لا ينبغي لبرنامج التصنيع باستخدام الحاسب الآلي المثالي أن يضمن معالجة قطع العمل المؤهلة المطابقة للرسومات فحسب, ولكن يجب أيضًا تمكين تطبيق وظائف أداة آلة CNC بشكل معقول والاستفادة منها بالكامل. إن أداة آلة CNC هي معدات أتمتة عالية الكفاءة. كفاءتها هي 2 ل 3 مرات أعلى من الأدوات الآلية العادية. لذلك, لإتاحة الفرصة الكاملة لهذه الميزة لأدوات آلة CNC, يجب على المرء أن يتقن أدائه, صفات, وطرق التشغيل. في نفس الوقت, يجب تحديد خطة المعالجة بشكل صحيح قبل البرمجة.
بسبب الاختلاف في حجم الإنتاج, تختلف خطة المعالجة لنفس الجزء. وفق شروط محددة, وينبغي اختيار خطة عملية اقتصادية ومعقولة.
(1) تقسيم إجراءات المعالجة
يمكن أن تكون أجزاء المعالجة على أدوات آلة CNC أكثر تركيزًا في العملية, ويجب إكمال جميع العمليات قدر الإمكان في إعداد واحد. بالمقارنة مع معالجة الأدوات الآلية العادية, تقسيم إجراءات المعالجة له خصائصه الخاصة, وهناك نوعان من المبادئ شائعة الاستخدام لتقسيم الإجراءات.
1. مبدأ ضمان الدقة
تتطلب معالجة التحكم العددي تركيز العملية قدر الإمكان, وغالبًا ما يتم الانتهاء من المعالجة الخشنة والدقيقة في مشبك واحد. من أجل تقليل تأثير التشوه الحراري وتشوه قوة القطع على الشكل, دقة الموقف, دقة الأبعاد وخشونة السطح لقطعة العمل, يجب أن يتم تنفيذ الآلات الخام والتشطيب بشكل منفصل. لأجزاء العمود أو القرص, سيتم تنفيذ الآلات الخام أولا, ترك هامش صغير للتشطيب لضمان متطلبات جودة السطح. في نفس الوقت, لبعض قطع العمل مربع, من أجل ضمان دقة تصنيع الثقب, يجب معالجة السطح أولاً ثم معالجة الثقب.
2. مبادئ تحسين كفاءة الإنتاج
في التصنيع باستخدام الحاسب الآلي, من أجل تقليل عدد تغييرات الأداة وتوفير وقت تغيير الأداة, بعد الانتهاء من جميع الأجزاء التي تحتاج إلى معالجة بنفس الأداة, يجب استخدام أداة أخرى لمعالجة الأجزاء الأخرى. في نفس الوقت, ينبغي التقليل من السكتة الدماغية الخمول. عند معالجة أجزاء متعددة من قطعة العمل بنفس الأداة, وينبغي استخدام أقصر طريق للوصول إلى كل جزء من أجزاء المعالجة.
في التمرين, ينبغي النظر في عملية التصنيع باستخدام الحاسب الآلي بشكل شامل وفقًا للخصائص الهيكلية والمتطلبات الفنية لأجزاء محددة.
(2) تحديد طريق المعالجة
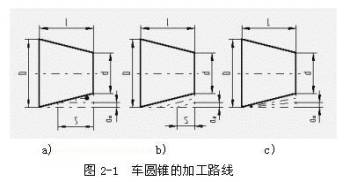
طريق التصنيع لتحويل الأجزاء المخروطية
في التصنيع باستخدام الحاسب الآلي, مسار الحركة واتجاه الأداة (بالمعنى الدقيق للكلمة, نقطة موضع الأداة) نسبة إلى قطعة العمل تسمى مسار المعالجة. إنه, المسار الذي تنتقل إليه الأداة من نقطة إعداد الأداة إلى نهاية برنامج المعالجة, بما في ذلك مسار القطع وضربات الخمول غير المقطوعة مثل إدخال الأداة وإرجاعها. يجب أن يضمن تحديد مسار المعالجة أولاً دقة الأبعاد وجودة سطح الأجزاء المعالجة, وثانيا النظر في الحساب الرقمي البسيط, أقصر مسار ممكن للأداة, والكفاءة أعلى.
تحلل الأمثلة التالية طرق المعالجة الشائعة الاستخدام عند معالجة الأجزاء باستخدام أدوات آلة CNC.
