Machining of parts. 2.5-axis and 3-axis and 5-axis milling machining strategies
- The machining of parts – Introduktion
2. Machining of parts with the 3-axis milling strategy
3. Machining of parts with the 5-axis milling strategy
4. Conclusion: Differences between cutting strategy in 2.5 og 3 akser
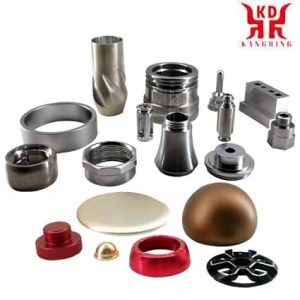
Design CNC Machining Parts Strategy
Machining Parts – Introduktion
Programming the machining of parts at the machine and making modifications by writing code directly on the CNC control is very common. Imidlertid, depending on the type of machine, the complexity of the part, the experience of the operator and the time they have to program, delays in the delivery of orders can be caused, quality controls not passed, or even that a full run of parts has to be re-manufactured.
To avoid the aforementioned, it is important that the operator, prior to executing the CNC program, analyze which operations are necessary to manufacture each part, and once they are clear, it will be possible to decide which milling strategies will be the best fit. .
This entire process, which takes a substantial amount of time, can be considerably reduced with the support of using a CAM program, also known as a machining program, which contributes to meeting the established production times and the required qualities, notably reducing the error range.
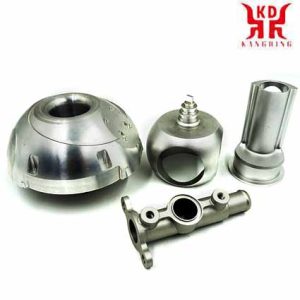
5-axis CNC machining
Machining of parts with the 2.5-axis milling strategy
2.5-axis machining operations are a set of procedures that can be applied in 2.5-axis and 3-axis machining centers (commonly known as milling machines), to manufacture parts of different materials. moving the tool in the X and Y coordinates at the same time during material cutting or chip removal.
In 2.5-axis cut machining, the tool can move in a maximum of 3 machine axes (XYZ), but it will never move in all three coordinates at the same time during the cutting path.
In the two images shown below (fig. 1). the cutting paths (represented by solid light blue lines) are always contained in planes parallel to the XY (plane of the base), so it is a 2.5-axis machining.
2.5-axis milling strategies are used primarily when geometry is simple and to roughly cut large amounts of material evenly. They are also used for 2.5 axis wall finishes when a very fine surface finish is not needed.
This cutting strategy for 2.5 axis milling machines can be found in some CAM programs. such as Solid Edge CAM Pro, and these operations for machining are found within the machining template “mil_planar” and in the first 7 for “mill_contour” (fig.2). The most common 2.5-axis machining operations are:

2.5-axis and 3-axis CNC machining comparison
Floor and wall milling.
Face milling.
Planar milling.
Cavity milling.
Wall milling in Z.
Machining of parts with the 3-axis milling strategy
Continuous 3-axis machining operations allow you to take full advantage of the control of the milling machine, controlling all three axes at the same time on milling paths.
In the two images shown below (figur 3), it can be seen how the cutting paths are not contained in any plane parallel to the XY plane of the base of the machine. These cutting paths “copy” the desired surface to achieve an optimal surface finish with a desirable ridge geometry.
I dette tilfælde. the light blue lines (fig. 3) are not contained in any particular plane, but are adapted at all times to the curvature requirements of the geometry to be machined, without forming cutting levels in the Z coordinate.
Again, this 3-axis milling strategy can be found in the CAM program, Solid Edge CAM Pro, the continuous 3-axis machining operations are located in four groups of the “mill_contour” template:
Contour milling.
Surface milling.
milling flows.
Milling of 3D profiles.
Continuous 3-axis milling operations are commonly called “copied” when machining a specific surface (as in the figure).
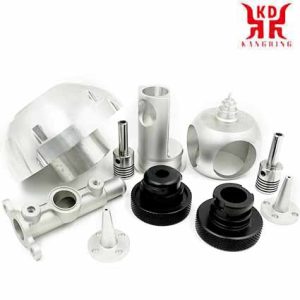
3-axis CNC machining
Conclusion: Differences between milling strategy in 2.5 og 3 akser
Typically, 2.5-axis milling strategies are used for roughing and for fast machining of single parts. They are also used on curved surfaces when surface finish is not critical and some stepping can be allowed on sloped walls.
Continuous 3-axis machining operations are used to give a higher quality in the surface finish, in terms of the type of roughness and ridges.
The decision to use 2.5-axis or 3-axis operations will be based on two factors: the surface finish and the geometric complexity of the part.
When dealing with the machining of a relatively complex part (for example the one shown above) it is advisable to combine the 2.5-axis and 3-axis machining operations. Først, the piece is roughed with 2.5-axis machining and it is finished in 3-axis.
Comparative table between cutting strategies: