تعد معايرة أدوات أدوات آلة CNC مهارة مهمة في التصنيع. تحدد دقة إعداد الأداة دقة تصنيع الجزء, وتؤثر كفاءة أداة المعايرة بشكل مباشر على كفاءة تصنيع الجزء. يعد إعداد الأداة مهمًا جدًا لعمليات معالجة الأدوات الآلية.
بعد تشغيل مخرطة CNC, عودة الصفر (نقطة مرجعية) يجب إجراء العملية. والغرض منه هو إنشاء مرجع موحد لقياس الموقف, يتحكم, وعرض مخرطة CNC, إنه, تعود الأداة إلى أصل الأداة الآلية. عادة ما يكون أصل الآلة الآلية عند الحد الأقصى للضربة الإيجابية للأداة, ويتم تحديد موضعه بواسطة مستشعر موضع أداة الآلة. بعد أن تعود الأداة الآلية إلى الصفر, المسافة بين موضع الأداة (تلميح الأداة) وتم إصلاح أصل الآلة. لذلك, من أجل تسهيل معايرة الأداة ومعالجتها, يمكن اعتبار موضع طرف الأداة بعد عودة الماكينة صفرًا بمثابة أصل الماكينة.
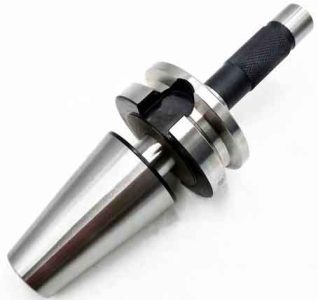
طريقة معايرة الأدوات للتصنيع باستخدام الحاسب الآلي
معايرة الأداة هي عملية إنشاء نظام إحداثيات قطعة العمل في نظام إحداثيات الآلة الخاص بأداة الآلة CNC, وجعل أصل نظام إحداثيات قطعة العمل يتطابق مع أصل البرمجة. قم بقياس المسافة بين نقطة برمجة طرف الأداة في نظام إحداثيات أداة الآلة وأصل المعالجة في الاتجاهين X وZ عن طريق القطع التجريبي أو طرق عدم الاتصال, وقم بتعيين القيمة على معلمات الجهاز. من خلال برنامج الدعوة, تم إنشاء نظام الإحداثيات لقطعة العمل. تعتمد القيمة الإحداثية المطلقة للنقطة الأساسية في البرنامج على أصل نظام إحداثيات قطعة العمل المعمول بها, وتتم معالجة محيط الجزء.
هناك طرق عديدة لمعايرة السكين على مخرطة CNC, ويشيع استخدام طريقة القطع التجريبية في العمل. وفيما يلي يقدم FANUC-0أنا مخرطة CNC طريقة أداة المعايرة شائعة الاستخدام.
1. طريقة إزاحة أداة القياس والإدخال
1) قم بتجربة قطع الدائرة الخارجية لقطعة العمل باستخدام الأداة المحددة, وقم بمحاذاة الأداة في الاتجاه X. في وضع التشغيل اليدوي, حاول قطع الدائرة الخارجية, حافظ على اتجاه X دون تغيير, وتخرج الأداة على طول المحور Z. استخدم الفرجار الورني لقياس قيمة القطر α للدائرة الخارجية المقطوعة, وانقر على “OFFSETSETING” button to enter the shape compensation parameter setting interface. Move the cursor to the X position of tool compensation, enter Xα, and click the soft key [Measure]. The numerical control system automatically calculates the coordinates of the current tool tip in the X direction in the machine tool coordinate system, and the X direction completes the calibration of the tool.
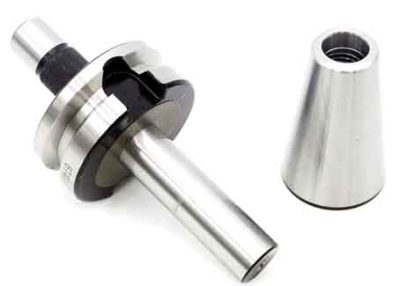
معايرة الأدوات الآلية
2) Use the selected tool to cut the end face and calibrate the tool in Z direction. في وضع التشغيل اليدوي, the tool cuts the end face of the workpiece to the center. Then the Z direction remains motionless, and the tool exits in the X direction. Enter the shape compensation parameter setting interface, move the cursor to the corresponding position of the tool compensation Z coordinate, enter Z0, press the [Measure] soft key, يتم إدخال إزاحة الأداة المقابلة تلقائيًا, واكتمل إعداد الأداة. تهدف هذه الطريقة إلى ضبط أصل المعالجة في منتصف الطرف الأيمن من قطعة العمل, وهي طريقة شائعة لأجزاء العمود العام. إذا كان جزءًا متماثلًا من اليسار إلى اليمين, يجب ضبط أصل المعالجة في المركز المتماثل لقطعة العمل, ثم أدخل Zβ, β هو نصف الطول المحوري للجزء.
ثم أدخل قيمة نصف قطر قوس الأنف للأداة R ورقم موضع الأداة T وفقًا للحجم الهندسي وموضع تثبيت الأداة, على سبيل المثال:
بالنسبة للرقم. 1 أداة, نصف قطر قوس طرف الأداة هو R = 0.8 مم, حرك المؤشر إلى الموضع المقابل للرقم. 1 أداة أدناه R, أدخل 0.8, أدخل رقم موضع الأداة في الموضع المقابل لـ T, واضغط “مدخل” للإدخال, ومن ثم يمكن استخدامه للمعالجة.
