تظهر الخطوط المعقدة في تصنيع الأدوات والعفن, وهي منتجات منتجة بكميات كبيرة. قبل ظهور أدوات آلة CNC, تم تصنيع قوالب وقوالب الحدادة المستخدمة في صناعة السيارات يدويًا بشكل أساسي. بعد السبعينيات, لقد تم استخدام أدوات آلة CNC على نطاق واسع في تصنيع الأدوات والقوالب. عادة ما تتم معالجة الخطوط الأساسية للمقاطع المعقدة عن طريق الطحن, ويتم ضبط أدوات آلة CNC المحيطة في البداية على رابط ثلاثي المحاور.
بعد دخول الثمانينات, لقد تم استخدام آلات الطحن ذات خمسة محاور على نطاق واسع في معالجة الأسطح المعقدة. إن محيط قطعة العمل بعد الطحن قريب جدًا من الشكل النهائي لقطعة العمل, لكن عملية التشطيب الأخيرة لا تزال يدوية. في أواخر الثمانينات, تم تطوير ونضج تكنولوجيا القطع عالية السرعة تدريجياً, وقد تم تحسين تطبيقه في الإنتاج الصناعي بشكل مستمر من حيث الأدوات الآلية, أدوات القطع والتقنيات الأخرى ذات الصلة. نظرًا لأن القطع عالي السرعة يمكن أن يضاعف سرعة التغذية, يمكن تقليل درجة التغذية دون تقليل كفاءة الإنتاج. وهذا يوفر شرطًا أساسيًا لتحسين دقة شكل قطعة العمل وتقليل خشونة السطح. في الوقت الحالي, لم تعد معظم قطع العمل التي تتم معالجتها بواسطة الطحن عالي السرعة بحاجة إلى إجراء المعالجة اليدوية الأخير, ولكن يمكن وضعها موضع الاستخدام مباشرة.
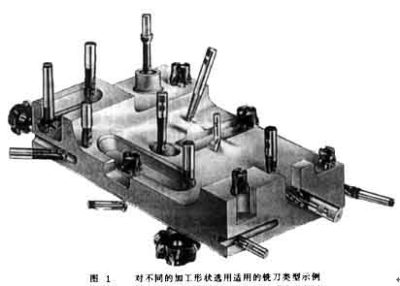
5-المعالجة المحورية للملامح المعقدة
مواد أداة جديدة: مثل السيراميك القائم على الألومينا, السيراميك القائم على نيتريد السيليكون, سيرميت, كربيد الأسمنت, وخاصة التطوير المستمر للطلاءات فائقة الصلابة, مما يجعل طحن الوجه الصلب ممكنًا. يمكن طحن سطح القالب لتشكيله بعد التبريد, وبالتالي تجنب التشوه الناتج عن التبريد بعد الطحن. هذا لا يبسط عملية التصنيع فقط, ولكن أيضًا يحسن دقة قطعة العمل.
فضلاً عن ذلك, مع تطبيق الدقة في تصنيع القوالب, القالب الفارغ بعد التزوير له بالفعل شكله الأساسي المصمم, and the remaining machining allowance is insignificant compared with the milling of the entire blank. في هذه الحالة, in addition to milling, it can also be processed by high-efficiency grinding. Compared with hard face milling, high-efficiency grinding can not only improve the shape accuracy of the workpiece, but also improve the surface roughness of the workpiece. There are many high-efficiency grinding methods, usually high-speed grinding with spherical grinding wheels and belt grinding with small-diameter belt wheels.
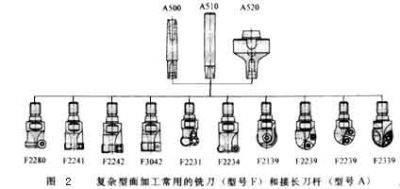
نوع قطع الطحن
Three-dimensional free-form surfaces in tools and molds are usually processed on a 5-axis machining center. Since the material of the workpiece is mostly alloy steel or tool steel, يجب أن يأخذ هيكل الآلة ونظام التحكم العددي في الاعتبار متطلبات الإنتاجية ودقة قطعة العمل في عملية المعالجة, وإجراء التخطيط والتحسين المناسبين بناءً على ذلك. من أجل ضمان أن أداة الآلة لا تتعرض للكثير من التشوه عند قطع مواد القالب المختلفة, يجب أن تكون صلابة أداة الماكينة هي الأولوية الأولى عند تحديد تصميم الماكينة. مركز تصنيع المحور الأكبر, معظم هيكل العملاقة, يتم أيضًا استخدام بعض مراكز المعالجة ذات خمسة محاور صغيرة الحجم في بعض الأحيان هيكل عمود مرتفع.
