Hvorfor er tråddrejning så krævende?
Kravene til gevinddrejning er højere end almindelige drejeoperationer. The cutting force is generally higher, and the cutting end radius of the threaded insert is smaller and weaker.
In thread processing, the feed rate must correspond exactly to the pitch of the thread. For a pitch of 8 threads/inch (tpi), værktøjet skal fremføres med en tilspændingshastighed på 8 omdrejninger/tommer eller 0.125 tommer/omdrejning. Sammenlignet med almindelige drejeapplikationer (hvor den typiske tilførselshastighed er omkring 0,012ipr), tilspændingshastigheden for gevinddrejning er 10 gange højere. Kraften ved spidsen af den gevindskårne bearbejdningsindsats kan være 100 til 1,000 gange højere.
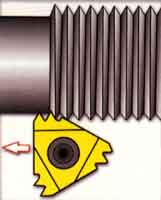
Gevinddrejning med flertands gevindindsats
figur 2: Multi-tand skær, med flere gevindtænder i en serie, trådbehandlingseffektiviteten kan forbedres, men skærekraften er højere.
Enderadius, der bærer denne kraft, er generelt 0.015 tommer, mens radius af et konventionelt drejeskær er 0.032 tommer. Til gevindværktøj, radius er strengt begrænset af rodradius af den tilladte trådform (dens størrelse er specificeret af den relevante gevindstandard). Den er også begrænset af den nødvendige skærehandling, because the material cannot withstand the cutting process in ordinary turning, otherwise thread deformation will occur.
The result of higher cutting force and narrower force concentration range is: Thread machining inserts bear much higher stress than general turning tools.
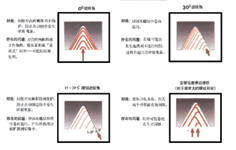
Turning thread with cross-cut feeding method
Comparison of partial and full profile blades
Partial profile inserts, sometimes referred to as “non-topped” inserts, cut thread grooves without cresting or cresting the thread. (See Figure 1) A tool can produce a series of threads, up to the thickest pitch-that is, the smallest number of threads per inch-which is permitted by the strength of the blade end radius.
The end radius is designed to be small enough that the blade can process various pitches. For small pitch threads, the end radius will appear to be too small. This means that the blade must penetrate deeper when machining. For eksempel, machining an 8 tpi thread with a partial profile insert requires a thread depth of 0.108 tommer. The same thread produced with a full profile blade requires only a specified depth of 0.81 tommer. Derfor, the full profile insert can produce a stronger thread. Ud over, the operation of machining threads with full profile inserts can be done in 4 less steps.
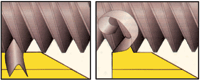
Thread cutting by flank transverse cutting method
Multi-tooth blade
The multi-tooth blade has a series of teeth continuously, and the cutting depth of any tooth in the thread groove is deeper than the previous tooth. (See Figure 2) With these inserts, the number of operations required to machine a thread can be reduced by 80%. The tool life is much longer than single-center inserts, because the final tooth only processes half or one-third of the metal of a given thread.
Imidlertid, due to their high cutting force, it is not recommended to use these inserts for the processing of thin-walled parts-because chatter may occur. Ud over, the structure for machining workpieces with these inserts must have sufficient thread clearance so that all teeth can exit cutting.
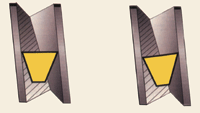
Turning thread by adjusting blade helix angle
Figur 3: The choice of cross-cutting feed method has a great influence on thread processing efficiency
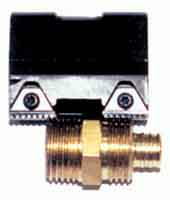
Custom thread cutting tool for milling threads
Figur 4: Flank transverse cutting does not produce V-shaped chips, but produces chips similar to those in ordinary turning.
Feed per thread
The cutting depth of each pass, or the feed of each thread, is very critical in thread processing. Each connected operating channel must engage the larger part of the cutting edge of the blade. If the feed per pass is constant (this method is not recommended), the cutting force and metal removal rate will increase drastically from the previous pass to the next.
For eksempel, when using a constant feed of .010 tommer / processing speed of a channel 60 ℃ thread shape, the second track material is removed 3 times the first track. As with each subsequent operation, the amount of metal removed continues to rise exponentially.
In order to avoid this increase in the amount of removal and maintain a more realistic cutting force, the thread depth should be reduced with each operation.
Cross-cut thread feed method
There are at least four thread crosscut feeding methods. (See Figure 3) Few people have discovered how much impact one of these methods has on the effectiveness of threading operations.
