تصنيع الأجزاء الدوارة
يشتمل تطوير مركز الدوران على جزء كبير من الأجزاء الدوارة (يقدر شخص ما أنه يمثل حوالي 1/2). بالإضافة إلى تحول, العمليات مثل الطحن, حفر, والتنصت مطلوبة أيضًا. فضلاً عن ذلك, وقت المعالجة لكل عملية للجسم الدوار قصير نسبيًا. لذلك, من الضروري إجراء معالجة مركبة متعددة العمليات على الجسم الدوار تحت مشبك واحد على أداة آلية, وأخيرًا تم تطوير مركز الخراطة المركب في السبعينيات.
Compared with ordinary CNC lathes, the turret tool post of the turning and milling center is equipped with power tools that can rotate the milling cutter, drill and tap. في نفس الوقت, the machine tool spindle also has the C-axis function that can be accurately indexed according to the CNC program and interpolated with the X-axis or Z-axis. This 3-axis (X, ز, ج) the control can be performed at a turning center of one clamping part turning body turning, طحن, حفر, التنصت. حتى الآن, it is still the most used composite machining machine tool for rotating parts in industrial production.
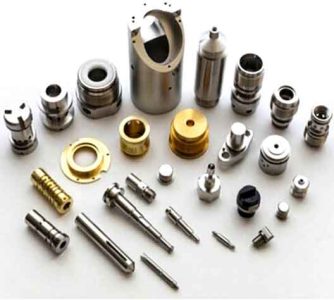
تصنيع الأجزاء الدوارة
Since then, the turning center has further developed in the direction of expanding the range of processing technology. In order to drill or mill holes or slots that deviate from the center line of the rotating body, a turret tool holder with Y-axis control has been developed. And correspondingly introduced a turning center controlled by 4 محاور (X, ي, ز, ج). لكن, no matter how the single-spindle turning center expands the process range, it still cannot solve the problem of the secondary machining of the back side of the rotating body under one clamping (إنه, the machining of the workpiece clamping end). نتيجة ل, double-spindle turning centers appeared in the 1980s. Most of the two spindles of this machine tool are arranged oppositely on the same axis, so that after turning and processing the main end of the rotating body, the second spindle automatically picks up the workpiece from the spindle to process the clamping end.
Since the machining tasks of the clamping end are generally relatively simple, the second spindle is usually called the sub-spindle, and its power is relatively small. The double-spindle turning center can be equipped with one tool post, but most of them are two tool posts, in order to improve the processing efficiency and give full play to the potential of the machine tool. Axis of the body on the same side of the machine, equipped with mutually opposed spindles (18.65kW) and a secondary spindle (11kW). The speed of the two spindles is 0~4000r/min, and both can be controlled by the C axis. The sub-spindle can also move along the axis to pick up the workpiece that has been machined on the spindle. A 10-tool turret tool post is provided above the main spindle and below the sub-spindle. Each tool position on the turret tool post can be equipped with a powered tool with a power of 3.7kW and a speed of 80-8000r/min. The upper tool post is controlled by 3 محاور (X1, Y1, Z1), and the lower tool post is controlled by 2 محاور (X2, Z2).
The rise of the turning center developed from the turning center. The 5-axis control (X, ي, ز, ب, ج) turning and milling center became a hot spot in the late 1990s. Not only has it further increased the B-axis control (to make the tool post rotate around the Y-axis), to drill and mill bevels. And instead of using the traditional turret tool post of the turning center, a high-speed and more powerful electric spindle tool post is used instead.
Since the electric spindle on the tool post can only be equipped with one tool at a time (the electric spindle is locked and does not rotate during turning), it is also equipped with an automatic tool changer and a tool magazine like a machining center. The milling and drilling capacity of this machine tool is equivalent to a small or medium-sized machining center. Its essence is to integrate a CNC lathe and a machining center, so it is named a turning-milling center.
The turning speed of the turning and milling center table is higher than that of the original machining center. في نفس الوقت, the (electric) spindle of the machine tool must be locked and a turning tool can be installed. The newly developed turning-milling center DMU80FD of German DMG company belongs to this type. The structure of DMU80FD is exactly the same as the company’s DMUP series machining center, and it has 5-axis and 5-face high-speed milling of the P series machining center. For all processing functions, the worktable of this machine adopts direct drive technology, the maximum speed is 500r/min, and the maximum speed of the machine tool spindle is also 2000r/min. لذلك, after the workpiece is clamped on this machine tool, 5-sided and 5-axis machining and compound machining from milling, حفر, ممل, tapping and turning can be realized efficiently.