2. سكين معايرة الاتجاه Z بعد تدوير قطعة العمل
بعد أن يتم تشغيل الشغل, يجب أن تضمن المعالجة الطول الإجمالي للجزء بعد المعالجة. لذلك, يجب معايرة السكين مرتين. الاتجاه X هو نفس طريقة إعداد الأداة السابقة. خطوات إعداد أداة الاتجاه Z هي كما يلي:
قطع الوجه النهائي لقطعة العمل إلى المركز, حافظ على اتجاه Z ثابتًا, اضغط على زر X للأمام, وتخرج الأداة. قم بقياس الطول الإجمالي لقطعة العمل الفارغة في اتجاه Z مثل Z1, الطول الإجمالي المطلوب لقطعة العمل هو Z, وفرق الطول هو ∆=Z1-Z. قبل تنفيذ البرنامج, يجب عليك أولاً تعيين نقطة O كأصل المعالجة (أنظر للشكل 1), وأدخل إلى واجهة إعداد معلمة تعويض الشكل. حرك المؤشر إلى موضع الإحداثيات Z, أدخل Z∆, (∆ هي قيمة الإحداثيات Z للموضع الحالي لتلميح الأداة في إحداثيات قطعة العمل المنشأة حديثًا), press the [Measure] soft key, ويتم إدخال إزاحة الأداة المقابلة تلقائيًا.
3. يقوم G92 بتعيين نظام إحداثيات قطعة العمل
1) استخدم أداة تحويل خارجية لمحاولة قلب الدائرة الخارجية أولاً. بعد قياس قطر الدائرة الخارجية, يتم سحب الأداة في الاتجاه الإيجابي للمحور Z, ويتوقف المغزل. قم بتدوين قيمة الإحداثيات المطلقة X1 للأداة في نظام إحداثيات الأداة الآلية في هذا الوقت, وقياس قطر الدائرة الخارجية D في نفس الوقت.
2) قطع الوجه النهائي إلى المركز, X لا يتحرك, والخروج على طول الاتجاه Z. Write down the absolute coordinate value Z1 of the tool in the machine tool coordinate system at this time;
3) Select the starting point. The starting point should be selected outside the workpiece. If the starting point is set at 50mm in the X direction and 50mm in the Z direction from the center of the right end face. Then the position of the starting point in the machine coordinate system X = X1-D+100.0 (diameter programming), Z=Z1+50.0;
4) Adjust the tool to reach the point. Before executing the program with the workpiece coordinate system set by G92, the tool must be adjusted to the up-point position. Methods as below:
First move the tool to the position close to the starting point in the manual state, and then adjust the magnification by the handwheel to reach the precise position;
5) في هذا الوقت, يجب أن تكون نقطة البداية للبرنامج: G92 X100.0 Z50.0
وصف:
(1) يجب معايرة الأداة قبل تنفيذ هذه التعليمات, ويجب وضع طرف الأداة في موضع نقطة البداية الذي يتطلبه البرنامج عن طريق ضبط أداة الآلة;
(2) لن يؤدي تنفيذ أمر G92 إلى أي حركة لأداة الآلة. فقط دع النظام يستبدل قيمة الإحداثيات القديمة بقيمة الإحداثيات الجديدة, وبالتالي إنشاء نظام إحداثيات جديد.
عند استخدام طريقة القطع التجريبية للتحقق من الأداة, يأتي خطأ أداة التحقق بشكل أساسي من خطأ القياس بعد القطع التجريبي لقطعة الشغل والخطأ الناتج عن الفحص البصري أثناء العملية. التدابير الرئيسية لتقليل خطأ إعداد الأداة هي: يجب أن يكون الموقف صارما, the operation must be careful, and the reading must be accurate; عند المعالجة, consider the influence of the machine tool’s repeated positioning accuracy on the tool setting accuracy and the influence of the installation height of the tool location point on the tool setting accuracy; After tool setting, the tool compensation value should be corrected according to the error between the actual size of the part processed by the tool and the programmed size.
Numerical control lathes have a variety of control systems. The tool calibration methods include manual calibration, calibration of external calibrator of the machine tool, and automatic calibration. Manual tool setting adopts the mode of “trial cutting-measurement-adjustment”, which is simple and economical, takes a long time in the machine tool, and has a large error. Using the calibrator for tool setting can automatically calculate the difference between the length of each knife and the standard knife, and store it in the system. When processing other parts, only the standard knife is needed, which greatly saves work assistance time. فضلاً عن ذلك, the use of a tool setting instrument for tool setting can eliminate errors during measurement and greatly improve the accuracy of tool setting. Automatic tool setting is realized by the tool tip detection system. The tool tip approaches the touch sensor at a set speed. When the tip of the tool touches the sensor and sends a signal, the CNC system immediately records the coordinate value at that moment and automatically corrects the tool compensation value. Although the principle of inputting parameters of external tool setting instrument and automatic tool setting is similar to that of manual tool setting, the principle and method of measurement are different, the degree of automation is high, and the work efficiency is improved.
Each tool calibration method has its own advantages and disadvantages, and operators can use them flexibly according to their actual needs. في هذا الطريق, the entire tool setting work is simple, and the processing quality can be ensured, and the auxiliary time can be greatly saved, and the production efficiency can be effectively improved.