1. تحليل مسار التصنيع لتحويل المخروط
لتحويل المخروط الخارجي على مخرطة CNC, بافتراض أن القطر الرئيسي للمخروط هو D, القطر الصغير هو د, وطول المخروط L, يظهر الشكل مسار المعالجة لمخروط الدوران 2-1.
وفقًا لمسار القطع المتدرج في الشكل 2-1أ, تحول خشن ذو قطعتين, وآخر تحول جيد بقطع واحد; يجب حساب مسافة الأداة النهائية S للدورة الخشنة ذات القطعتين بدقة, والتي يمكن أن يكون لها مثلثات مماثلة:
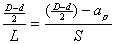
تصميم مسار القطع للأجزاء المتدرجة
لهذا النوع من مسار المعالجة, سمك الدوران هو نفسه بالنسبة للتحول الخام, لكن سمك الدوران يختلف بالنسبة للتحول الدقيق; في نفس الوقت, مسار القطع للأداة هو الأقصر.
وفقًا لطريق القطع المائل المماثل في الشكل 2-1ب, من الضروري أيضًا حساب مسافة الأداة النهائية S أثناء الدوران القاسي, والتي يمكن حسابها أيضًا من مثلثات مماثلة:

تصميم أقصر مسار لحركة قطع الأداة
وفقا لطريق المعالجة هذا, مسافة القطع للأداة قصيرة نسبيًا.
وفقًا لمسار معالجة الخط المائل في الشكل 2-1ج, يتم تحديد مقدار تطبيق الأداة الخلفية فقط في كل مرة, بدلاً من حساب مسافة الأداة النهائية, البرمجة مريحة. لكن, سمك كل قطع يتغير, ومسار القطع للأداة أطول.
2. تحليل مسار المعالجة لقوس الدوران
استخدم G02 (أو G03) أمر لتحويل القوس. إذا تمت معالجة القوس عن طريق الدوران مرة واحدة, كمية السكين كبيرة جدًا ومن السهل ضرب السكين. لذلك, في الدوران الفعلي للأقواس, مطلوب قطع متعددة, ويتم إزالة كمية كبيرة من الفائض أولاً, ومن ثم يتم تشغيل القوس المطلوب.
فيما يلي وصف لطرق المعالجة الشائعة لأقواس الدوران.
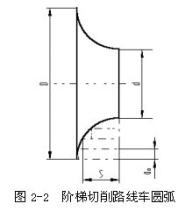
تحول القوس لتصميم مسار قطع الخطوة
شكل 2-2 يُظهر مسار القطع التدريجي لقوس الدوران. إنه, يتم إجراء التحول الخام الأول إلى خطوات, ويتم قطع القوس بالقطع النهائي. في هذه الطريقة, بعد تحديد سمك الدوران, يجب حساب مسافة الأداة النهائية S للدوران الخام بدقة, إنه, يتم حساب نقطة تقاطع القوس والخط المستقيم. في هذه الطريقة, مسافة حركة القطع للأداة أقصر, لكن الحساب العددي أكثر تعقيدا.
شكل 2-3 يُظهر مسار القطع بالقوس المتحد المركز لقوس الدوران. إنه, تحول مع دوائر نصف قطرها مختلفة, وأخيرا معالجة القوس المطلوب. تعتبر هذه الطريقة أسهل في تحديد إحداثيات نقطة البداية ونقطة النهاية للقوس 90 درجة بعد تحديد مقدار ap لكل أداة. الحساب العددي بسيط, والبرمجة مريحة, لذلك يتم استخدامه في كثير من الأحيان. ولكن عند المعالجة حسب الشكل 2-3ب, وقت السكتة الدماغية الخمول أطول.
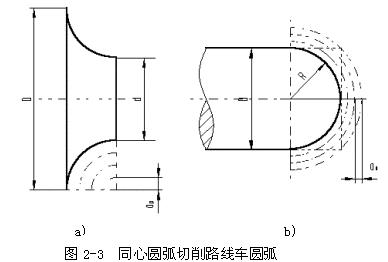
تصميم قوس مسار القطع من أقواس متحدة المركز
شكل 2-4 يُظهر مسار القطع لطريقة مخروط الدوران لتحويل الأقواس. إنه, أول تحويل مخروط, ومن ثم تحويل القوس. لكن, تجدر الإشارة إلى أنه إذا لم يتم تحديد نقطة البداية ونقطة النهاية للمخروط بشكل جيد, قد يتلف سطح المخروط, أو قد يكون الهامش كبيرًا جدًا. تظهر طريقة التحديد في الشكل 2-4. قم بتوصيل OC لتقاطع القوس عند D, وجعل المماس AB للقوس عبر النقطة D.