• Radial thread crosscut feed
•Although this may be the most commonly used method for thread processing, it is indeed the least recommended method. Since the tool is fed radially (perpendicular to the centerline of the workpiece), the metal is removed from both sides of the thread flank, resulting in V-shaped chips. Such chips are difficult to break, so the flow of chips is a problem. Ud over, due to the higher heat and pressure on both sides of the blade end, the tool life is usually shorter than other cross-cutting feed methods.
• thread flank cross feed
In this method, the transverse direction is parallel to one of the flank of the thread, hvilket generelt betyder, at værktøjet fremføres i en lige linje ved 30°C. Spåner ligner dem, der produceres ved almindelig drejning. (See Figure 4.) Sammenlignet med radial tværskæring, de spåner, der produceres ved denne metode, er nemmere at forme og udledes let fra skærkanten, med bedre termisk diffusion. Imidlertid, i denne tværgående fodermetode, bladets bagkant gnider mod tandflanken og skærer ikke. Dette vil brænde trådene, resulterer i dårlig overfladeruhed og jævn skravling.
• Modificeret gevindtandflanke-tværgående skærefremføring (anbefalede)
Denne metode ligner fremføringsmetoden for gevindflankens tværgående skæring, bortset fra at den tværgående skærevinkel er mindre end gevindvinklen - dvs, Mindre end 30 ℃. Denne metode bevarer fordelene ved gevindflankens tværgående skæremetode, samtidig med at man undgår problemerne forårsaget af bladets bagkant. En tværsnitsvinkel på 291/2 ℃ giver generelt de bedste resultater, men i egentlig drift, en tværsnitsvinkel i området 25~291/2 ℃ er acceptabel.
Figur 5: Ved at justere bladets helixvinkel, såsom “tilbøjelig” klinge til højre, frigangsvinklen under bladets for- og bagkant kan afbalanceres, som kan give mere ensartet slid.
• Skiftende gevindflanke, tværgående skærefremføring
Denne metode fremføres skiftevis langs de to flanker af gevindet, så den bruger de to flanker af bladet til at danne gevindet. Denne metode kan garantere en længere værktøjslevetid, fordi begge sider af knivenden bruges. Men det kan også forårsage problemer med spånstrømmen -
Dette problem kan påvirke overfladens ruhed og værktøjets levetid. Denne metode bruges normalt kun til stor tonehøjde og (kejserlig) trapezformede og skrå firkantede tråde.
Udligningsgevindvinkelkompensation
Visse gevindbearbejdningsskær og værktøjsholdersystemer har evnen til nøjagtigt at vippe skæret i skæreretningen ved at ændre helixvinklen. Denne funktion kan producere gevind af højere kvalitet, fordi den forhindrer bladet i at gnide mod flanken af gevindet. Det kan også give længere værktøjslevetid, fordi skærekraften er jævnt fordelt over hele skærekantens længde.
Der er ikke noget skær, der hælder på denne måde- Måden at gøre skæret parallelt med arbejdsemnets midterlinje- En uens frigangsvinkel vil blive dannet under bladets forkant og bagkant. (See Figure 5) Især til tykkere pladser, denne ulighed kan forårsage friktion i tandflanken.
Det justerbare system gør det muligt at vippe vinklen på klingen gennem positioneringen af værktøjspatronen (normalt med shims). Præcis justering vil opnå lignende for- og bagkantvinkler, sikre ensartet udvikling af knivslid.
Figur 6: Dette brugerdefinerede gevindskæreværktøj bruges til at bearbejde to uafhængige gevind på en seks-spindlet drejebænk. I fortiden, tråde blev behandlet én ad gangen. Skæret brugt her var faktisk oprindeligt beregnet til gevindfræsere, men den bruges her som drejeskær
Miniaturisering og specialisering af gevindskæringsskær
Indexable insert-type tools for turning internal threads on holes with a diameter of approximately 0.3 inches are now available on the market.
There are many advantages to machine such small holes into threads by turning. The thread quality to be machined is usually relatively high, the blade structure allows chips to flow out of the hole and rarely damages the thread, and the blade can be indexed, so the tool cost is low.
The grades of cemented carbide used in these applications are generally those that allow processing at lower surface speeds. For internal thread machining in small holes, the limitations of machine tools are generally other problems than low surface speeds.
The technological advances that people have made have expanded the scope of application of thread turning tools, and the turning of internal threads into small holes is one example. Imidlertid, despite the expansion of the scope of application of standard tools, manufacturers still have to encounter specific problems, which creates room for the existence of customized tools. (See Figure 6) The special tool developed in cooperation with the tool supplier is an option that cannot be ignored when searching for the correct threading tool for a specific job.