تسمى فتحات التصنيع باستخدام الحاسب الآلي في الجزء الصلب من قطعة العمل باستخدام المثقاب بالحفر. الحفر هو بالقطع الخام, درجة تحمل الأبعاد التي يمكن تحقيقها هي IT13~IT11, وقيمة خشونة السطح هي Ra50~12.5μm. بسبب طول المثقاب الملتوي, القطر الأساسي الصغير والصلابة الضعيفة, وكذلك تأثير حافة الإزميل, الحفر لديه الخصائص التكنولوجية التالية:
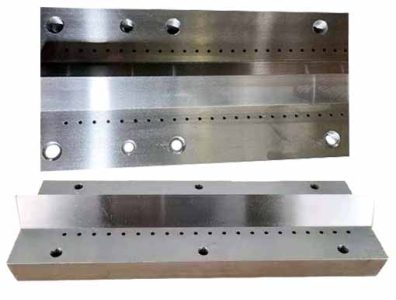
CNC Drilling of Micro Holes in Melt Blown Cloth Mold
1. The drill bit is easily deflected. Due to the inaccurate centering effect of the chisel edge of the drill, the drill is easy to deflect when cutting in; فضلاً عن ذلك, the rigidity and guiding effect of the drill bit are poor, and the drill bit is easy to bend during cutting. When drilling on a 3-axis machine tool, as shown in Figure 7-2a, it is easy to cause the axis of the hole to be offset and not straight, but the diameter of the hole does not change significantly; When drilling a hole on a lathe, as shown in Figure 7-2b, it is easy to cause a change in the hole diameter, but the axis of the hole is still straight. لذلك, the end face should be processed before drilling, and a taper pit should be pre-drilled with a drill or a center drill, كما هو مبين في الشكل 7-3, so that the drill can be centered. When drilling small holes and deep holes, in order to avoid the deviation and non-straightness of the axis of the hole, the workpiece rotation method should be used for drilling as much as possible.
2. The aperture is easy to expand. When drilling, the unequal radial forces of the two cutting edges of the drill will cause the hole diameter to expand; The lead-in deviation when drilling a horizontal lathe is also an important reason for the enlargement of the aperture; فضلاً عن ذلك, the radial runout of the drill bit is also the cause of the enlargement of the hole diameter.
3. The surface quality of the hole is poor. The drilled chips are wide and are forced to spiral in the hole. When the chips flow out, they rub against the hole wall and scratch the machined surface.
4. Large axial force during drilling. This is mainly caused by the chisel edge of the drill. Tests have shown that 50% of the axial force and 15% of the torque when drilling is generated by the chisel edge. لذلك, when the drilling diameter is d>30مم, the drilling is generally carried out in two times. Drill (0.5~0.7)d for the first time, and drill to the required hole diameter for the second time. Since the chisel edge does not participate in cutting for the second time, a larger feed can be used to improve the surface quality and productivity of the hole.
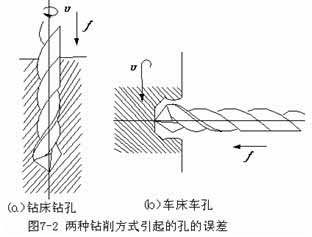
Comparison of drilling holes on a drilling machine and turning holes on a lathe