من العلاقة الهندسية CD=OC-OD= -R=0.414R, هذا هو الحد الأقصى المسموح به للقطع عند الدوران المستدق, إنه, عندما تتحول تفتق, لا يمكن أن يتجاوز مسار المعالجة خط AB. حسب العلاقة الموضحة في الشكل, ويمكن الحصول على AC=BC=0.586R, بحيث يمكن تحديد نقطة البداية ونقطة النهاية للمخروط. عندما لا يكون R كبيرًا جدًا, يمكن أخذ AC=BC=0.5R. الحساب العددي لهذه الطريقة معقد, ومسار القطع للأداة قصير.
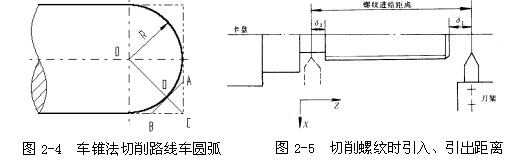
تحويل القوس بمسار القطع بطريقة مخروط الدوران
3. تحليل مسافة التغذية المحورية عند تدوير الخيط
عند تحويل الخيط, يجب أن تحافظ تغذية الأداة على طول اتجاه الخيط على علاقة صارمة لنسبة السرعة مع دوران مغزل قطعة العمل. مع الأخذ في الاعتبار أن الأداة تصل إلى معدل التغذية المحدد من حالة التوقف أو تنخفض من معدل التغذية المحدد إلى الصفر, يجب أن يكون لنظام القيادة عملية انتقالية. طول مسار المعالجة على طول التغذية المحورية, بالإضافة إلى ضمان طول الخيط, يجب أيضًا زيادة مسافة إدخال الأداة بمقدار δ1 (2~ 5 ملم) ومسافة قطع الأداة δ2 (1~ 2 مم), كما هو مبين في الشكل 2-5 . هذا للتأكد من أنه عند قطع المواضيع, ستتصل الأداة بقطعة العمل بعد اكتمال زيادة السرعة, وسوف تتباطأ الأداة بعد مغادرة قطعة العمل.
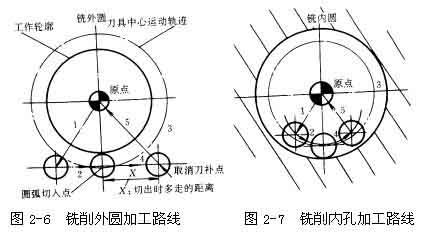
مسار المعالجة للدائرة الخارجية للجزء المطحون
4. تحليل مسار معالجة الطحن الكنتوري
لخطوط الطحن المستمر, خاصة عند معالجة الأقواس, انتبه إلى ترتيب القطع داخل وخارج الأداة, وحاول تجنب المعالجة المتكررة عند التقاطع, وإلا ستكون هناك علامات طحن حدودية واضحة. كما هو مبين في الشكل 2-6, عند استخدام الاستيفاء الدائري لطحن دائرة خارجية, ترتيب القاطع للدخول في عملية الطحن المحيطي من الاتجاه العرضي. بعد معالجة الدائرة بأكملها, لا تسحب الأداة مباشرة عند نقطة الظل, ولكن دع الأداة تتحرك مسافة معينة. من الأفضل اتباع الاتجاه العرضي لتجنب الاصطدام بين الأداة وسطح قطعة العمل عند إلغاء تعويض الأداة, مما تسبب في إلغاء قطعة العمل. عند طحن الأقواس الداخلية, وينبغي أيضًا مراعاة مبدأ القطع من الاتجاه العرضي, وينبغي ترتيب الأقواس الانتقالية بحيث يتم قطعها وقطعها, كما هو مبين في الشكل 3-7. إذا بدأت الأداة من أصل إحداثيات قطعة العمل, مسار المعالجة هو 1 → 2 → 3 → 4 → 5, وذلك لتحسين دقة المعالجة وجودة سطح الثقب الداخلي.
