What is the prototype and its function? How many ways are there to make a prototype?
Prototyping is an essential part of the product development process; however, it has often been a hindrance. Rapid prototyping is a process used to make plastic, kov, or ceramic items. Also known by its name in English as “additive technology Or subtractive technology “, since 3D printing manufacturing process is to add material layer by layer. And CNC machining (turning and milling) is a layer by layer of subtractive technology.
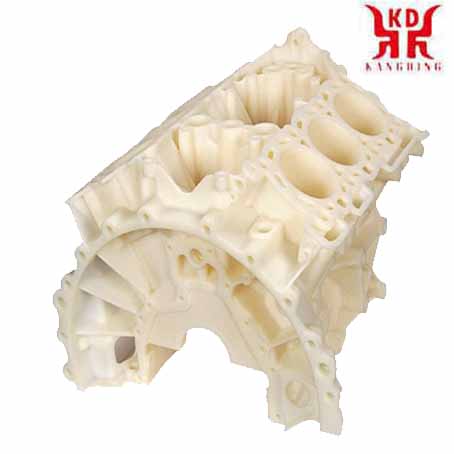
3D printing rapid prototyping
Product designers and engineers created makeshift proof-of-concept models using basic tools, but functional prototyping and quality part creation often required the same processes as final products. Traditional manufacturing processes, such as injection molding, require expensive tooling and setup, which is prohibitively expensive for custom, low-volume prototyping.
In some cases with physical properties that are similar to what would be produced by conventional methods, such as injection molding and extrusion, or blow molding. in this way it is avoided to manufacture expensive molds to make a prototype that could change its shape. Initially, rapid prototyping was only used for prototyping.
Rapid prototyping helps companies turn ideas into realistic proofs of concept. transform these concepts into high-fidelity prototypes that have the same look and feel as the final products and take the products through a series of validation stages to chain production.
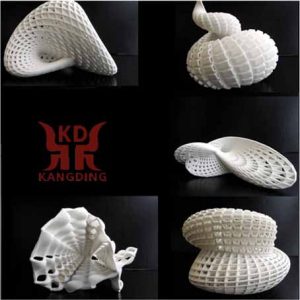
3D printed plastic prototype
With rapid prototyping, designers and engineers can prototype directly from computer-aided design (CAD) data faster than ever before, and carry out fast and frequent reviews of their designs based on actual testing and feedback. .
In this guide, you will discover how rapid prototyping can be integrated into the product development process, what its applications are, and what rapid prototyping tools are currently available to product development teams.
What is rapid prototyping?
Rapid prototyping is the set of techniques used to rapidly fabricate a scale model of a part or a physical set of parts from three-dimensional computer-aided design (CAD) data. Since these parts or assemblies are usually built using additive manufacturing techniques, rather than traditional subtractive methods, the concept has become closely linked to additive manufacturing and 3D printing.
Additive manufacturing is perfect for rapid prototyping. It offers almost unlimited freedom in shape, requires no tooling, and can produce parts with mechanical properties very similar to that of various materials made with traditional manufacturing methods. 3D printing technologies have existed since the 1980s, but in most cases, their high cost and complexity limited their use to large companies or forced smaller companies to outsource production to specialized services and to wait weeks between each iteration.
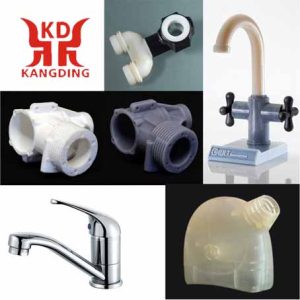
Služba rychlého prototypování v Číně
With 3D printing, engineers and designers can quickly iterate between digital designs and physical prototypes and get to production more quickly.
The arrival of desktop and work 3D printing has changed this situation and fostered an increase in the adoption of this technology that shows no signs of stopping. With on-site 3D printing, engineers and designers can quickly iterate between digital designs and physical prototypes. It is now possible to prototype in one day and perform multiple design, velikost, shape, or assembly iterations based on actual test and analysis results. Ultimately, the rapid prototyping process helps companies get better products to market faster than the competition.
