FOR EVERY PURPOSE
معالجة الألمنيوم, الفولاذ المقاوم للصدأ, التيتانيوم, البلاستيك وأكثر من ذلك بكثير باستخدام آلة طحن البوابة CNC. بفضل عملية الطحن التي يتم التحكم فيها بواسطة الكمبيوتر، يمكنك الإنتاج بدقة, بدقة وموثوقية. سواء لورشة العمل (هواية, صناعة نموذج, صانع), التجارة (إنتاج CNC, بناء النموذج الأولي, إنتاج السلسلة). ستجد معنا أجزاء الطحن المناسبة لتطبيقك.
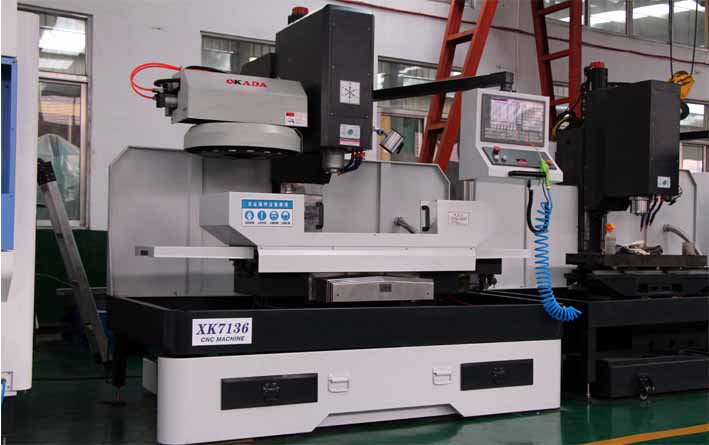
ماكينة طحن CNC
The introduction of computerized numerical control (CNC) has exponentially expanded applications of industrial machines by programmable automation of production and achieving impossible movements performed manually. such as circles, diagonal lines and other figures complicated that enable the manufacture of parts with highly complex profiles. This also translates into the optimization of many essential variables of any manufacturing process: productivity, precision, safety, speed, repeatability, flexibility and reduction of waste.
The multiplicity of milling machines that exist today has comfortably expanded into the proliferation of their CNC-equipped peers. في الحقيقة, there are also special kits to transform old milling machines into a CNC milling machine.
أساسًا, the CNC milling machines are very similar to the conventional ones and have the same moving parts, إنه, the table, the cutting head, the spindle and the side and cross slide carriages. لكن, they do not have levers or cranks to operate these moving parts, but rather a screen inserted in a panel full of controls and a metal box that houses the electrical and electronic components that regulate the operation of motors destined to carry out the same work that they did. the levers and cranks of the old machines. Among these components is the CNC, which is a computer mainly responsible for the movements of the milling machine through the corresponding software. The combination of electronics and drive motors or servo motors is capable of achieving all possible milling operations.
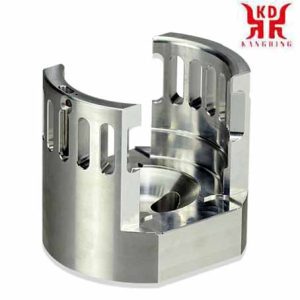
التصنيع باستخدام الحاسب الآلي لآلة الطحن العملاقة
To understand the movement control exercised by the CNC, we are going to briefly review how a conventional milling machine works.
The figure schematizes a typical milling machine. In this type of machine, the cranks actuate the moving parts manually so that the cutting tool (milling cutter) moves linearly in at least three axes, which are called main axes:
X axis: horizontal and parallel to the clamping surface of the part. It is associated with the movement in the longitudinal horizontal plane of the milling table.
والمحور: forms a direct direction trihedron with the X and Z axes. It is associated with the movement in the horizontal transverse plane of the milling table.
Z axis: where the cutter is mounted, it is the one that has the cutting power and can adopt different positions according to the possibilities of the head. It is associated with the vertical displacement of the machine head.
If the milling machine has a fixed table, these three movements are executed by the spindle.
