The drilling is semi-closed CNC cutting. The cutting temperature is very high in the process of drilling titanium alloy, the rebound after drilling is large, the drill chips are long and thin, easy to stick and not easy to discharge. Drilling of titanium often causes the bit to be bitten, twisted, وما إلى ذلك وهلم جرا. لذلك, the drill bit is required to have high strength and good rigidity, and the chemical affinity between the drill bit and the titanium alloy is small. It is best to use cemented carbide drills, but the most commonly used at present is still twist drills, after taking some measures to improve, better results can also be achieved.
(1) Improve drill bits: In order to meet the needs of titanium alloy CNC drills, the following improvement measures should be taken for twist drills:
Increase the top angle of the drill bit, 2Ф=135°~140°; Increase the clearance angle at the outer edge of the drill bit, taking 12°~15°; Increase the helix angle, p=35°~40°; Increase the thickness of the drill bit core and take (0.22~0.4) do (do is the diameter of the drill bit).
Use “س” shape or “X” shape to sharpen the chisel edge of the drill, the chisel edge length b=(0.08~0.1)do, while ensuring that the symmetry of the chisel edge is ≤0.06 mm. Both types of chisel edges can form a second cutting edge, which plays a role of chip separation and reduces the axial force during drilling.
The most commonly used is to grind a cutting edge shape suitable for drilling titanium alloys on a twist drill. إنه, the titanium alloy group drill, the shape of the cutting part is shown in Figure 7-1. In the figure, the outer and inner cutting edge angles 2φ and 2φ′ are 130°~140° when the drill diameter do>3~10mm, and 125°~140° when do>10~30 mm;
The clearance angle α of the outer edge is 12°~18° when do>3~10 mm, and 10°~15° when do>10~30 mm;
Chisel edge angle ψ=45°;
Internal cutting edge angle γτ=-10°~-15°;
Inner blade angle τ=10°~15°;
The relief angle of the arc blade aR=18°~20°.
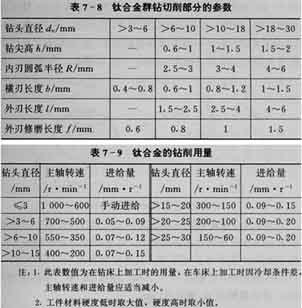
Relevant parameters and drilling amount of titanium alloy group drill
See Table 7-8 and Table 7-9 for the relevant parameters and drilling quantities of titanium alloy group drills.
Four guiding blades are made on the drill bit to increase the section moment of inertia of the drill bit, improve rigidity, and naturally form two auxiliary cooling grooves. The durability is about 3 times higher than that of standard drills, and the cutting temperature is reduced by about 20%. في نفس الوقت, the amount of hole expansion is reduced due to the stable guiding. على سبيل المثال, the hole expansion of a Ф3 mm four-flute drill bit is 0.03~0.04 mm, while the standard drill bit is 0.05~0.06 mm.
(2) Choose a suitable gun drill: When drilling deep holes with a titanium alloy aspect ratio greater than 5, when the hole diameter is less than or equal to 30 مم, a cemented carbide gun drill is generally used, كما هو مبين في الشكل 7-2; When the hole diameter is greater than 30 مم, a cemented carbide BTA drill bit or jet suction drill is used. Use the gun drill shown in Figure 7-2 to drill the hole of TC4, the hole depth is 204 مم (length-to-diameter ratio is about 26), and the surface roughness Ra is 1.6 ميكرومتر. The productivity is increased by 4 مرات, the chips are in the shape of “Plum” أو “ج”, and chip removal is normal.
Water-based cutting fluids should not be used when drilling deep holes, because water may form steam bubbles on the cutting edge at high temperatures, which may easily generate built-up edges and make drilling unstable. It is advisable to use N32 engine oil and kerosene, the ratio of which is 3:1 أو 3:2, and sulfurized cutting oil can also be used.
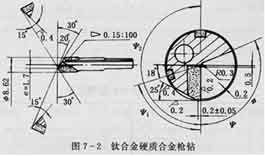
Cemented carbide gun drills for drilling titanium alloys
When using a carbide gun to drill deep holes with a length-to-diameter ratio greater than 30. Vibration drilling by applying vibration of less than 100 Hz in the axial direction can make the surface roughness Ra of the workpiece 0.3 μm and increase the productivity by 5 مرات. The specific parameters are Vc=17 m/min, f=0.033 min/r, the amplitude is 0.07 مم, the frequency is 35 Hz, the roundness of the workpiece is 4 ميكرومتر, and the surface roughness Ra is 0.33 ميكرومتر.
(3) Choose the right cutting fluid: Electrolytic cutting fluid can be used when drilling shallow holes. Its ingredients are sebacic acid 7%-10%, triethanolamine 7%-10%, glycerol 7%-10%, boric acid 7%-10%, sodium nitrite 3%-5%, and the rest is water.