Advantages of rapid prototyping
Make and explore concepts faster
Rapid prototyping turns initial ideas into low-risk concept explorations with the appearance of real products in no time. It enables designers to go beyond virtual visualization and makes it easier to understand what a design looks like and how it feels, as well as to compare concepts.
Communicate your ideas effectively
Physical models give designers the ability to share their concepts with colleagues, clients, and collaborators to convey ideas in ways that are not possible simply by viewing designs on a screen. Rapid prototyping makes it possible to obtain clear and useful information from the user that is essential for creators to understand user needs and to refine and improve their designs.
Design iteratively and incorporate changes instantly
Design is always an iterative process that requires several cycles of testing, evaluation, and refinement before reaching a final product. Rapid prototyping with 3D printing offers the flexibility to create realistic prototypes faster and implement changes immediately, improving this crucial trial and error process.
A good model is a 24-hour design cycle: design during business hours, let the prototype parts be 3D printed overnight and run rehearsals the next day, modify the design, and start over.
Save time and money
With 3D printing, there is no need to invest in expensive tools and installations. The same equipment can be used to produce different geometries. Rapid on-site prototyping eliminates the high costs and lead times associated with outsourcing.
Perform extensive testing and minimize design flaws
In product design and manufacturing, finding and fixing design flaws in advance can help companies avoid costly design reviews and tooling changes throughout the process.
Rapid prototyping enables engineers to thoroughly test parts that look and function the same as final products, reducing the risk of usability or manufacturability issues before moving to production.
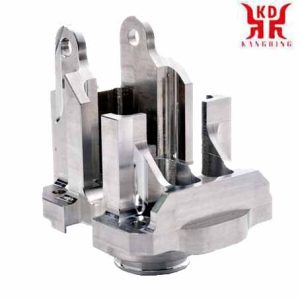
CNC machining rapid prototyping service
Rapid prototyping applications
Thanks to the various technologies and materials available, rapid prototyping supports designers and engineers throughout product development, from initial conceptual models to engineering, validation testing, and production.
Proof of Concept Prototypes and Concept Models
Concept or proof-of-concept model prototypes help product designers to validate ideas and assumptions and to test the feasibility of a product. Physical conceptual models serve to showcase an idea to shareholders, encourage discussion, and influence acceptance or rejection of the idea through low-risk concept explorations.
Proof-of-concept prototyping occurs early in the product development process, and these prototypes present the minimum functionality necessary to validate assumptions before moving the product to the next stages of development.
The key to successful conceptual modeling is speed. Designers need to generate a large number of ideas before building and elaborating physical models. At this stage, usability and quality are less important and teams use commercial parts as much as they can.
3D printers are ideal tools for making conceptual models. Its lead time to convert a computer file to a physical prototype is unbeatable, allowing designers to test more concepts more quickly. Unlike most workshop and fabrication tools, desktop 3D printers are tailored for offices, eliminating the need for dedicated office space.
Functional prototypes
Parallel to the industrial design process, engineering teams work on another series of prototypes to test, iterate, and refine the mechanical, electrical, and thermal systems that make up the product. These functional prototypes may look different than the final product, but have the basic technologies and functions that must be developed and tested.
Many times these basic functions are developed and tested in separate subunits before being integrated into a single product prototype. This subsystem approach isolates variables, making it easier for teams to divide responsibilities and ensure reliability at a more granular level before bundling all items together.
Engineering prototypes
The engineering prototype is where design and engineering come together to create a minimal viable version of the final commercial product, which has a manufacturing-oriented design. These prototypes are used to conduct user trials in the laboratory with a select group of pilot users, to communicate production intent to tooling specialists in the later stages and to serve as a demonstration in early sales meetings.
At this stage, details become increasingly important. 3D printing enables engineers to create high-fidelity prototypes that accurately represent the final product. This makes it easy to verify the design, fit, function and manufacturability of the product before investing in expensive tooling and moving into the production phase where the time and cost of making changes becomes increasingly prohibitive.
Advanced 3D printing materials are capable of reproducing the look, feel and material characteristics of parts created using traditional manufacturing processes such as injection molding. Various materials can simulate parts with precise details and textures, smooth, low-friction, soft-touch surfaces, rigid and robust housings, and transparent components. 3D printed parts can be finished with secondary processes such as sanding, leštění, painting or galvanizing to reproduce any visual features of a final part. They can also be combined to create multi-piece and multi-material assemblies.