لكن, it is clear that the milling of more complex parts will require a greater number of axes whose trajectory is not only linear, but also rotary. At this point is where the concept of CNC comes into play, giving rise to a multiplicity of complementary axes controlled independently and determined by the movement of rotary tables and / or adjustable heads. This gives rise to a variety of machine models that allow the machining of the part by different planes and approach angles.
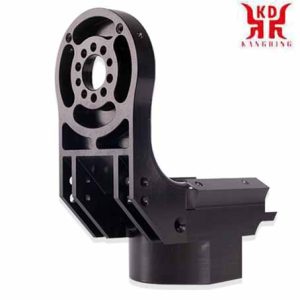
CNC machining cavity of milling machine
In the following figure we see an example of a CNC milling machine with its basic components and main (X, ي, ز) and complementary (ب, دبليو) محاور.
1 – Column
2 – Workpiece
3 – Milling table, with movement in the X and Y axes
4 – Strawberry
5 – Cutting head including spindle motor
6 – CNC control panel
7 – Coolant hoses
X, ي, ز – Main axes of displacement
ب – Complementary axis of rotary displacement of the cutting head
دبليو – Complementary axis of longitudinal displacement of the cutting head
The main function of the CNC is to control the movements of the table, the transverse and longitudinal carriages and / or the spindle along their respective axes by means of numerical data. لكن, this is not all, because the control of these movements to achieve the desired final result requires the perfect adjustment and the correct synchronization between different devices and systems that are part of every CNC process. These include the main and complementary axes, the transmission system, the workpiece clamping systems and the tool changers, each of which presents its modalities and variables that must also be properly stipulated.
This rigorous control is carried out by software that is supplied with the milling machine and is based on one of the CNC numerical programming languages, such as ISO, HEIDENHAIN, Fagor, Fanuc, SINUMERIK and Siemens. This software contains numbers, letters and other symbols – على سبيل المثال, the G and M codes – that are encoded in an appropriate format to define an instruction program capable of carrying out a specific task. G codes are machine motion functions (rapid moves, feeds, radial feeds, pauses, cycles), while M codes are miscellaneous functions that are required for machining parts, but are not machine motion. (spindle start and stop, تغيير الأداة, coolant, program stop, إلخ.). From this it follows that to operate and program this type of machine requires basic knowledge in machining operations on conventional equipment, elementary knowledge of mathematics, technical drawing and handling of measuring instruments.
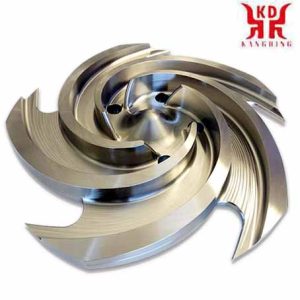
تجهيز طحن المكره من آلة الطحن
Currently the use of CAD (التصميم بمساعدة الحاسوب) and CAM (computer-aided manufacturing) programs is an almost mandatory complement to any CNC machine, therefore. عمومًا, the manufacture of a part involves the combination of three types of software:
نذل - وغد: makes the design of the part.
CAM: calculates the displacements of the axes for the machining of the part and adds the feed rates, rotation speeds and different cutting tools.
Control software (included with the machine): receives the instructions from the CAM and executes the orders to move the moving parts of the milling machine in accordance with these instructions.
The following video illustrates the manufacture of a part using CAD / CAM:
CNC milling machines are specially adapted for milling profiles, cavities, surface contours and die cutting operations, in which two or three axes of the milling table must be controlled simultaneously. Although, depending on the complexity of the machine and the programming carried out, CNC milling machines can operate automatically, an operator is usually required to change the cutters, as well as to mount and dismount the workpieces.
Industries that routinely use CNC milling machines include automotive (design of engine blocks, قوالب, and miscellaneous components), الفضاء الجوي (aircraft turbines), and electronics (mold and prototyping), as well as manufacturing of machinery, instruments and electrical components.
Let’s see in this video some types of CNC milling machines, as well as working examples.