Cutting is roughly divided into turning, fræsning, and center-tooth-based cutting (end face cutting of drills and end mills, etc.). The cutting heat of these cutting processes has different effects on the cutting edge. Turning is a continuous cutting, the cutting force on the tip does not change significantly, and the cutting heat continuously acts on the cutting edge; Milling is a kind of intermittent cutting, and the milling force is intermittently acting on the tip of the blade, and vibration will occur during milling. The heat effect on the cutting edge is the heating during cutting and the cooling during non-cutting alternately, and the total amount of heat received is less than during turning.
The cutting heat during milling is a kind of intermittent heating phenomenon, and the cutter teeth are cooled when they are not cutting, which will help to extend the life of the tool. The Japanese Institute of Physics and Chemistry conducted a comparative test on the tool life of turning and milling. The tool used for milling is a ball end mill, and the turning tool is a general turning tool. The two are in the same machining material and cutting conditions (due to different cutting methods, the cutting depth, feed rate, skærehastighed, etc. can only be roughly the same) and the same environmental conditions for cutting comparison tests. The results show that milling is more beneficial to prolong tool life.
When cutting with tools such as drills and ball end mills with a center edge (det er, the cutting speed = 0m/min), the tool life near the center edge is often reduced, but it is still better than turning.
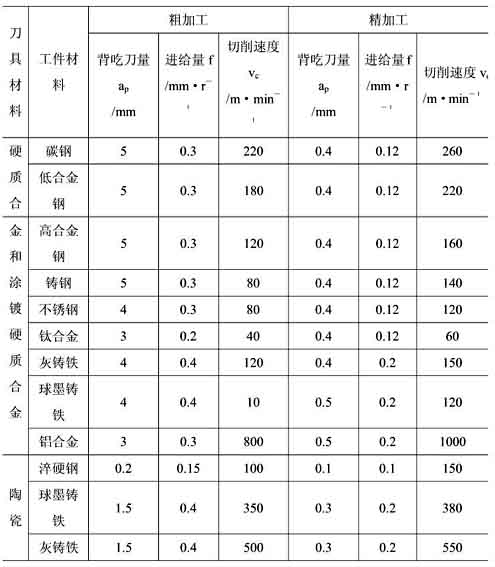
Choose different tools when CNC machining difficult-to-machine materials
When cutting difficult-to-machine materials, the cutting edge is greatly affected by heat, which often reduces tool life. If the cutting method is milling, the tool life will be relatively longer. Imidlertid, difficult-to-machine materials cannot be milled from beginning to end. There will always be times when turning or drilling is needed. Derfor, corresponding technical measures should be taken for different cutting methods to improve processing efficiency
When cutting difficult-to-machine materials, the optimization of the tool shape can give full play to the performance of the tool material. Choosing the tool geometry such as the rake angle, the relief angle, and the entry angle that are compatible with the characteristics of difficult-to-machine materials and the proper treatment of the cutting edge will have a great impact on the improvement of cutting accuracy and the extension of tool life. Derfor, the shape of the tool must not be taken lightly. Imidlertid, with the popularization and application of high-speed milling technology, recently, small depth of cut has been gradually adopted to reduce the load of cutter teeth, and up-cut milling has been adopted and the feed rate has been increased. Derfor, the design idea of the cutting edge shape has also changed.
When drilling difficult-to-machine materials, increasing the drill tip angle and performing cross-shaped grinding is an effective way to reduce torque and cutting heat. It can control the contact area between the cutting and the cutting surface within the minimum range, which is very beneficial to prolong tool life and improve cutting conditions. When the drill is drilling, the cutting heat is easily trapped near the cutting edge, and chip removal is also very difficult. When cutting difficult-to-machine materials, these problems are more prominent, and sufficient attention must be given.
For at lette fjernelse af spåner, there is usually a coolant spray outlet on the back side of the cutting edge of the drill, which can supply sufficient water-soluble coolant or mist coolant. Make chip removal more smooth, this method is also ideal for the cooling effect of the cutting edge. I de seneste år, some coating materials with good lubricating properties have been developed. After these materials are coated on the surface of the drill bit, dry drilling can be used when processing 3 to 5D shallow holes with them.
Hole finishing uses boring, but recently it has gradually changed from a traditional continuous cutting method to an interrupted cutting method such as contour cutting. This method is more beneficial to improve chip removal performance and extend tool life. Derfor, after the boring tool for discontinuous cutting was designed, it was immediately applied to CNC cutting of automotive parts. In terms of threaded hole processing, spiral cutting interpolation is also currently used, and end mills for thread cutting have been put on the market in large numbers.
As mentioned above, this conversion from the original continuous cutting to the discontinuous cutting is carried out with the deepening of the understanding of CNC cutting, which is a gradual process. When this cutting method is used to cut difficult-to-machine materials, the smoothness of the cutting can be maintained, and it is beneficial to extend the life of the tool.