Engineering prototypes require extensive usability and functional testing to see how a part or assembly performs under the rigors and conditions of actual use. 3D printing offers engineering plastics that are used to make high-performance prototypes capable of withstanding thermal, chemical, and mechanical stress.
Validation and manufacturing tests
Rapid prototyping enables engineers to create small batches, custom point solutions, and sub-assemblies for design, engineering, and product validation testing projects that test prototype manufacturability.
3D printing makes it easy to test tolerances with the current manufacturing process in mind, and carry out extensive testing both in-house and in the environment of use, before moving to line production.
Rapid 3D printed tooling can also be combined with traditional manufacturing processes, such as injection molding, thermoforming or silicone molding, to improve production processes by improving their flexibility, agility, scalability and cost effectiveness. The technology also provides an efficient solution for creating test fixtures and fixtures as they simplify functional testing and certification by collecting useful data.
With 3D printing, design doesn’t have to end when production begins. Rapid prototyping tools enable designers and engineers to continually improve their products and act quickly and efficiently to resolve problems in the chain with clamping and fixture arrangements that improve assembly or quality control processes.
CAST DEPOSITION MODELING (FDM) | STEREOLITHOGRAPHY (SLA) | SELECTIVE LASER SINTERING (SLS) | CNC TOOLS | |
Print volume | Up to 300 × 300 × 600mm (desktop and work 3D printers) | Up to 300 × 335 × 200mm (desktop and work 3D printers) | Up to 165 × 165 × 300mm (industrial working 3D printers) | Depends on the tool |
Materials | Standard thermoplastics, such as ABS, PLA and their various mixtures. | Varieties of resin (thermosetting plastics). Standard, engineering resins (similar to ABS, polypropylene and silicone; flexible, temperature resistant, rigid), for casting, dental and medical applications (biocompatible). | Engineering thermoplastics, typically nylon and its compounds (Nylon 12 Powder is biocompatible and sterilizable). | Plastics, soft metals, hard metals (industrial machines), wood, akryl, stone, glass, composite materials. |
Applications | Basic proof-of-concept models, low-cost prototyping for simple parts. | Rapid prototypes, high-fidelity aesthetic prototypes, and functional prototypes that require tight tolerances and smooth surfaces. | Complex geometries, functional prototypes and engineering prototypes. | Simple designs, structural parts and metal components. |
Price range | The most affordable printers and 3D printing equipment start at a few hundred dollars. Higher-quality and mid-range desktop printers start at $ 2,000 and industrial systems start at $ 15,000. | Professional printers start at $ 3,500 and large-format job printers start at $ 11,000, while large-scale industrial machines start at $ 80,000. | Industrial work systems can be purchased from $ 18,500 and traditional industrial printers are available from $ 100,000. | Small CNC machines start at around $ 2,000, but professional tools far exceed that number. Basic engraving machines are available for less than $ 500, while mid-range laser cutters start at $ 3,500. Waterjet cutters can be purchased from around $ 20,000. |
CNC obrábění
Počítačové numerické řízení (CNC) tools are subtractive manufacturing processes, unlike FDM, SLA or SLS. These processes begin with solid plastic, kov, or other material blocks, bars, or rods that are shaped by removing material from them through cutting, vrtání, vrtání, and grinding.
CNC tools include CNC machining, which removes material from the part in two ways: with a rotary tool and the fixed part (frézování), or by rotating the part with a fixed tool (otáčení). Laser cutters use a laser to engrave or cut through a wide range of materials with great precision. Waterjet cutters use water mixed with abrasive materials and high pressure to cut through almost any material. CNC lathes and mills can have multiple axes, allowing them to handle more complex designs. Laser and waterjet cutters are best suited for flat parts.
CNC tools can shape parts from plastics, soft metals, hard metals (industrial machines), wood, akryl, stone, glass, composite materials. CNC tools are more complicated to set up and handle than additive manufacturing tools, while some materials and designs may require special tooling, handling, positioning, and processing, making them costly for point parts compared to additive processes.
In rapid prototyping, simple designs, structural parts, metal components, and other parts that are not feasible or cost-effective to produce with additive tools are ideal.