Product Categories
Product Tags
The difference between automatic lathe and CNC lathe machining
Different metal nuts processed by automatic lathe
Our company provides automatic lathe processing of various nuts, including but not limited to the insert nuts for injection molding as shown in the left picture. There are a large number of examples of this product in other directories on this website:
It also includes hexagonal and thin copper nuts, non-standard special nuts, etc. The process of turning various nut parts on automatic lathes.
During the operation of the automatic lathe, the tool and frame move and process simultaneously. This is very different from CNC lathe processing or machining center. The turrets of CNC lathes or machining centers are processed in turn. Some of the more high-end multi-axis linkage CNC lathes can process two positions at the same time, and the price is very high, and it is not true synchronous processing.
Automatic lathe processing is like "group fight", and CNC lathe processing is like "wheel battle". This analogy is not very good, as long as you understand the meaning.
For the purpose of shooting, this is the processing image of stopping the fuel injection and reducing the speed, 6 seconds per frame. The processed product is such a nut:
For suitable parts such as small shaft pins, small nuts, etc., the processing efficiency of automatic lathes is 10000PCS/per shift (calculated by 10 hours) is not difficult, which is unimaginable for CNC lathes
2. Cost.
On the one hand, as mentioned above, the improvement of efficiency means the reduction of cost;
On the other hand, the price of the equipment itself is not high and the depreciation cost is low, so in general, the unit price of products processed by automatic lathes is often very cheap. (Of course, the cheapness mentioned here refers to our company's product quotation guidelines, I don't know whether other manufacturers are cheaper)
3. Precision.
Dimensional accuracy, surface finish, concentricity, etc., are in fact not lower than CNC lathes, unless they are not suitable for products processed by automatic lathes.
4. Automatic lathes almost integrate the advantages of CNC lathes, cold forging machines, and ordinary lathes, and the product cost seems to be closer to that of cold forging. This is also the reason why automatic lathe processing has flourished in China in recent years.
What products can automatic lathes do?There are many types of products that can be processed by automatic lathes. In addition to the products displayed on this page and the general products in other catalogs on this website, it can also process professional parts in various industries. For example, various small parts in the connector industry, riveting parts in the cabinet industry, and various professional parts and components used in electronics, sheet metal, communications, and automobiles can all be produced.
The maximum outer diameter is within 32MM, and the materials include but are not limited to: stainless steel, copper, easy-car iron, aluminum, titanium alloy
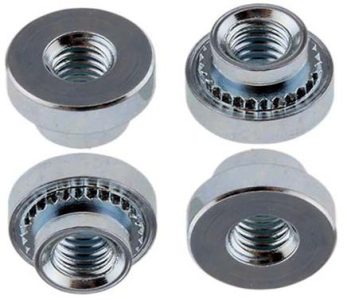
Nuts processed by automatic lathes
Different metal nuts processed by automatic lathe
Our company provides automatic lathe processing of various nuts, including but not limited to the insert nuts for injection molding as shown in the left picture. There are a large number of examples of this product in other directories on this website:
It also includes hexagonal and thin copper nuts, non-standard special nuts, etc. The process of turning various nut parts on automatic lathes.
Contact Us
Waiting for your email, we will reply you within 12 hours with valuable information you needed.