في الطحن, من الخصائص المهمة لسبائك التيتانيوم التوصيل الحراري السيئ للغاية. بسبب القوة العالية والتوصيل الحراري المنخفض لمواد سبائك التيتانيوم, حرارة قطع عالية للغاية (تصل إلى 1200 درجة مئوية إذا لم يتم التحكم فيها) يتم إنشاؤها أثناء المعالجة. لا يتم تفريغ الحرارة مع الرقائق أو امتصاصها بواسطة قطعة العمل, ولكنه يتركز على طليعة CNC. مثل هذه الحرارة العالية سوف تقلل بشكل كبير من عمر الأداة.
Using special CNC processing technology, it is possible to improve the performance and life of the tool (using the correct CNC processing technology to control the temperature, the temperature can be reduced to 250 ~ 300 درجه مئوية).
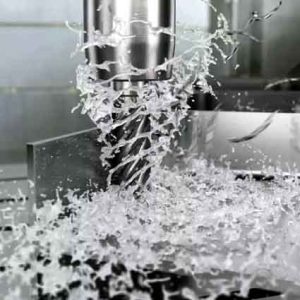
CNC طحن عالي السرعة لأجزاء سبائك التيتانيوم
1. Reduce heat generation in titanium milling
Reducing the radial and axial engagement between the tool and the titanium workpiece can control the generation of cutting heat. For titanium alloys, the adjustment period for speed, معدل التغذية, and radial and axial joints is very short before a built-up edge is generated due to overheating. In order to achieve proper tool life, the maximum “joining arc length” ل 15% is required for machining titanium alloys, compared with 50% ل 100% when machining ordinary steel. Reducing the contact arc length can increase the cutting speed and increase the removal rate of titanium without losing the life of the tool.
Using a cutting tool with an angle of 45° or thinning titanium chips can increase the contact length between the cutting edge of the tool and the chips. This reduces local high temperatures, extends the life of the cutting edge, and also allows higher cutting speeds.
2, Geometrical design of blades for cutting titanium
عند طحن سبائك التيتانيوم, the use of peripheral grinding inserts is essential to minimize the cutting pressure and friction with the machined surface. The geometric angle of the milling insert must be positive, but this is not enough to ensure optimal performance. If in order to strengthen the first part of the cutting edge, a small initial angle with higher strength is used. Then the use of a larger secondary angle (to obtain a larger front chamfer) is the best geometric design for enhancing the compression resistance of the milling insert and prolonging the tool life. فضلاً عن ذلك, slight passivation also helps to protect the cutting edge, but the size of the passivation must be coordinated with the cutting process and maintain tight tolerances. When machining titanium requires the use of sharp cutting edges cut the material, but too sharp cutting edge is prone to chipping and shorten tool life. Proper passivation can protect the cutting edge and avoid premature chipping. The correct blade geometry parameters can reduce the stress and pressure on the tool material, make the tool longer life and improve processing efficiency.
The cutting angle of the milling cutter body and the insert must be a positive angle to obtain a progressive cutting effect, and to avoid impact on the entire cutting edge during cutting and failing to obtain the desired milling effect. If this is not done, the structure of the workpiece may be deformed, making processing impossible.
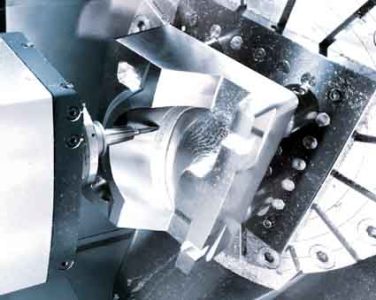
طحن تجويف التيتانيوم وطحن الاستيفاء الحلزوني
3. Cavity milling and spiral interpolation milling of titanium parts
When performing titanium pocket milling and spiral interpolation milling, internally cooled milling tools must be used. If possible, a constant pressure coolant should be used, which is especially important for deep cavity or deep hole machining.
When processing deep cavities, the use of high-density cemented carbide extension tools with modular cutting heads can increase rigidity and reduce flexural deformation to obtain the best processing results.
The function of the coolant is to remove the chips from the cutting area and avoid secondary cutting that may cause early tool failure. في نفس الوقت, the coolant also helps to reduce the temperature of the cutting edge, reduce the geometric deformation of the workpiece, and extend the life of the tool.
Spiral interpolation milling holes with milling cutters can reduce the use of other tools (such as drills, إلخ.) in the tool magazine. A milling cutter of one diameter can be used to machine holes of different sizes.
As the application of titanium alloys in the aerospace industry continues to grow, the cutting technology that supports high-efficiency CNC machining of titanium alloys is also constantly evolving. Due to the large demand for the processing capacity of titanium alloy parts, those workshops or manufacturers that use the most effective processing technology will benefit first.