Specifická pevnost součástí z titanové slitiny je mezi kovovými konstrukčními materiály velmi vysoká. Jeho pevnost je ekvivalentní oceli, but its weight is only 57% z oceli. Navíc, titanium alloy has the characteristics of small specific gravity, high thermal strength, good thermal stability and corrosion resistance, but titanium alloy materials are difficult to cut, turn, and mill, and have low processing efficiency. Proto, how to overcome the difficulty and low efficiency of titanium alloy CNC machining has always been a problem to be solved urgently.
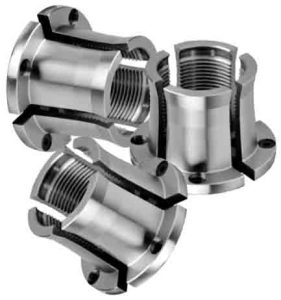
Titanium parts machining characteristics
Reasons for difficult titanium alloy processing
The thermal conductivity of titanium alloy is small, so the cutting temperature is very high when processing titanium alloy. Za stejných podmínek, the cutting temperature of processing TC4 is more than twice that of 45# ocel, and the heat generated during processing is difficult to release through the workpiece;
The specific heat of titanium alloy is small, and the local temperature rises quickly during processing. Proto, the temperature of the tool is very high, the tip of the tool wears sharply, and the service life is reduced.
The low modulus of elasticity of titanium alloy makes the processed surface prone to springback, especially the processing springback of thin-walled parts. It is easy to cause strong friction between the tool surface and the surface of the machined parts, thereby wearing the tool and chipping.
Titanium alloys have strong chemical activity and are easy to interact with oxygen, hydrogen and nitrogen at high temperatures, increasing their strength and decreasing plasticity. The oxygen-rich layer formed during heating and forging makes machining difficult.
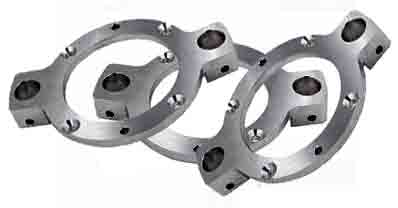
Obrábění titanových lékařských součástí
Principles of cutting titanium alloy materials
Během procesu obrábění, the selected tool material, cutting conditions and cutting time will all affect the efficiency and economy of titanium alloy cutting.
1. Choose reasonable tool materials
In view of the properties, processing methods, and processing technical conditions of titanium alloy materials, reasonable selection of tool materials. The tool material should be more commonly used, lower price, good wear resistance, high thermal hardness, and sufficient toughness.
2. Improve cutting conditions
The rigidity of the machine tool-fixture-tool system is better. The clearance of each part of the machine tool should be adjusted well, and the radial runout of the spindle should be small. The clamping work of the fixture must be firm and rigid enough. Keep the cutting part of the tool as short as possible. In the case of sufficient chip capacity, try to increase the thickness of the cutting edge to increase the strength and rigidity of the tool.
3. Appropriate heat treatment of the processed material
The performance and metallographic structure of titanium alloy materials are changed by heat treatment to achieve the purpose of improving the machinability of materials.
4. Choose a reasonable cutting amount
The cutting speed should be low. Because the cutting speed has a great influence on the temperature of the cutting edge, the higher the cutting speed, the sharp increase in the temperature of the cutting edge. The temperature of the cutting edge directly affects the life of the tool, so choose an appropriate cutting speed.