منذ بداية التسعينيات, تمت معالجة جميع الأشكال المعقدة تقريبًا عن طريق القطع عالي السرعة في الإنتاج. والغرض من ذلك هو تحسين كفاءة الإنتاج, تقليل تكلفة المنتج, وفي نفس الوقت تحسين دقة شكل قطعة العمل وتقليل خشونة السطح. من أجل تلبية احتياجات القطع عالية السرعة, يستخدم مغزل الآلة الآلية تقريبًا دون استثناء مغزلًا كهربائيًا. تتغير سرعة المغزل بشكل مستمر وفقًا لقطر الأداة المستخدمة, وتتراوح السرعة من عدة آلاف من الدورات في الدقيقة إلى عشرات الآلاف من الدورات في الدقيقة. يختلف نظام القيادة للطاولة المنزلقة أيضًا عن مراكز المعالجة التقليدية في القطع عالي السرعة. نظام شائع الاستخدام مع مجموعة لولبية ذات محرك عالي السرعة ومحرك خطي, يمكن أن تصل سرعة التغذية القصوى إلى 100 متر / دقيقة أو أكثر.
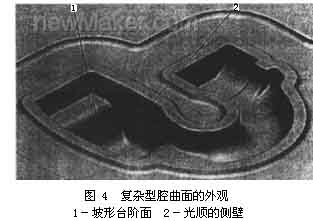
رسم مظهر سطح التجويف المعقد بالتصنيع باستخدام الحاسب الآلي
عند معالجة الأسطح المعقدة, يجب أن يلبي نظام CNC الخاص بالأداة الآلية أيضًا بعض المتطلبات الخاصة. على سبيل المثال, يتم إنشاء برامج التصنيع باستخدام الحاسب الآلي للأسطح المعقدة بشكل عام على برنامج CAD/CAM. غالبًا ما يتطلب البرنامج التعريفي عدة ميغابايت (بايت) من مساحة التخزين, ولم يعد من الممكن نقل برامج NC باستخدام قرص مرن. لذلك, يجب أن يتمتع نظام CNC بوظيفة التواصل مع أنظمة الكمبيوتر الأخرى حتى يتمكن من استقبال برنامج CNC مباشرة من CAD/CAM. فضلاً عن ذلك, يجب أن يعتمد نظام التحكم العددي أيضًا تكنولوجيا التحكم المتقدمة, أولاً, فهو يتطلب وظيفة LookAhead. بعبارة أخرى, قبل أن تقوم الآلة الآلية بمعالجة مسار معين, يقوم نظام البيانات بتحليل السطح المراد معالجته مسبقًا. According to the curvature of each point of the curved surface and the connection relationship of each adjacent point, the feed speed of the machine tool is appropriately adjusted to achieve the highest productivity under the premise of ensuring the accuracy of the workpiece. In order to reduce dynamic errors during processing, the new servo error correcting data using a conventional tandem system is no longer proportional integral derivative (معرف المنتج) controller, instead of using the state regulator by compensating for the position and speed state parameters. Using this kind of regulator can completely eliminate the drive hysteresis error, تعويض الخطأ غير الخطي الناتج عن الفجوة أو الاحتكاك, وحتى تعويض اهتزازات معينة للأداة الآلية. وذلك لتلبية متطلبات تحسين دقة شكل قطعة العمل وتقليل خشونة السطح.
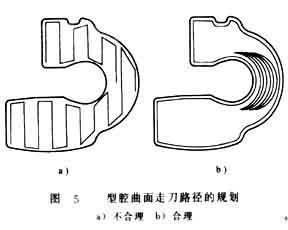
تحديد مسار القطع لسطح التجويف
يلعب نظام الأداة دورًا حاسمًا في كفاءة الإنتاج وجودة المعالجة عند معالجة الملفات الشخصية المعقدة. عند اختيار نظام أداة القطع, يجب علينا أولاً أن نبدأ من هندسة الأجزاء المراد معالجتها, واستخدام أنواع أدوات القطع بشكل معقول. كما هو مبين في الشكل 1, هندسة كل جزء مختلفة جدا. إذا تم استخدام قاطعة الطحن ذات نهاية الكرة فقط للمعالجة, يجب اختيار قاطعة طحن ذات نهاية كروية ذات قطر صغير, مما يجعل من الصعب تحسين كفاءة المعالجة. فضلاً عن ذلك, نصف قطر القوس لبعض الأجزاء صغير جدًا بحيث لا يمكن معالجته حتى باستخدام مطحنة نهاية كروية صغيرة. لذلك, مع الأخذ في الاعتبار متطلبات كل من كفاءة الإنتاج وشكل قطعة العمل, يجب أن تكون الأنواع الأخرى من قواطع الطحن مجهزة بمركز المعالجة خماسي المحاور لمعالجة المقاطع المعقدة, مثل المطاحن النهائية وقواطع الطحن ثلاثية الوجه.
