Medical components, especially implants, are one of the fastest growing segments in the processing of small to medium-sized precision Titan components. This is because the proportion of people over 65, who make up the largest share of the market for implants, will almost triple by 2050.
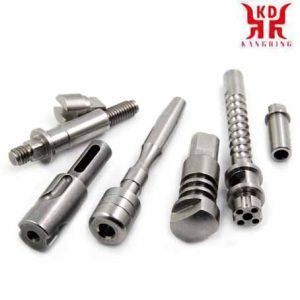
Obráběné lékařské titanové komponenty
Medicínské využití titanu jako materiálu se neustále rozšiřuje, neustále se otevírají nové aplikační možnosti v lidském těle. Na čepy se používají díly vyrobené z titanu, šrouby, dráty a tyče, desky, mřížky a klece k pohyblivým částem s klouby, jako jsou náhrady prstů na rukou nebo nohou. Výměna kostí a kloubů z frézovaných titanových dílů a titanových sestav je složitý úkol, ale operace, ortopedie a stomatologie jsou nepostradatelné bez implantátů vyrobených z titanu.
In many cases, titanium has also established itself as a material for instruments, nástroje, devices, templates, measuring templates and devices. In this context, the high strength, the low density and the resulting low weight, the corrosion resistance, the non-reflective surface and the non-magnetic properties of titanium are valued. For this reason, tweezers, retractors, needles and microneedles as well as holders, scissors, scalers, drills, electrodes and clips are preferably made of titanium. Surgeons and teachers use devices, brackets, gauges and measuring templates made of titanium. Titanium products are also used in the aerospace, optical and electronic industries.
The demand for products made of titanium is constantly increasing. The processing of titanium metal was around 60,000 t worldwide for around 20 years. It is now assumed that annual consumption amounts to around 300,000 t worldwide. The USA, Western Europe and China are seen as the main drivers of growth.
Continuous dynamic growth can be observed in the medical industry, which consequently also stimulates the machining industry. This growth goes hand in hand with intensive R&D activities and the longer lifespan of people in all industrialized nations.
Orthopedic implants represent a special market segment in which this dynamic is very noticeable. In this area, manufacturers are constantly on the lookout for new, improved processing machines and cutting tools in order to set themselves apart from the competition.
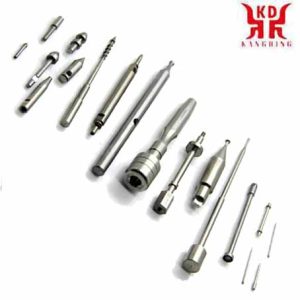
Titanové části implantované do těla
Replacing bones and joints is a complex task
Machining components for medical technology means dealing with sometimes very small, complex components made of difficult-to-machine materials such as titanium, Co-Cr alloys or stainless steel and not losing sight of the high dimensional accuracy. It is an extremely complex task to machine such complex orthopedic parts that have to replace human bones and joints.
In the case of components that are machined off the shelf, a lot of material has to be removed. Since the workpiece materials used can only be machined with lower machining parameters than steel, this makes the machining process very expensive. For this reason, some workpieces are preformed close to the contour, which in turn makes complex and therefore expensive clamping devices necessary.
Another factor that adds to the complexity of machining is the exact tolerances required. All of these considerations have led to the development of new machining technologies and solutions that also support small and medium-sized companies in the production of medical parts in the most competitive and productive way possible. Thanks to advanced tools in combination with the latest cutting material grades, innovative geometries and chip breakers, complex shapes can also be manufactured while maintaining precise tolerances.
Most of the implant workpieces are made from the titanium alloy Ti6AI4V. Stainless steels are also used, but surgeons prefer titanium because of its extremely beneficial strength-to-weight ratio and the fact that it grows better with human tissue.
Due to its low weight, high strength and biocompatibility, Ti6AI4V is the most common workpiece material for medical implants. Titanium implants are also useful for examinations that may be necessary, such as B. magnetic resonance or computed tomography are no obstacles.
