The use of short cutting tools is the main feature of five-axis machining. Short tools will significantly reduce tool deviation, thereby obtaining a good surface quality, avoiding rework, reducing the amount of welding rod used, and shortening the processing time of EDM. When considering five-axis machining, the goals of using five-axis machining molds must be considered:
Use the shortest cutting tool possible to complete the processing of the entire workpiece. It also includes reducing programming, clamping and processing time but can get a more perfect surface quality.
As long as the workpiece cavity is not very deep (relative to the tool diameter), a three-axis tool path (2, 3, 5) is sufficient. If the workpiece cavity is very deep and has very narrow parts, it is not enough to use a pure three-axis tool path to complete the entire finishing. I dette tilfælde, poor surface quality and long processing time ensue. Figur 1 is the case of a three-axis tool path. Here, the shortest tool must be very long in order to be able to machine all areas of the workpiece in the vertical direction.
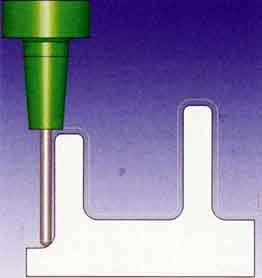
3-axis machining path of short tool
Figur 1, Three-axis machining path
When using a shorter tool, the spindle should be tilted to ensure that the special area of the workpiece can be processed. 3+2 axis machining is usually considered as setting a constant angle to the spindle. Complex workpieces may require many oblique views to cover the entire workpiece, but this will cause tool paths to overlap and increase machining time.
Ud over, all the oblique views are difficult to accurately combine, so the workload of manual polishing will increase, og på samme tid, it will greatly increase the movement in and out, which often leads to surface quality problems and more tool movement.
Figur 2, 3+2 axis tool pathFinally, programming in this way will interfere with each other and is time-consuming, and the sum of all views often cannot cover the entire geometry. Figur 2 demonstrates four workpiece views, but there is still an area in the center of the workpiece that cannot be covered. This area still needs an additional oblique view.
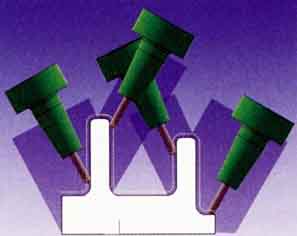
3+2 axis short tool machining path
Figur 3, 5-axis tool path
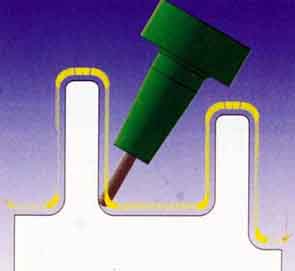
5-axis short tool machining path
For at overvinde manglerne ved 3+2 aksebearbejdning, fem-akset samtidig bearbejdning kan være et bedre valg, for ikke at nævne, at nogle fem-aksede værktøjsmaskiner også har nogle funktioner, der er specielt designet til formindustrien. Fem-akset forbindelsesbearbejdning kan koordinere tre lineære akser og to roterende akser for at få dem til at bevæge sig på samme tid, som løser alle problemerne med 3-akse og 3+2 aksebearbejdning. Værktøjet kan være meget kort, der er ingen overlapning af synspunkter, muligheden for at gå glip af forarbejdningsområdet er mindre, og behandlingen kan udføres kontinuerligt uden yderligere import og eksport (se figur 3).