-hours are many, the cost is high, and the one-time investment is large.
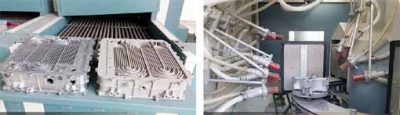
Surface sandblasting of machined parts
Electrochemical surface treatment of parts
This method uses electrode reaction to form a coating on the surface of the workpiece. The main methods are:
(1) Galvanisering
In the electrolyte solution, the workpiece is the cathode. The process of forming a coating on the surface under the action of an external current is called electroplating. The plating layer can be metal, legering, semiconductor or containing various solid particles, such as copper plating, nickel plating, etc.
(2) Anodizing
In the electrolyte solution, the workpiece is the anode. The process of forming an oxide film on the surface under the action of external current is called anodization, such as the anodization of aluminum alloy.
The oxidation treatment of steel can be done by chemical or electrochemical methods. The chemical method is to put the workpiece in an oxidizing solution, and rely on chemical action to form an oxide film on the surface of the workpiece, such as bluing of steel.
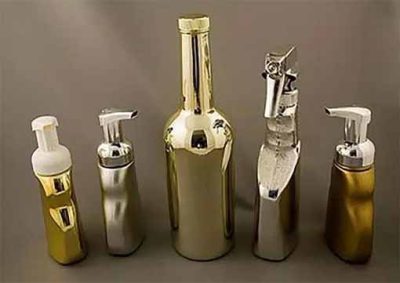
Pletteringsbehandling af dele
Chemical surface treatment of parts
This method has no current action, and uses the interaction of chemical substances to form a plating layer on the surface of the workpiece. The main methods are:
(1) Chemical conversion membrane treatment
In the electrolyte solution, the metal workpiece has no external current action, and the chemical substance in the solution interacts with the workpiece to form a coating on its surface, which is called chemical conversion film treatment. Such as bluing, fosfatering, passivering, and chromium salt treatment on the metal surface.
(2) Electroless plating
In the electrolyte solution, the surface of the workpiece is catalytically treated, and there is no external current effect. Due to the reduction of chemical substances in the solution, the process of depositing certain substances on the surface of the workpiece to form a coating is called electroless plating, such as electroless nickel plating and electroless copper plating.
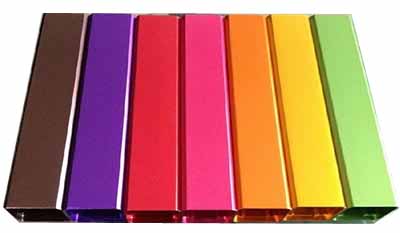
Anodizing of aluminum alloy
Thermal processing surface treatment of parts
This method is to melt or thermally diffuse the material under high temperature conditions to form a coating on the surface of the workpiece. The main methods are:
(1) Hot dip plating
The process of putting a metal workpiece into molten metal to form a coating on its surface is called hot dip plating. Such as hot-dip galvanizing, hot-dip aluminum and so on.
(2) Thermal spraying
The process of atomizing the molten metal and spraying it on the surface of the workpiece to form a coating is called thermal spraying. Such as thermal spraying zinc, thermal spraying aluminum and so on.
(3) Hot stamping
The process of heating and pressing the metal foil to cover the surface of the workpiece to form a coating layer is called hot stamping. Such as hot stamping aluminum foil and so on.
(4) Chemical heat treatment
The process in which the workpiece is in contact with chemical substances and heated, and a certain element enters the surface of the workpiece at a high temperature is called chemical heat treatment. Such as nitriding, karburering, etc.
(5) Surfacing welding
By welding, the process of depositing the deposited metal on the surface of the workpiece to form a welding layer is called surfacing. Such as surfacing welding wear-resistant alloys.
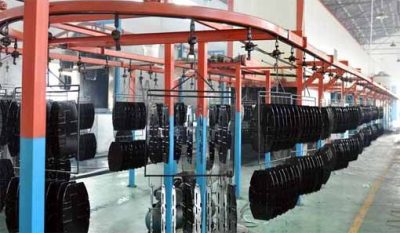
Electrophoresis and electrostatic spraying equipment
Vacuum surface treatment of parts
This method is a process in which materials are vaporized or ionized and deposited on the surface of the workpiece in a high vacuum state to form a coating. The main method is.
(1) Physical vapor deposition (PVD)
Under vacuum conditions, the process of vaporizing metal into atoms or molecules, or ionizing them into ions, which are directly deposited on the surface of the workpiece to form a coating. It is called physical vapor deposition, and the deposited particle beam comes from non-chemical factors. Such as evaporation plating, sputtering plating, ion plating, etc.
(2) Ion implantation
The process of implanting different ions into the surface of the workpiece under high voltage to modify its surface is called ion implantation. Such as boron injection and so on.
(3) Chemical Vapor Deposition (CVD)
The process in which gaseous substances form a solid deposition layer on the surface of the workpiece due to chemical reactions under low pressure (sometimes also at normal pressure) is called chemical vapor plating. Such as vapor deposition of silicon oxide, silicon nitride and so on.
Electrophoresis and electrostatic spraying
- Electrophoresis
As an electrode, the workpiece is put into the conductive water-soluble or water-emulsified paint, and forms a circuit with the other electrode in the paint. Under the action of the electric field, the coating solution has been dissociated into charged resin ions, the cations move to the cathode, and the anions move to the anode. These charged resin ions, together with the adsorbed pigment particles, are electrophoresed to the surface of the workpiece to form a coating. This process is called electrophoresis.
2. Electrostatic spraying
Under the action of a DC high-voltage electric field, the atomized negatively charged paint particles are directed to fly onto the positively-charged workpiece to obtain a paint film, which is called static spraying.