شكل 2 يعرض بعض أنواع قواطع الطحن. طالما أن الحجم يسمح بذلك, بغض النظر عن شكل الأداة, يجب أن تكون حافة القطع عبارة عن أداة طحن بمشبك قابل للتحويل. يمكن الجمع بين هذه السكاكين بعدة طرق بسبب النصل والجسم, ويمكن إنتاج الشفرة والجسم بواسطة شركات مختلفة. لذلك, يمكن تشكيل إنتاج متخصص على نطاق واسع, مما لا يساعد فقط على تحسين جودة الأداة, ولكنه يساعد أيضًا في تقليل تكلفة إنتاج الأداة.
حالياً, تستخدم معظم الشفرات القابلة للفهرسة المتوفرة في السوق شفرات كربيد مطلية بتقنية CVD. من أجل تحقيق مقاومة أعلى للتآكل الزائف, الإدخالات القابلة للفهرسة كلها عبارة عن طبقات متعددة الطبقات. يمكن لـ Bizhi Al2O3 تحسين الاستقرار الكيميائي للشفرة. يمكن لـ TiN وTiCN تعزيز مقاومة التآكل للشفرة. من أجل تعزيز حدة النصل, بالإضافة إلى طريقة الأمراض القلبية الوعائية ذات درجة الحرارة المنخفضة, ويمكن أيضًا إنتاج الطلاء بطريقة PVD. بعض المعالجة لها متطلبات صارمة للغاية على الشفرة. يجب أن يكون للشفرة حافة قطع حادة لتقليل خشونة السطح النهائي, ولكن لديها أيضًا مقاومة عالية للتآكل لضمان دقة شكل قطعة العمل. في هذه الحالة, يجب استخدام مزيج من الطلاءات المتعددة. من أجل التأكد من أن استخدام بعض الشفرات مضمون, يمكن أن يصل عدد طبقات الطلاء إلى 100.
يرتبط عمر الأداة ارتباطًا وثيقًا بمعدل التغذية, سرعة القطع وعمق القطع. غالبًا ما تكون كمية القطع المثالية عبارة عن نطاق صغير, والتي يجب تحديدها وفقًا للأداة المحددة ومواد الشغل.
فضلاً عن ذلك, استراتيجيات القطع مثل: تخطيط مسار الأداة, المتجه الطبيعي لسطح محور الأداة (الاتجاه الطبيعي للسطح عند هذه النقطة) أو الطرق المختلفة على طول ناقل الظل السطحي (الاتجاه المماس للسطح عند هذه النقطة), إلخ., هي أيضًا عامل رئيسي في معالجة الأسطح المعقدة . إنه لا يؤثر فقط على خشونة سطح قطعة العمل المعالجة, ولكنه يؤثر أيضًا على شكل قطعة العمل ودقة أبعادها. شكل 3 يوضح استراتيجيات القطع المختلفة المستخدمة عند تصنيع سطح أسطواني. للقطع في الاتجاه المحيطي, يجب أن يتم استكمال مسار الأداة في رابط ثنائي المحور. عند القطع على طول اتجاه المولد, تحتاج الأداة فقط إلى إجراء استيفاء أحادي المحور. فضلاً عن ذلك, طرق القطع المختلفة لها اختلافات كبيرة في تآكل الأداة. إن تآكل الأداة أثناء الطحن السفلي أقل بكثير من تآكل الأداة أثناء الطحن العلوي, ويكون التآكل أثناء الطحن الترددي أكبر بكثير من التآكل في الطحن أحادي الاتجاه.
من أجل تحسين استقرار عملية المعالجة, عند تحسين استراتيجية القطع, ويجب ضمان استمرارية القطع, ويجب تقليل حركة القطع والسكتة الدماغية الخاملة قدر الإمكان من أجل تقصير وقت القطع. عند الطحن الخام للصلب, يجب ضمان الطحن المستمر للتسلق, لتقليل ذروة شفرة القطع أثناء قطع كمية التقلب.
عند معالجة قطعة العمل الموضحة في الشكل 4, إذا تم استخدام معالجة قسم مسار قطع الصف الموضح في الشكل 5أ; حركة الأداة غير معقولة للغاية, ظروف القطع غير مرضية للغاية, وقت المعالجة 33 دقيقة, وخشونة السطح لقطعة العمل هي 6-9μm. إذا قمت بالتبديل إلى مسار قطع الدائرة الموضح في الشكل 5ب للمعالجة, وقت المعالجة على وشك 27 دقائق. في نفس الوقت, يمكن أيضًا تقليل خشونة قطعة العمل إلى 2 ~ 4 ميكرومتر.