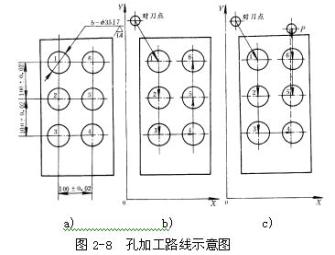
تصميم مسار ثقب الجزء بالقطع
5. تحليل مسار تصنيع الثقب بدقة موضعية عالية
لتصنيع الثقب الذي يتطلب دقة عالية في دقة الموضع, ينبغي إيلاء اهتمام خاص لترتيب تسلسل معالجة الثقب. قد يؤدي الترتيب غير المناسب إلى حدوث رد فعل عكسي على طول محور الإحداثيات ويؤثر بشكل مباشر على دقة الموضع. كما هو مبين في الشكل 2-8, الشكل أ هو رسم جزئي. هناك طريقتان للمعالجة لستة ثقوب من نفس الحجم تتم معالجتها في هذا الجزء. عند المعالجة وفقًا للمسار الموضح في الشكل ب, اتجاه تحديد المواقع من الثقوب 5 و 6 عكس ذلك من الثقوب 1, 2, 3 و 4. سيؤدي الخلوص العكسي في الاتجاه Y إلى زيادة خطأ تحديد الموقع ويؤثر على دقة موضع الثقوب 5 و 6 وغيرها من الثقوب. حسب المسار الموضح في الشكل ج, بعد المعالجة 4 الثقوب, انتقل لأعلى مسافة إلى النقطة P, ومن ثم العودة إلى العملية 5 و 6 الثقوب. في هذا الطريق, الاتجاه ثابت, والتي يمكن أن تتجنب إدخال رد فعل عنيف وتحسين دقة موضع الثقوب 5 و 6 وغيرها من الثقوب.
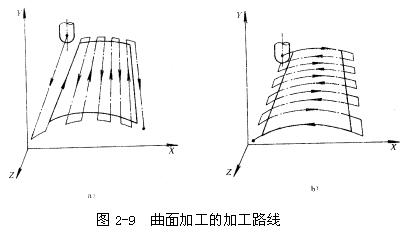
تصميم مسار المعالجة لسطح الجزء
6. تحليل مسار المعالجة لسطح الطحن
عند طحن سطح منحني, يشيع استخدام سكين ذو نهاية كروية للمعالجة باستخدام السكين “طريقة قطع الأسلاك”. إن ما يسمى بطريقة قطع الأسلاك يعني أن المسار المماس للأداة وكفاف الجزء يكون سطرًا تلو الآخر, ويتم تحديد المسافة بين الخطوط وفقًا لمتطلبات دقة تصنيع الجزء. لمعالجة الأسطح ذات الحدود المفتوحة, يمكن استخدام طريقتين بالقطع. كما هو مبين في الشكل 2-9, لشفرات المحرك الكبيرة, عند استخدام مخطط المعالجة في الشكل 2-9أ. في كل مرة تتم معالجتها على طول خط مستقيم, حساب نقطة موضع الأداة بسيط, البرنامج قليل, تتوافق عملية المعالجة مع تكوين السطح المسطر, ويمكن ضمان استقامة الحافلة بدقة. عند استخدام خطة المعالجة الموضحة في الشكل 2-9ب, تتوافق بيانات هذا النوع من الأجزاء مع المعلومات المقدمة لسهولة الفحص بعد المعالجة. دقة شكل المكره عالية, ولكن هناك العديد من الإجراءات. لأن حدود الجزء السطحي مفتوحة, لا توجد قيود سطحية أخرى, لذلك يمكن تمديد حدود السطح, ويجب أن تبدأ السكين ذات النهاية الكروية في المعالجة من خارج الحدود.
لقد قام ما سبق بتحليل طرق المعالجة الشائعة الاستخدام في التصنيع باستخدام الحاسب الآلي من خلال عدة أمثلة. في الإنتاج الفعلي, يجب أن يعتمد تحديد مسار المعالجة على الخصائص الهيكلية المحددة للأجزاء, النظر الشامل والاستخدام المرن. المبادئ العامة لتحديد مسار المعالجة هي: بشرط ضمان دقة المعالجة وجودة سطح الأجزاء, تقصير مسار المعالجة قدر الإمكان لتحسين الإنتاجية.