Ti6AI4V is used for hip joints, bone screws, knee joints, bone plates, dental implants and surgical instruments, with cobalt-chrome alloys also being used more recently in the recent past.
The machining of titanium alloys requires higher cutting forces than the machining of steels. In contrast to steels with similar degrees of hardness, titanium alloys have metallurgical properties that make the machining process difficult.
Titanium leads to cutting edge breakouts when the tool enters and leaves the tool
Compared to more popular iron and aluminum alloys, titanium is more difficult to machine. Think of it as stainless steel, with tougher and longer chips being formed when machining titanium. Dále, there is a tendency for cutting edge breakouts to be observed when the tool enters and leaves the tool.
Tungsten carbide tools do not necessarily have to be coated because, unlike steel, they do not cause a chemical reaction with titanium, but they do have to be very sharp. If coatings are used, these are PVD-coated cutting material grades such as IC807 and IC808, because these help avoid overheating with higher machining parameters.
KANGDING already offers a wide range of indexable inserts and cutting inserts for machining titanium, which by and large can be used in all common tool holders. Its main features include very sharp cutting edges as well as polished or ground rake faces, which lead to a high surface quality and counteract the formation of built-up edges.
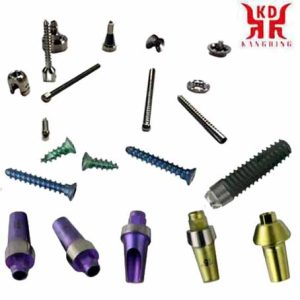
Části implantátů z titanové slitiny
Titanium places special demands on machining.
When machining components made of titanium, the tools and the machining parameters must be adapted. The tendency of titanium to work hardening can have an effect on turning and milling. A high level of friction on the cutting edge can cause the tool to quickly become blunt. Sharp tools, correct cutting parameters and desired chip formation are parameters that affect quality. The hardness of the tools and the heat resistance of the coating and the material must be adapted. There is a tendency for cutting edge breakouts as the tool enters and exits. This can be avoided by choosing the right tool and using the optimal machining parameters. The supply of coolants must be optimized due to the metallurgical properties of the titanium alloys. The properties of titanium and their combination lead to particular elasticity or tensile strength, which must be taken into account when milling or turning. If milling and parting off titanium parts are to be carried out economically, tj. with a long tool life and maximum feed rates, and high surface quality and dimensional accuracy are to be maintained, cutting tools also play an important role.
Frézování
KANGDING has use solid carbide end mills with sharp cutting edges for free-form milling. These end mills have rounded cutting edges of a maximum of 0.01 mm for semi-finishing and finishing. Navíc, tools for machining both titanium and stainless steel in Chatterfree design (= unequal tooth pitch) have been use. They have excellent vibration-damping properties. Thanks to this unique geometry, high surface quality and tool life are achieved even at maximum feed rates.
With its relatively low modulus of elasticity, titanium is more elastic than steel, so that the workpiece material to be machined tends to spring back. Thin-walled workpieces are deflected under the cutting pressure, which leads to chatter marks and tolerance problems on the component. The solution to these problems is to stabilize the entire system by using sharp cutting edges in combination with adapted geometries.
Dále, titanium alloys have a strong tendency to react chemically with the cutting tools (especially in the case of coated tools) and generate built-up edges.
Optimized coolant supply for titanium processing
All cutting inserts and indexable inserts are available in the cutting material grades IC807 and IC808, which have been the preferred cutting material grade for machining titanium in the aerospace industry for years. Today the product range of tools for the machining of medical components includes end mills with extremely sharp cutting edges and polished rake faces; Solid carbide milling cutters from a diameter of 0.8 mm and reamers from a diameter of 3 mm; Different types of indexable inserts with aggressive WF (= wiper finish) or MD (lékařský) chip formers as well as titanium versions of the Jetcut parting off tools.
KANGDING has carried out extensive market studies on the most effective tools for machining these very complex orthopedic parts. On this basis, KANGDING has USE specific tools, cutting inserts and indexable inserts and chipformers for machining Ti6AI4V in order to be able to achieve the tolerances required by the industry.